впускной клапан |
выпускной клапан | |
Наружный диаметр седла клапана, мм |
37,2 |
32,4 |
Ширина рабочей фаски, мм |
2,0 |
2,4 |
Заглубление плоскости седла относительно плоскости головки блока, мм |
9,2 |
9,7 |
Угол фаски, град |
45 |
45 |
Угол верхнего конуса, град |
30 |
30 |
Диаметр отверстия в направляющих втулках клапанов, мм |
8,013 – 8,035 |
8,013 – 8,035 |
Предельно допустимый зазор между стержнем клапана и направляющей втулкой, мм |
1,0 |
1,3 |
Диаметр тарелки клапана, мм |
28,0 |
33,0 |
Диаметр стержня клапана, мм |
7,97 |
7,95 |
Максимальная допустимая при шлифовке ширина рабочей фаски, мм |
3,5 |
шлифовке не подлежит |
Минимальная высота тарелки клапана до фаски, мм |
0,5 |
шлифовке не подлежит |
Длина клапана, мм: | ||
– номинальная |
98,7 (91,0 для двигателя NP) |
98,5 (90,8 для двигателя NP) |
– минимальная |
98,2 (90,5 для двигателя NP) |
98,0 (90,3 для двигателя NP) |
45 |
45 | |
Зазор между кулачками распределительного вала и регулировочными шайбами толкателей клапанов, мм: | ||
– при температуре охлаждающей жидкости 35° С |
0,25 ± 0,05 |
0,45 ± 0,05 |
– при температуре охлаждающей жидкости 20° С |
0,20 ± 0,05 |
0,40 ± 0,05 |
Зазор между поршнем и цилиндром двигателя, мм |
0,03 | |
Максимально допустимый зазор между поршнем и цилиндром, мм |
0,08 | |
Диаметр цилиндров, мм: | ||
– номинальный |
81,01 | |
– 1-й ремонтный |
81,26 | |
– 2-й ремонтный |
81,51 | |
– 3-й ремонтный |
82,01 | |
Диаметр шеек коленчатого вала, мм: |
коренных |
шатунных |
– номинальный |
54,0-0,022 -0,042 |
47,8-0,022 -0,042 |
– 1-й ремонтный |
53,75-0,022 -0,042 |
47,55-0,022 -0,042 |
– 2-й ремонтный |
53,5-0,022 -0,042 |
47,3-0,022 -0,042 |
– 3-й ремонтный |
53,2-0,022 -0,042 |
47,05-0,022 -0,042 |
Диаметр вкладышей подшипников, мм: | ||
– номинальный |
53,96 – 53,98 |
47,76 – 47,79 |
– 1-й ремонтный |
53,71 – 53,73 |
47,51 – 47,53 |
– 2-й ремонтный |
53,46 – 53,48 |
47,26 – 47,29 |
– 3-й ремонтный |
|
47,01 – 47,03 |
Максимальная допустимая овальность, мм |
0,03 | |
Осевой зазор коленчатого вала, мм: | ||
– номинальный |
0,07 – 0,17 | |
– максимальный допустимый |
0,25 | |
Зазор между коренными вкладышами и шейками коленчатого вала, мм: | ||
– номинальный |
| |
– предельно допустимый |
0,17 | |
Диаметр поршня, мм: | ||
– номинальный |
80,98 | |
– 1-й ремонтный |
81,23 | |
– 2-й ремонтный |
81,48 | |
– 3-й ремонтный |
81,98 | |
Глубина выемки в головке поршня, мм |
|
DS, NP4,4 |
Длина поршневого пальца, мм |
57 (54 выпуска до июля 1985 г.) | |
Зазор в замке поршневых колец, мм: |
компрессионное |
маслосъемное |
– номинальный |
0,3 – 0,45 |
0,25 – 0,5 |
– предельно допустимый |
1,0 |
1,0 |
Зазор между кольцами и канавкой в поршне, мм: | ||
– номинальный |
0,02 – 0,05 |
– |
– предельно допустимый |
1,05 |
– |
Предельно допустимый зазор между шатунными вкладышами и шейками коленчатого вала, мм |
0,12 | |
Предельно допустимый осевой зазор шатуна на шейке коленчатого вала, мм |
0,37 | |
Предельно допустимый осевой зазор распределительного вала при снятых толкателях, мм |
0,15 | |
Радиальное биение шеек распределительного вала, мм, не более |
0,01 | |
Диаметр шеек распределительного вала, мм: | ||
– номинальный |
26,0 | |
– ремонтный |
25,75 | |
Минимальная высота головки блока, мм |
132,6 | |
Зазор между зубьями шестерен масляного насоса, мм: | ||
– номинальный |
0,05 | |
– предельно допустимый |
0,2 | |
Зазор между наружным диаметром шестерен и корпусом насоса, мм |
0,15 | |
впускной клапан |
выпускной клапан | |
Наружный диаметр седла клапана, мм |
37,2 |
30,8 |
Ширина рабочей фаски, мм |
2,0 |
2,0 |
Заглубление плоскости седла относительно плоскости головки блока, мм |
9,6 |
9,0 |
Угол фаски, град |
45 |
45 |
Угол верхнего конуса, град |
30 |
30 |
Диаметр отверстия в направляющих втулках клапанов, мм |
8,013 – 8,035 |
8,013 – 8,035 |
Предельно допустимый зазор между стержнем клапана и направляющей втулкой, мм |
1,0 |
1,3 |
Диаметр тарелки клапана, мм |
38,0 |
33,0 |
Диаметр стержня клапана, мм |
7,97 |
7,95 |
Максимальная допустимая при шлифовке ширина рабочей фаски, мм |
3,5 |
шлифовке не подлежит |
Минимальная высота тарелки клапана до фаски, мм |
0,5 |
шлифовке не подлежит |
Длина клапана, мм: | ||
– номинальная |
91,0 |
90,8 |
– минимальная |
90,05 |
90,3 |
Угол рабочей фаски клапана, град |
45 |
45 |
Зазор между кулачками распределительного вала и регулировочными шайбами толкателей клапанов, мм: | ||
– при температуре охлаждающей жидкости 35° С |
0,25 ± 0,05 |
0,45 ± 0,05 |
– при температуре охлаждающей жидкости 20° С |
0,20 ± 0,05 |
0,40 ± 0,05 |
Максимальный допустимый зазор между поршнем и цилиндром, мм |
0,07 | |
Диаметр цилиндра, мм: | ||
– двигатели 1,9 л и 2,2 л: | ||
номинальный |
79,51 | |
1-й ремонтный |
79,76 | |
2-й ремонтный |
80,01 | |
3-й ремонтный |
80,51 | |
– двигатели 2,0 л и 2,3 л: | ||
номинальный |
81,01 (82,51 для двиг. NF) | |
1-й ремонтный |
81,26 (82,76 для двиг. NF) | |
2-й ремонтный |
81,51 (83,01 для двиг. NF) | |
Диаметр вкладышей подшипников, мм: |
коренных |
шатунных |
– номинальный |
57,96 – 57,98 |
45,96 – 45,98 |
– 1-й ремонтный |
57,71 – 57,73 |
45,71 – 45,73 |
– 2-й ремонтный |
57,46 – 57,48 |
45,46 – 45,48 |
– 3-й ремонтный |
57,21 – 57,23 |
45,21 – 45,23 |
Осевой зазор коленчатого вала, мм: | ||
– номинальный |
0,07 – 0,18 (0,07 – 0,23 с 1984 г.) | |
– максимальный допустимый |
0,25 | |
Максимально допустимый зазор между коренными вкладышами и шейками коленчатого вала, мм |
0,16 | |
Диаметр поршня, мм: | ||
– двигатели 1,9 л и 2,2 л: | ||
номинальный |
79,48 | |
1-й ремонтный |
79,73 | |
2-й ремонтный |
79,98 | |
3-й ремонтный |
80,48 | |
– двигатели 2,0 л и 2,3 л: | ||
номинальный |
80,98 (82,48 для двиг. NF) | |
1-й ремонтный |
81,23 (82,74 для двиг. NF) | |
2-й ремонтный |
81,48 (82,98 для двиг. NF) | |
Зазор в замке поршневых колец, мм: | ||
– номинальный |
0,25 – 0,5 | |
– предельно допустимый |
1,0 | |
Зазор между кольцом и канавкой в поршне, мм: | ||
– номинальный |
0,02 – 0,08 | |
– предельно допустимый |
0,1 | |
Предельно допустимый зазор между шатунными вкладышами и шейками коленчатого вала, мм |
0,12 | |
Предельно допустимый осевой зазор шатуна на шейке коленчатого вала, мм |
0,4 | |
Предельно допустимый осевой зазор распределительного вала при снятых толкателях, мм |
0,15 | |
Минимальная высота головки блока (между поверхностями), мм |
132,75 |
Осмотр и дефектовка частей Наружная пружина: высота под нагрузкой 26,0+1,7 кгс высота под нагрузкой 46,2+2,4 кгс Внутренняя пружина: высота под нагрузкой 9,0+0,8 кгс высота под нагрузкой 27,5+1,5 кгс а – седло впускного клапана Величина зазоров между клапаном и направляющей втулкой, мм: номинальный промежуток для выпускных клапанов предельно допустимый промежуток для впускных и выпускных клапанов Если промежуток меньше предельно допустимого, попробуйте заменить клапан. Если промежуток преувеличивает предельно допустимый, подмените направляющую втулку.порядо. Осуществления 6. Дефекты рабочей фаски клапанов, которые невозможно вывести притиркой, можно прошлифофать на особом станке. При шлифовке стоит выдержать размеры, заданные на рисунке. В скобках даны отличающиеся размеры для двигателя Ваз-21083 (см. примечания).. 5. Исследуйте клапаны. Подмените клапаны со следующими дефектами: глубокие риски и царапины на рабочей фаске, трещины, деформация вала клапана, коробление тарелки клапана, последствия прогара. Неглубокие риски и царапины на рабочей фаске можно убрать притиркой клапанов. 9. Наиболее значительные дефекты седел клапанов устраняются шлифовкой. При шлифовке выдержите размеры, заданные на рисунке (см. замечание 1). Прежде шлифуется фаска под углом 20°, далее фаска под углом 45°. Дальше шлифовки стоит притереть клапаны, далее досконально расчистить и продуть сжатым воздухом головку блока, чтобы в каналах и камерах сгорания не осталось частиц абразива. В скобках даны отличающиеся размеры для двигателя Ваз-21083. 10. Измерьте промежуток между направляющими втулками и клапанами (см. замечание 2). Промежуток вычисляется как избыток между диаметром отверстия во втулке и диаметром вала клапана. 8. Измерьте положение седел клапанов. На рабочих фасках седел не должно быть следов износа, раковин и коррозии. Незначительные дефекты (мелкие риски, царапины и т.п.. можно убрать притиркой клапанов. 11. Исследуйте толкатели клапанов. Если на рабочей плоскости толкателя имеются задиры, царапины или другие повреждения, подмените толкатели. |
Диаметр седла клапана ваз 2108
Седло клапана — небольшое кольцо, имеющее скос по внутренней поверхности.
Устанавливается в отверстия головки блока цилиндров, предназначенные для установки клапанов и перегонки через них топливовоздушной смеси и отработавших газов. Деталь запрессовывается в ГБЦ на заводе.
Выполняет следующие функции:
- герметичность отверстия;
- передает излишки тепла к ГБЦ;
- обеспечивает необходимый приток воздуха, когда механизм открыт.
Замена седла клапана требуется в том случае, когда восстановить его герметичность способом механической обработки не удается (многочисленные обработки в прошлом, прогар, сильный износ). Сделать это можно своими руками.
Ремонт детали выполняют при:
- прогаре тарелки;
- после замены направляющих втулок;
- при умеренной степени естественного износа;
- при нарушении герметичности соединения кольца с тарелкой.
Правка изношенных и поврежденных седел в домашних условиях выполняется с использованием шарошек. Помимо этого, может потребоваться сварочный аппарат или мощная газовая горелка, стандартный набор гаечных ключей, необходимых для демонтажа и разборки ГБЦ, притирочная паста, дрель.
Замена седел
Процедура замены состоит из двух ответственных процедур: удаления старых деталей и монтажа новых.
Удаление старых посадочных элементов
Замена седел клапанов выполняется на демонтированной ГБЦ с разобранным газораспределительным механизмом. Удалить старое кольцо можно с использованием сварочного аппарата, если материал, из которого оно изготовлено, позволяет это сделать.
Для выполнения процедуры изготавливается съемник седел клапанов — берется старый ненужный клапан, тарелку которого необходимо проточить до размеров внутреннего диаметра седла.
После этого полученный инструмент утапливают в посадочное место, не доходя до края 2-3 мм и «прихватывают» сваркой в 2-3 местах. После клапан вместе с металлическим кольцом выбивают с обратной стороны молотком.
Важно! Процедура с использованием сварки может привести к некоторой деформации посадочного места. При этом стандартные седла будут иметь слабое закрепление, что может привести к их самопроизвольному демонтажу в процессе работы мотора. Требуются кольца увеличенного диаметра, которые не продаются в магазинах, а изготавливаются на заказ.
Седло клапана, изготовленное из металлов, не подлежащих сварке, можно удалить путем вкручивания в него отрезка трубы, используемого как съемник седел клапанов. Для этого на внутренней поверхности кольца нарезается резьба. Аналогичную резьбу наносят на внешнюю поверхность подходящей по диаметру металлической трубы.
Берется старый клапан, который предварительно приваривают к торцу трубы в обратной положении. При этом ножка клапана проводится в предназначенное для нее отверстие, труба вкручивается в резьбу, после чего элемент удаляют постукиваниями по ножке.
Монтаж новых седел
Перед началом процедуры монтажа новых седел, посадочные места под них очищают от загрязнений. После ГБЦ следует равномерно нагреть до температуры, превышающей 100˚С. При этом металл расширяется, позволяя запрессовать кольцо.
Монтируемую деталь охлаждают с помощью жидкого азота. При его отсутствии можно использовать сочетание льда и ацетона, что позволяет снизить температуру металла до -70˚С. Размеры деталей подбирают таким образом, чтобы разница между диаметром посадочного места и кольца составляла не более 0.05-0.09 мм на холодных деталях.
Седло клапана запрессовывается с помощью специальной оправки или отрезка трубы подходящего диаметра. Деталь должна входить на посадочное место с небольшим усилием. При этом важно, чтобы кольцо встало без перекоса.
После запрессовки и остывания ГБЦ следует проверить, не болтается ли элемент на посадочном месте. Если зазор отсутствует, а замененный элемент плотно держится на своем месте, процедуру его замены можно считать оконченной. Далее требуется прирезка седел клапанов с использованием шарошек.
Важно! При стандартной процедуре замены тарелки всех клапанов оказываются посажены достаточно высоко. Однако некоторые специалисты рекомендуют обрабатывать фаски таким образом, чтобы выпускные клапаны сидели несколько глубже нормального положения. Седло впускного клапана при этом оставляют в штатном положении.
Ремонт седел
Ремонт седел клапанов выполняется при их естественном износе и неплотном прилегании тарелки к своему посадочному месту.
С целью восстановления геометрии колец применяются шарошки для седел клапанов — набор фрезерующих головок, позволяющих делать необходимые углы.
Шарошки могут использоваться в сочетании со специальным оборудованием. Однако оно является дорогостоящим. Поэтому в домашних условиях применяют ключ-трещотку с удлинителем. Правильно обработанные места имеют углы 30˚, 60˚ и 45˚. Обработка седел клапанов для создания каждого из них производится соответствующей фрезой.
Шлифовка седел клапанов не требует их нагрева или другой обработки. Проточку производят «насухую». В дальнейшем, в момент притирки, необходимо использовать специальную притирочную пасту. Для достижения лучшего результата притирку на новые седла рекомендуется производить вручную, а не с помощью дрели.
Еще одной разновидностью ремонта является проточка посадочных мест под ремонтные вставки. Для этого по вышеописанному алгоритму удаляют седла, после чего, специальным режущим инструментом протачивают места под них. Размер ремонтного места должен быть на 0.01-0.02 см меньше вставки. Монтаж производят после нагрева ГБЦ и охлаждение монтируемых элементов.
Правильно произвести расточку самостоятельно можно попытаться на свой страх и риск. Однако, с учетом сложности процедуры и необходимой высокой точности работ, подобные манипуляции лучше производить в условиях квалифицированной автомастерской или авторемонтного завода.
Если подшипники распределительного вала разбиты, то можно установить восстановленную головку блока. В этом случае не нужно проводить никаких работ на седлах клапанов.
Проверить все седла клапанов на наличие следов износа или образование зазубрин. Небольшие следы износа можно удалить 45-градусной фрезой. Если седло выработано уже слишком глубоко, то нужно заменить кольца седел клапанов.
Кольца седел клапанов запрессованы в головку блока цилиндров, и старое кольцо лучше удалить, высверлив его или вывернуть его с помощью приспособления для обработки седел клапанов. При этом нужно обязательно следить за тем, чтобы не повредить головку блока цилиндров. Основное отверстие (D1) нужно измерить и, если нужно, развернуть до следующего ремонтного размера. Разворачивать кольца седел клапанов ремонтных размеров до тех пор, пока не будет достигнуто перекрытие в 0,068 — 0,10 мм. Кольца седел клапанов для впускных клапанов больше по диаметру.
Размеры колец седел клапанов
D. Наружный диаметр кольца седла клапана;
D1. Внутренний диаметр кольца седла клапана;
D2. Посадочное отверстие в головке цилиндров;
Н. Высота кольца седла клапана;
Т. Расстояние между поверхностью головки и верхней стороной кольца седла клапана. D=40,100-40,084 мм для впускного клапана, 37,100-37,084 мм для впускного клапана; D2=40,000-40,016 мм для впускного клапана, 37,000-37,016 мм для выпускного клапана; Н=6,97-7,00 мм для всех клапанов;
Т=2,37-2,25 мм для впускных клапанов, 2,44-2,25 для выпускных клапанов.
Нагреть головку блока цилиндров в водяной бане примерно до 90°С, а кольцо седла клапана охладить с помощью сухого льда. Вбить кольцо седла клапана подходящим стержнем. Произвести обработку кольца седла клапана с помощью специального приспособления или с помощью шлифовальной машинки. Используя клапан, измерить расстояние (А). Оно должно составлять на новом клапане и новом кольце седла клапана 0,1-0,5 мм. Граница износа составляет 1,0 мм.
После обработки измерить ширину седла клапана. Если она у впускных клапанов не составляет 2,5 мм и у выпускных — 3,5 мм, то необходимо обработать седло вверху 15-градусной фрезой, а внизу — 60-градусной фрезой.
Фрезерные работы нужно закончить, когда седло будет иметь нужную ширину. Обработанные седла клапанов нужно притереть. Для этого смазать поверхность седла клапана шлифовальной пастой и вставить клапан в соответствующее седло. Зажать стержень клапана подходящим способом и вращать клапан туда-сюда. Постепенно проворачивать клапан на четверть оборота и затем снова притирать его. При необходимости добавить шлифовальной пасты.
После притирки тщательно очистить все детали от грязи и шлифовальной пасты и проверить прилегание клапана к седлу. На обеих деталях должно быть видно непрерывное матовое кольцо которое дает ширину седла клапана. С помощью карандаша нанести несколько штрихов на кольце тарелки клапана, чтобы расстояние между ними было около 1,0 мм. После этого дать клапану упасть в направляющую и на седло и повернуть клапан на 90°, приложив к нему небольшое усилие.
Вынуть клапан и проверить, удалены ли карандашные штрихи на кольце седла. Если ширина седел клапанов находится в нужных пределах, то можно устанавливать головку. В противном случае доработать седла клапанов или, в крайнем случае, установить реставрированную головку. В этом случае переставить старые детали на новую головку.
Клапаны
Из-за использования гидравлических уравнительных элементов для регулировки клапанного зазора концы стержней впускных и выпускных клапанов должны специально проверяться, чтобы поддерживать высокую эффективность их работы.
Небольшие повреждения поверхности тарелки клапана можно устранить притиркой клапанов в седлах в головке блока цилиндров, как описано выше. Если клапаны на уплотняемых поверхностях выглядят небезупречно, то их можно перешлифовать в шлифовальной машинке. У притертого и перешлифованного клапана, который находится в хорошем состоянии, толщина кромки тарелки клапана должна составлять у впускных клапанов 0,5 — 0,7 мм и у выпускных 0,5 — 0,6 мм.
Клапаны заполнены натрием, как и у других двигателей фирмы Mercedes.
Измерить клапаны. Размеры должны соответствовать размерам, приведенным в таблице. Заменить все клапаны, не удовлетворяющие данному условию.
диаметр тарелки клапана (D) мм | диаметр стержня клапана (D1) мм | длина клапана (L) мм | |
Впускной клапан | 38,60 | 7,97 | 106,4 |
Выпускной клапан | 35,0 | 8,96 | 106,4 |
При приобретении клапанов нужно всегда сообщать, что они используются на дизельном двигателе, и какие клапаны требуются впускные или выпускные. Иногда возможно заменить только впускные клапаны, когда они, к примеру, обгорели по краям.
Головка блока цилиндров
Тщательно очистить поверхности головки и блока цилиндров и проверить поверхность головки на деформацию. Для этого приложить линейку к головке и проверить с помощью плоского щупа зазор между линейкой и поверхностью головки в продольном, поперечном и в диагональном направлениях. Если возможно вдвинуть щуп толщиной более 0,1 мм при измерениях в продольном направлении, то следует перешлифовать головку в мастерской. Имеются различные подкладки для минимальной высоты головки цилиндров. Если головка блока измеряется поперек головки, то зазора между линейкой и поверхностью головки быть не должно. Головку можно перешлифовывать, пока высота установки клапана (А) не будет иметь допустимые значения.
Следует также проверить размер выступания предкамеры для впрыска дизельного топлива. Конец предкамеры должен выступать на 7,6 — 8,1 мм. В мастерской корректируют этот размер путем подкладывания уплотнительных колец различной толщины под предкамеру, чтобы она выступала на нужную величину.
Распределительный вал
Настоящий раздел описывает только проверки, производимые на распределительном валу.
» Вложить вал обоими концевыми шейками в призмы или зажать между концами токарного станка и установить стрелочный индикатор на среднюю шейку.
» Медленно вращая вал, следить за показаниями индикатора. Если они превышают 0,01 мм, то вал изогнут, и его надо заменить.
Замена сальников стержней клапанов (головка не снята)
Сальники стержней клапанов поставляется в ремонтном наборе. В нем также имеются защитные втулки, которые нужно надеть на стержни впускных клапанов при установке. Сальники различаются по диаметру, поэтому их невозможно перепутать. Кроме этого они различны по форме (на рисунке слева показан сальник выпускного клапана, справа — для выпускного).
Для надевания сальников обычно нужно специальное приспособление. Если его нет, и используется кусок тонкой трубки, то нужно работать очень осторожно, чтобы не повредить кромки и кольцевую пружину. При замене сальников нужно снять сухари клапана и клапанные пружины. Чтобы предотвратить падение клапана в камеру сгорания, нужно чтобы соответствующий поршень находился в положении ВМТ. У рассматриваемых двигателей эта работа выполняется очень точно, т.к. двигатель нужно повернуть на строго определенный угол и нужно иметь определенный опыт.
Выполнить следующие операции:
» Провернуть двигатель, пока поршень первого цилиндра не встанет в положение ВМТ.
» Снять распределительный вал.
» Снять сухари клапанов первого цилиндра.
» Вытащить плоскогубцами старые сальники, не повреждая стержень клапана или отверстая толкателей.
» Хорошо смазать новые сальники и осторожно напрессовать их на стержень клапана, нажав вниз на сальник. Надеть защитную втулку на стержень впускного клапана. Напрессовать сальники на направляющую втулку, пока она не сядет правильно.
» Установить клапанные пружины цветной меткой вниз и установить сухари, обратив внимание на их правильную посадку.
» Немного приподнять звездочку распределительного вала, чтобы не снялась цепь и провернуть коленчатый вал, чтобы клапаны следующего цилиндра оба закрылись — порядок работы цилиндров на 5-цилиндровом двигателе 1-2-4-5-3, а на 6-цилиндровом 1-5-3-6-2-4. Как сказано выше, эту работу следует проводить осторожно. Перед снятием сухарей оба клапана должны быть на одинаковой высоте.
ЗАМЕЧАНИЕ: Работать сжимателем клапан них пружин очень медленно, т.к. сухари иногда «залипают» на стержнях и нужно обязательно предотвратить, чтобы из-за быстрого усилия клапанная пружина не вдавились в поршень. Клапанные пружины могут двигаться только вниз.
По посадочным местам блока цилиндров головки взаимозаменяемые. Выпускные клапана и каналы одинаковые. Впускные клапана отличаются размером: ВАЗ-2108 — 35 мм, ВАЗ-21083 — 37 мм. Отсюда и впускной канал головки ВАЗ-21083 больше по пропускной способности горючей смеси. При установке ГБЦ (головки блока цилиндров) ВАЗ-21083 на двигатель ВАЗ-2108 придется менять впускной коллектор.
ГБЦ ВАЗ-21083 с прокладкой от ВАЗ-2108:
ГБЦ ВАЗ-2108 с родной прокладкой:
Ниже показаны различия в геометрии между прокладкамии ВАЗ-21083 и ВАЗ-2108:
Толкатель клапана ВАЗ 2108.
Газораспределительный механизм обеспечивает наполнение цилиндров двигателя свежим зарядом горючей смеси и выпуск отработавших газов в соответствии с требованиями рабочего процесса в каждом из цилиндров двигателя. Этот механизм характеризуется верхним рядным расположением клапанов.
Толкатели — это детали, с помощью которых происходит движение тех или иных клапанов в ДВС, то есть их роль в работе очень ощутима.
Параметр Стандарт Единица измерения: мм
Наружный диаметр толкателя 29,977-29,987
Диаметр отверстия под толкатель 30,000-30,021
Зазор толкателя 0,013-0,044
Толкатели предназначены для передачи усилия от кулачков распределительного вала к клапанам. Толкатели изготовлены в виде цилиндрических стаканов и находятся в направляющих головки цилиндров. В торцевом углублении толкателя размещается регулировочная шайба определенной толщины, обеспечивающая необходимый зазор между кулачком распределительного вала и толкателем с шайбой.
1 — клапан; 2 — направляющая втулка; 3 — стопорное кольцо; 4 -маслоотражательный колпачок; 5 — опорная шайба пружин; 6 — внутренняя пружина; 7 — наружная пружина; 8 — тарелка пружин; 9 — сухари; 10 — регулировочная шайба; 11 – толкатель.
При работе двигателя толкатели все время провертываются вокруг своих осей, что необходимо для их равномерного износа. Вращение толкателей достигается за счет смещения оси кулачка относительно оси толкателя на 1 мм.
Для компенсации теплового расширения клапана конструктивно задается зазор между торцом стержня клапана и кулачком распределительного вала.
Шайбы сделаны из стали 20Х и для увеличения твердости поверхности подвергнуты нитроцементации. В запасные части поставляются регулировочные шайбы толщиной от 3 до 4,5 мм с интервалом через каждые 0,05 мм. Толщина шайбы маркируется на ее поверхности.
При увеличенном зазоре клапан не будет полностью открываться, при уменьшенном — полностью закрываться.
Зазор измеряется на холодном двигателе (при 20°С ) между кулачком распределительного вала (кулачок должен быть направлен вверх от толкателя) и регулировочной шайбой толкателя клапана.
Номинальный зазор для впускного клапана составляет (0,2+0,05) мм, для выпускного — (0,35+0,05) мм. Зазоры регулируются подбором толщины регулировочных шайб. В качестве запасных частей поставляются шайбы толщиной от 3 до 4,5 мм через 0,05 мм.
Шайбу необходимо устанавливать в толкатель маркировкой вниз.
Для того чтобы легче вынуть регулировочную шайбу, в толкателе проточены два паза. Поворачиваете толкатель так, чтобы было удобнее подцепить шайбу.
Толщина новой шайбы рассчитывается по формуле: H = B A – C ,
Где, A – измеренный зазор, мм;
B – толщина старой шайбы, мм;
C – номинальный зазор, мм;
H – толщина новой шайбы, мм.
Пример (для впускного клапана):
A = 0,26 мм,
B = 3,75 мм,
C = 0,2 мм,
тогда
H = 3,75 0,26 – 0,2 = 3,81 (мм).
В пределах допуска зазора +0,05 мм подбираете ближайшую по толщине шайбу (3,8 мм).
Другие артикулы товара и его аналогов в каталогах: 21080100705500.
ВАЗ-2108, ВАЗ-2109, ВАЗ-21099, ВАЗ-2110, ВАЗ-2111, ВАЗ-2112, ВАЗ-2115, ВАЗ 1117-1119, ВАЗ-2114, ВАЗ-2113, ВАЗ-1111 «ОКА», ВАЗ-2110 (2007), ВАЗ 2190.
Любая поломка – это не конец света, а вполне решаемая проблема !
Как самостоятельно заменить толкатель клапана ВАЗ 2108 на автомобиле семейства ВАЗ.
С интернет – Магазином AvtoAzbukaзатраты на ремонт будут минимальными.
Просто СРАВНИ и УБЕДИСЬ !!!
Не забудьте поделиться со своими друзьями и знакомыми найденной информацией, т. к. она им тоже может понадобится — просто нажмите одну из кнопок социальных сетей, расположенных выше.
Направляющие клапанов на ВАЗ-2108: замена своими руками
В статье мы поговорим про направляющие клапанов ВАЗ-2108 и 2109. Моторы на этих машинах устанавливались идентичные, поэтому и ремонт производится одинаково. Собственноручно выполнить ремонт сможет любой желающий, но придется обзавестись навыками и инструментом. Правда, если вы не уверены в своих силах, лучше всего отдать автомобиль в руки опытным мастерам, которые починят его за считаные минуты.
Для чего нужны направляющие?
По сути, это основной элемент клапанного механизма на автомобильном двигателе. Конструкция и материал, из которого изготавливаются направляющие, нацелены на то, чтобы они функционировали в режиме высокой скорости и нагрузки. Кроме того, на элементы воздействует большая температура. А иногда и вовсе случаются перегрузки – в момент, когда пропадает смазка элемента.
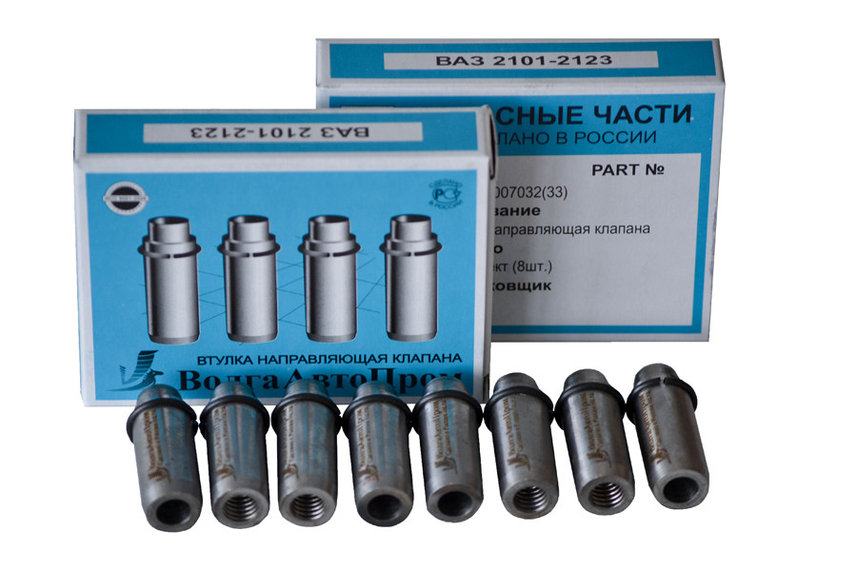
При помощи направляющей получается установить клапан таким образом, чтобы его тарелка максимально плотно прилегала к ГБЦ. Только в этом случае возможно увеличить степень сжатия, а следовательно, и мощность.
Что происходит при деформации?
Как вы понимаете, при работе двигателя может произойти буквально все что угодно. Направляющие элементы подвергаются перегреву, нарушается соосность со стержнем клапана, в итоге ухудшаются параметры мотора. При постоянных нагрузках элемент разбивается еще сильнее, разрушается фаска седла. И в лучшем случае вам придется заменить седло и клапан, так как последний прогорит.
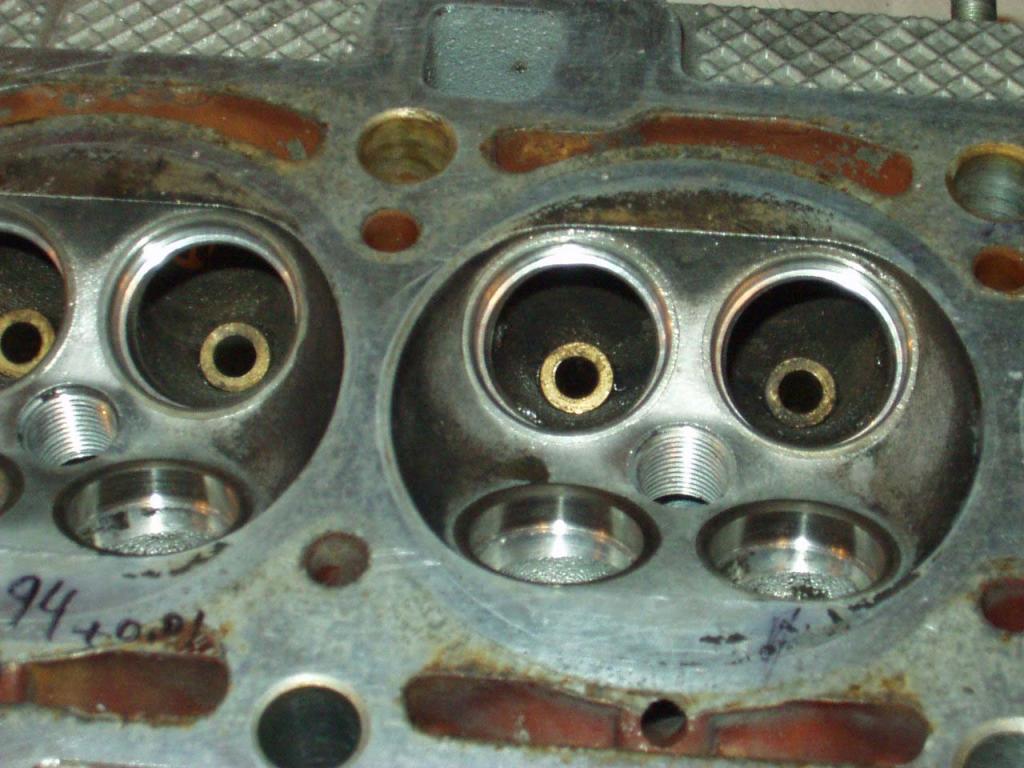
Если ножка клапана продолжит «гулять» в направляющей, то разрушатся и сальники. Они изготовлены из относительно мягкого материала, но при чрезмерных нагрузках он затвердевает. В результате даже при небольшом смещении стержня может произойти разрушение сальника. Результат – масло попадает в камеры сгорания, появляется сильный нагар, увеличивается уровень вредных выбросов. Кроме того, приходит в негодность катализатор и лямбда-зонд (датчик кислорода). И даже если вы произведете установку новых колпачков, проблема не исчезнет надолго.
Из чего делают направляющие?
Существует несколько разновидностей направляющих, которые делятся по материалу, из которого они изготавливаются:
- Латунь.
- Бронза.
- Сплавы чугуна.
- Металлокерамика.
Лидеры по стоимости и теплопроводности – это элементы, изготовленные из латуни и бронзы. Именно поэтому большая часть изделий делается именно из этих материалов. Металлокерамические имеют хорошие характеристики, но стоимость у них в несколько раз выше, и рядовым автомобилистам зачастую они недоступны.
Как определить износ?
На втулке более всего изнашивается внутренняя поверхность. Заметным износ становится при достижении пробега в 150 тыс. км и более. Но если вы используете низкокачественные марки масел, то ресурс элементов становится еще меньше.
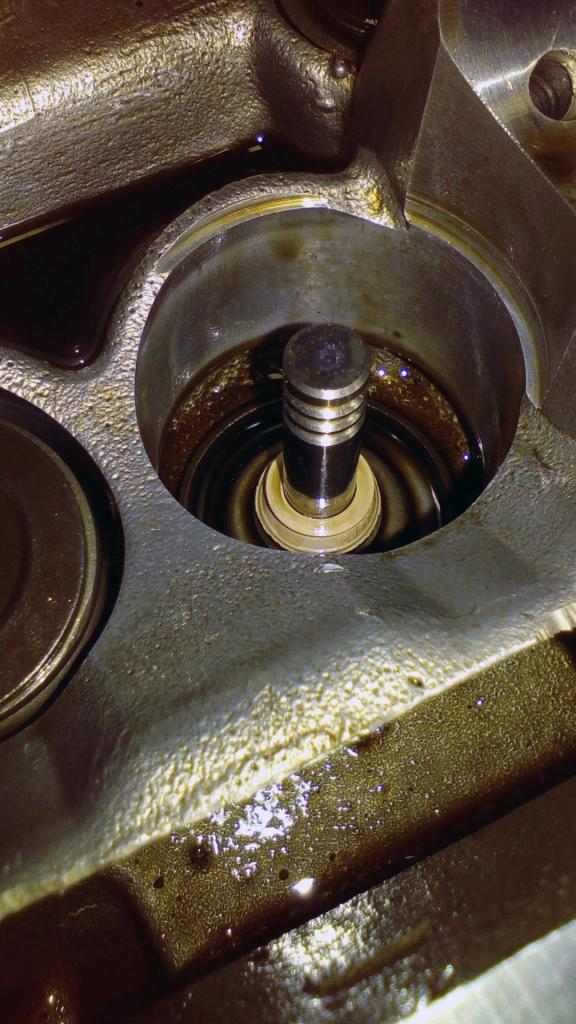
Проверить степень износа можно двумя способами:
- При помощи двух измерительных приборов – нутрометра и микрометра. Они позволяют измерить минимальное значение диаметра (внутреннего) втулок. Кроме того, с их помощью вы можете произвести замер максимального диаметра части хода стержня клапана. По сути, разность между этими двумя значениями и является значением износа. Обязательно только перед началом измерений очищайте все элементы от грязи и пыли, масла. Это позволит существенно увеличить точность и уменьшить погрешность.
- С помощью специального часового индикатора, установленного на стойке. Это может быть индикаторный или микрометрический нутрометр. В том случае, если зазор большой, необходимо установить новый клапан и произвести повторную проверку. Если и в этот раз зазор зашкаливает, то придется менять направляющие.
Впрочем, лучше всего при капитальном ремонте выполнить замену направляющих клапанов. Все равно для замеров нужно снимать ГБЦ. А это самое сложное в процедуре ремонта.
Как снять старые направляющие
Перед тем как начинать ремонт, нужно ГБЦ прогреть до 100 градусов. За счет того, что алюминий расширяется сильнее латуни или бронзы, извлечь направляющие будет немного легче.
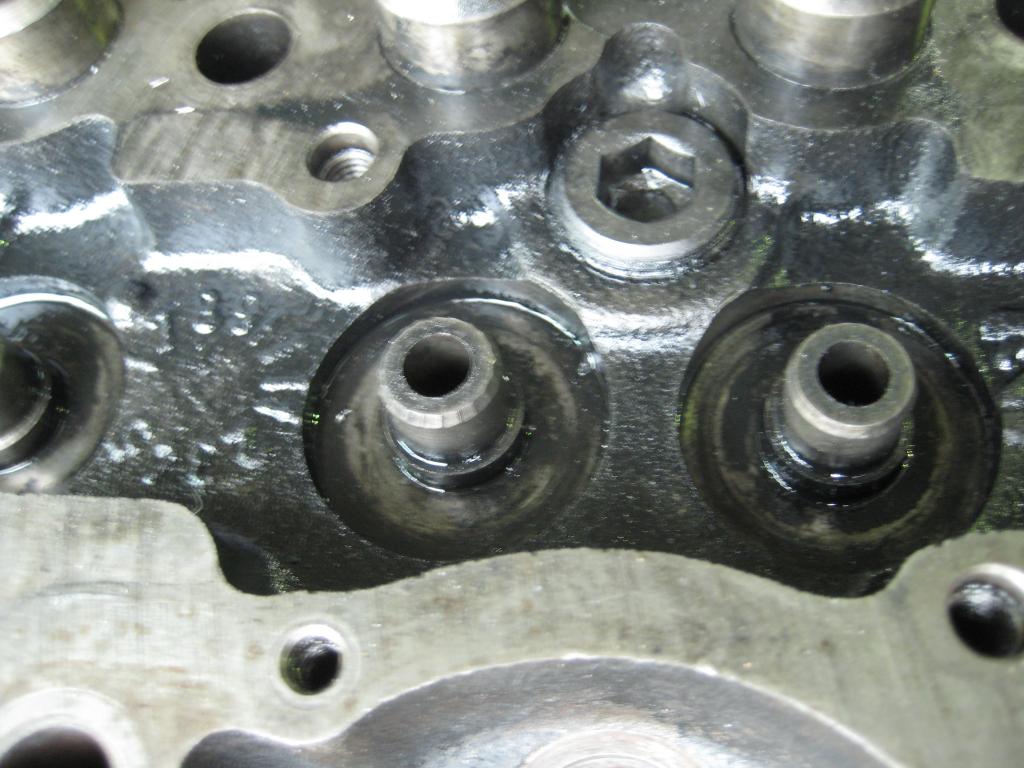
Что нужно учесть при демонтаже:
- Для извлечения лучше всего использовать выколотку (специальную оправку). Конечно, стоимость инструмента довольно высокая, но с его помощью у вас получится выпрессовать втулку четко по оси. Но допускается использовать простые и пневматические молотки.
- Довольно часто случается так, что втулка выходит плохо. Придется прибегнуть к помощи дрели – нею нужно высверлить направляющую. Зачастую ее не нужно полностью высверливать, достаточно просто уменьшить толщину стенок.
- Обратите внимание на то, что у посадочного гнезда должна быть максимально гладкая поверхность. Не допускается наличие царапин, различного рода шероховатостей, иных дефектов, даже незначительных.
После проведения выпрессовки старых втулок, нужно тщательно очистить внутренние посадочные поверхности.
Как поставить новые втулки?
Прежде чем начинать установку направляющих клапанов 2108, нужно определить фактический натяг. Для того чтобы это сделать, потребуется измерить диаметры втулок и посадочных мест под них в головке. Максимальная разница должна быть 0,05 мм. В том случае, если гнездо чересчур маленькое, то придется подбирать втулку меньшего диаметра, и наоборот.
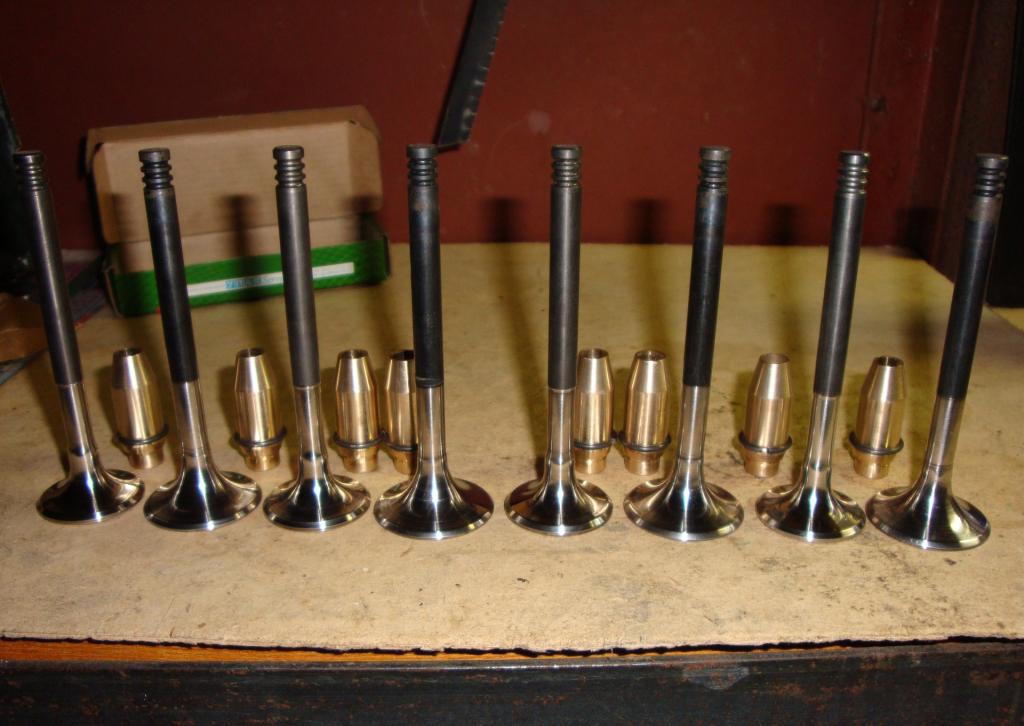
Непосредственно перед запрессовкой втулок требуется прогреть головку, а сами направляющие обработать при помощи жидкого азота. Не всегда только такой имеется в гараже. Поэтому положите детали на несколько часов в морозильную камеру – в результате охлаждения они уменьшатся в диаметре.
Процедура выпрессовки выполняется в обратном порядке. Для того чтобы установить элементы, нужно использовать молоток (простой или пневматический) и оправку. Аккуратными ударами нужно забивать в посадочные отверстия элементы. И также рекомендуется обработать машинным маслом направляющие клапанов ВАЗ-2108, чтобы запрессовка произошла легче.
Ремонт головки блока цилиндров Самара, Самара 2
Руководство по ремонту и эксплуатации — Бензиновые двигатели ВАЗ 2108, ВАЗ 2111-80 — Ремонт головки блока цилиндров
ПРЕДУПРЕЖДЕНИЕ
Головка блока цилиндров заменяется с корпусами подшипников в сборе, так как они обрабатываются совместно.
1. Снимите с автомобиля ваз 2108, ваз 2109, ваз 21099 головку блока цилиндров (Замена прокладки головки блока цилиндров).
2. Отверните винт крепления и отсоедините штуцер подогрева от карбюратора. Если винт отвернуть не удается, ослабьте хомут и снимите шланг со штуцера.
3. Отверните четыре гайки крепления карбюратора (две из них расположены с противоположной стороны).
4. Снимите карбюратор с впускной трубы.
5. Аккуратно снимите прокладки карбюратора.
6. Отверните две гайки крепления теплоизоляционного щитка карбюратора.
7. Ослабьте затяжку гайки на штуцере.
8. Снимите теплоизоляционный щиток карбюратора.
9. Отверните две гайки крепления патрубка забора теплого воздуха.
10. Отверните гайку крепления рыма.
11. Снимите рым и патрубок забора теплого воздуха.
12. Отверните девять гаек крепления впускной трубы и выпускного коллектора.
13. Снимите выпускной коллектор.
14. Снимите впускную трубу.
ПОЛЕЗНЫЙ СОВЕТ
После снятия выпускного коллектора и впускной трубы подложите под головку блока цилиндров деревянные прокладки, чтобы не повредить клапаны, выступающие из головки блока.
15. Снимите две прокладки.
ПРИМЕЧАНИЕ
Снимайте уплотнительные прокладки аккуратно. Если прокладки выпускного коллектора и впускной трубы не повреждены и не сильно обжаты, их можно использовать вторично. Пригоревшие прокладки выпускного коллектора и впускной трубы осторожно отделите с помощью отвертки.
16. Выверните из головки блока цилиндров свечи зажигания.
17. Выверните датчик температуры охлаждающей жидкости (ДТОЖ).
18. Выверните датчик контрольной лампы аварийного давления масла.
19. Отверните десять гаек крепления обоих корпусов подшипников распредвала.
20. Снимите оба корпуса подшипников распредвала с головки блока цилиндров.
21. Выньте распредвал.
22. Снимите сальник с переднего конца распредвала.
23. Отверните гайку крепления натяжного ролика.
24. Снимите натяжной ролик и упорную шайбу, установленную под натяжным роликом.
25. Выньте толкатели клапанов вместе с регулировочными шайбами.
ПРЕДУПРЕЖДЕНИЕ
Вынув очередной толкатель клапана, промаркируйте его и регулировочную шайбу порядковым номером, чтобы при сборке установить их на свое место.
ПРИМЕЧАНИЕ
Привод клапанов состоит из следующих деталей: 1, 2 — клапаны; 3 — наружная пружина; 4 — внутренняя пружина; 5 — верхняя тарелка; б — сухарь; 7 — нижняя тарелка.
Все эти детали нужно демонтировать из головки блока цилиндров.
26. Промаркируйте клапаны номером цилиндра, чтобы при сборке установить клапана на свои места. Маркировку можно нанести с помощью керна как можно ближе к центру клапана: клапаны первого цилиндра — одна точка, второго — две и т.д.
27. Установите под снимаемый клапан подходящий упор.
28. Установите на головку блока цилиндров приспособление для сжатия пружин клапанов. Сожмите им пружины клапана и выньте сухари. Постепенно ослабляя нажим на ручку приспособления, полностью разожмите пружину клапана и снимите приспособление с головки.
29. Снимите наружную пружину клапана с тарелкой.
30. Снимите внутреннюю пружину клапана.
31. Выньте клапан из головки блока цилиндров.
32. Аккуратно снимите маслоотражательный колпачок, не повредив направляющую втулку клапана.
33. Выньте опорную шайбу (тарелку) пружин клапана. Аналогичным образом выньте остальные клапаны.
34. Промойте детали головки блока в бензине, протрите и просушите их.
35. Очистите камеры сгорания от нагара. Осмотрите головку блока цилиндров. Если на головке блока есть трещины или следы прогара в камерах сгорания, замените головку блока цилиндров.
36. Проверьте плоскостность поверхности, прилегающей к блоку цилиндров. Для этого поставьте металлическую линейку ребром на поверхность головки блока цилиндров по центру вдоль, а затем по диагоналям и замерьте щупом зазор между плоскостью головки блока и линейкой. Замените головку блока цилиндров, если зазор превысит 0,1 мм.
37. Очистите нагар с клапанов. Это можно сделать подходящим металлическим инструментом.
38. Осмотрите клапаны. Замените клапаны со следующими дефектами: глубокие риски и царапины на рабочей фаске, трещины, деформация стержня клапана, коробление тарелки клапана, следы прогара. Неглубокие риски и царапины на рабочей фаске можно удалить притиркой клапанов.
ПРИМЕЧАНИЕ
Рис. 4.5. Размеры тарелок клапанов
Повреждения рабочей фаски клапанов, которые невозможно вывести притиркой, можно устранить шлифовкой на специальном станке. При шлифовке надо выдержать размеры, указанные на рис. 4.5. В скобках даны отличающиеся размеры для двигателя ваз 21083.
39. Проверьте состояние пружин клапанов. Искривленные, поломанные или имеющие трещины пружины клапанов замените. Проверьте упругость пружин клапанов. Для этого измерьте высоту пружин в свободном состоянии, а затем под двумя различными нагрузками. Если пружина клапана не соответствует требуемым параметрам, замените пружину.
ПРИМЕЧАНИЕ
Параметры пружин клапанов для определения их упругости:
наружная пружина клапана:
высота в свободном состоянии……………45,2 мм;
высота под нагрузкой ( 26,0+1,7 ) кгс…….33,7 мм;
высота под нагрузкой ( 46,2+2,4 ) кгс…….24,7 мм;
внутренняя пружина:
высота в свободном состоянии…………..34,1 мм;
высота под нагрузкой ( 9,0+0,8 ) кгс……..29,7 мм;
высота под нагрузкой ( 27,5+1,5 ) кгс……20,7 мм.
40. Проверьте состояние седел клапанов. На рабочих фасках седел клапанов не должно быть следов износа, раковин и коррозии. Незначительные повреждения (мелкие риски, царапины и т.п.) можно удалить притиркой клапанов.
ПРИМЕЧАНИЕ
Более значительные дефекты седел клапанов устраняются шлифовкой.
Рис. 4.6. Размеры седел клапанов: а — седло впускного клапана; б — седло выпускного клапана; I — новое седло; II — седло после ремонта.
При шлифовке выдержите размеры, указанные на рис. 4.6. Сначала шлифуется фаска под углом 20°, затем фаска под углом 45°. После шлифовки седел надо притереть клапаны, затем тщательно очистить и продуть сжатым воздухом головку блока, чтобы в каналах и камерах сгорания не осталось частиц абразива. В скобках даны отличающиеся размеры для двигателя ваз 21083.
41. Проверьте зазор между направляющими втулками и клапанами (рис. 4.7).
ПРИМЕЧАНИЕ
Рис. 4.7. Размеры клапанов и их направляющих втулок
Зазор между клапаном и направляющей втулкой, мм:
номинальный для впускных клапанов…………….0,022-0,055;
номинальный для выпускных клапанов……………0,029-0,062;
предельно допустимый зазор для впускных и выпускных клапанов …0,3.
Зазор вычисляется как разность между диаметром отверстия во втулке и диаметром стержня клапана. Если зазор меньше предельно допустимого, попробуйте заменить клапан. Если зазор превышает предельно допустимый, замените направляющую втулку.
42. Выпрессуйте со стороны камеры сгорания дефектную направляющую втулку клапана специальной оправкой.
43. Вставьте новую направляющую втулку клапана в специальную оправку.
ПРИМЕЧАНИЯ
В качестве запасных частей поставляются направляющие втулки клапанов со стопорными кольцами. Направляющие втулки клапанов имеют увеличенный на 0,2 мм наружный диаметр и уменьшенный диаметр отверстия под клапан.
44. Запрессуйте с помощью оправки направляющую втулку клапана со стороны распредвала до упора стопорного кольца в головку блока цилиндров.
45. Разверните отверстие в направляющей втулке клапана с помощью развертки до 8,022-8,040 мм для впускных клапанов и до 8,029-8,047 мм — для выпускных. После этого прошлифуйте седла клапанов, как описано выше, центрируя инструмент по отверстию во втулке.
46. Осмотрите толкатели клапанов. Если на рабочей поверхности толкателя клапана есть задиры, царапины или другие повреждения, замените толкатели клапанов.
47. Осмотрите регулировочные шайбы толкателей клапанов. На их рабочих поверхностях не должно быть задиров, забоин, царапин, следов ступенчатого или неравномерного износа, натира металла. При таких дефектах шайбы надо заменить. На шайбах допускаются концентрические следы приработки с кулачками распределительного вала.
48. Измерьте длину болтов крепления головки блока цилиндров, так как при многократной затяжке болты головки блока вытягиваются. Если длина болтов головки блока цилиндров превышает 135,5 мм, замените болты.
49. Для проверки герметичности головки блока цилиндров заглушите отверстие в патрубке рубашки охлаждения в заднем торце головки блока, переверните головку блока цилиндров камерами сгорания вверх и залейте керосин в каналы рубашки охлаждения. Если появились течи керосина, значит, головка блока цилиндров не герметична, и головку блока надо заменить.
50. Если устанавливается старый клапан, снимите заусенцы с проточек под сухари. После этого необходимо притереть клапан к седлу.
51. Установите клапаны в головку блока в соответствии с ранее сделанной маркировкой, предварительно смазав стержни клапанов моторным маслом.
52. Установите нижние тарелки пружин клапанов.
53. Установите маслосъемные колпачки.
54. Замените распределительный вал, если на шейках и кулачках распредвала есть следы износа, задиры и глубокие риски. В мастерских, оборудованных специальным инструментом и приспособлениями, можно проверить радиальное биение шеек распредвала (радиальное биение шеек не должно превышать 0,02 мм) и зазор между отверстиями опор и шейками распредвала, который не должен превышать 0,2 мм (зазор для новых деталей 0,069-0,11 мм).
55. Установите распредвал и корпуса подшипников.
56. Установите прокладки, выпускной коллектор и впускную трубу.
57. Установите головку на блок цилиндров, проверьте зазоры в приводе клапанов и при необходимости отрегулируйте их.
Цитата
Примечания
Наружная пружина:
Внутренняя пружина:
Величина зазоров между клапаном и направляющей втулкой, мм:
Если зазор меньше предельно допустимого, попробуйте заменить клапан. Если зазор превышает предельно допустимый, замените направляющую втулку.
|