Производство двигателей для КамАЗов
Автор:29 января 2016 11:58
Всегда приятно увидеть в России производство, соответствующее самым высоким мировым стандартам. Одним из таких высокотехнологичных предприятий является Завод двигателей «КАМАЗ», занимающий 8-е место в мире по объёму выпуска дизельных двигателей. Его нам удалось посетить во время декабрьского визита в Набережные Челны.

Источник:
Огромные производственные цеха впечатляют и заставляют задуматься об объёмах производимой здесь продукции.

Источник:
Повсюду самое современное высокоточное оборудование, необходимое для такой сложной части автомобиля как двигатель.

Источник:
Многие процессы происходят за стеклом, в точности как в операционной.

Источник:
Посколько большая часть производства автоматизирована, немногочисленным рабочим приходится лишь контролировать непрерывно идущую работу.

Источник:
Свежеотточенные нутренние детали двигателя.

Источник:

Источник:
Кто угадает, что это за штуковина?

Источник:
На конвейер плотным потоком заходят блоки цилиндров, прямиком с места их рождения — литейного завода.

Источник:

Источник:
Затем их внутренности заполняются коленчатыми и распределительными валами.

Источник:

КАМАЗ‑910.10 — перспективный дизельный мотор — журнал За рулем
КАМАЗ и швейцарская фирма Liebherr-International AG создают перспективный рядный двигатель, отвечающий нормам Евро-5.
01
Это обычная для КАМАЗа практика — дать зарубежному партнеру техзадание и совместно с ним разрабатывать новый узел или агрегат.
Что-то подобное было в начале 70‑х годов прошлого века — в период строительства Камского автозавода, когда дизель для челнинских грузовиков разрабатывал Ярославский моторный завод.
Сейчас работают над КАМАЗом нового поколения, и очень важно получить современный дизель, удовлетворяющий требованиям норм Евро‑5, а в перспективе — и Евро‑6.
P5ZV7385_новый размер
По габаритам мотор D946 сопоставим с европейскими дизелями объемом 12–13 литров, а здесь многое зависит от размерности и межцентрового расстояния.По габаритам мотор D946 сопоставим с европейскими дизелями объемом 12–13 литров, а здесь многое зависит от размерности и межцентрового расстояния.
Можно было бы купить лицензию и технологические сборочные линии, как это сделала «Группа ГАЗ» с двигателем Renault Trucks DCi 11 для Ярославского моторного завода. Но там мотор был изначально уровня Евро‑3, хотя и с возможностью доводки до Евро‑4.
Но ведь в Челнах готовят к производству свои двигатели уровня Евро‑5 — традиционные V‑образные «восьмерки» КАМАЗ‑740.735–400 и КАМАЗ‑750.10–400. Зачем же тратить лишние деньги и время, разрабатывать рядный шестицилиндровый мотор — только ради того, чтобы он был?
Дело в том, что давние приверженцы V‑образных дизелей для грузовиков Mercedes-Benz и Scania тоже неспроста планируют сворачивать их производство в пользу рядных «шестерок». Это связано в первую очередь с особенностями компоновки двигателей уровня Евро‑6 и выше. Для нейтрализации отработавших газов, для оптимизации настроек электронно-управляемых топливных систем дизелей будет недостаточно сочетания рециркуляции отработавших газов (EGR), впрыска водного раствора мочевины (SCR) и регенерируемого сажевого фильтра. Специалисты сходятся во мнении, что эти системы придется дополнять турбокомпаундом. То есть установкой еще одной турбины, которая через вязкостную муфту и понижающий редуктор дополнительно, причем без затрат топлива, подкручивает коленвал. Дармовая мощность позволяет без особых проблем придушить двигатель в угоду экологии.
03
Если понадобится, можно поставить и двухступенчатый турбонаддув.Если понадобится, можно поставить и двухступенчатый турбонаддув.
В Европе турбокомпаунд на дизелях первыми начали применять Volvo и Scania, в несколько этапов: в середине 1990‑х, в середине 2000‑х, а теперь и в период 2012- 2014 годов.Шведы и немцы из фирмы Daimler говорят, что очень сложно скомпоновать дополнительную громоздкую турбину с редуктором на блоке V‑образного мотора, не увеличив ширину и высоту двигателя. А на рядной «шестерке» турбокомпаунд легко монтируется сбоку блока, рядом с маховиком.
Именно необходимость иметь свой перспективный рядный шестицилиндровый дизель заставила ОАО «КамАЗ» тратить деньги на разработку нового мотора. При выборе партнера в первую очередь обратились к фирме AVL List, но австрийцы просили на работу пять лет. А Liebherr обещал управиться за три года. Видимо, сошлись и в цене.
04
На турбине есть заслонка — простейший моторный тормоз.На турбине есть заслонка — простейший моторный тормоз.
НОВАЯ РАЗМЕРНОСТЬ
Компания Liebherr знаменита не только холодильниками и подъемными кранами: с 1984 года она выпускает и дизели, которые стали устанавливать на краны, экскаваторы и бульдозеры марки Liebherr. К тому времени в Челнах уже восемь лет как выпускали V‑образную «восьмерку» КАМАЗ‑740…
Новый мотор КАМАЗа будут строить на основе 12‑литрового дизеля Liebherr D946, который стоит на конвейере всего два года и используется только на строительной технике, но не на автомобилях. И одна из главных составляющих адаптации этих моторов к челнинским грузовикам — уменьшение массы и габаритов.
Конструктивно Liebherr D946 схож со многими рядными дизелями: у него чугунный блок, мокрые гильзы (это традиционно для любых дизелей Liebherr), распредвал находится в блоке, привод клапанов — штангами, шестерни ГРМ и насосов — со стороны маховика. Точный рабочий объем 11,95 литра, размерность 130×150 мм, то есть КАМАЗ отходит от привычного диаметра поршня 120 мм.
05
Головки у этого дизеля — чугунные, раздельные, четырехклапанные.Головки у этого дизеля — чугунные, раздельные, четырехклапанные.
Часто говорят, что современный 11-13-литровый дизель должен быть короткоходным. На самом деле и среди легковых дизелей можно по пальцам пересчитать даже «квадратные» моторы, а уж тем более с «коротким ходом».
У больших дизелей для повышения механического КПД тем более выгодно уменьшать обороты максимальной мощности — короткоходность не нужна.
У дизеля КАМАЗ‑910.10.550 должен быть очень хороший показатель удельной литровой мощности — 33,75 кВт/л и, что важно, удельный эффективный расход топлива — 183 г/кВт·ч.
06
Во впускном коллекторе есть спираль для подогрева воздуха.Во впускном коллекторе есть спираль для п
от СССР до наших дней
Рожденный полвека назад как крупнейший производитель большегрузных автомобилей, Камский автозавод и ныне, наперекор всем превратностям судьбы, сохраняет свой статус.
Шестидесятые годы прошлого столетия. Растущая экономическая мощь советского государства способствует значительному увеличению объемов грузоперевозок. Страна остро нуждается в большегрузных автомобилях с экономичными дизельными двигателями, но существующие автозаводы не в состоянии покрыть этот дефицит. Назрела потребность в строительстве нового автогиганта.
В августе 1969 года ЦК КПСС и Совмин СССР приняли Постановление № 674 «О строительстве комплекса автомобильных заводов в Набережных Челнах Татарской АССР». Объем производства определили в 150 тыс. автомобилей и 250 тыс. дизельных двигателей. 26 сентября 1969 года министр автомобильной промышленности Александр Тарасов подписал приказ о наименовании нового предприятия Камским автозаводом, а уже 13 декабря экскаваторщик Михаил Носков приступил к работе на площадке первого объекта КАМАЗа. Эта дата является официальным началом строительства завода.
Конструкцию грузовика, по опыту ГАЗа, рассчитывали купить у ведущих зарубежных компаний. Но ни Ford, ни Daimler в реалиях холодной войны не смогли сотрудничать с СССР, из-за опасений НАТО усиления советской военной мощи. Пришлось рассчитывать на собственные силы. Выбор пал на ЗИЛ, где в тот период шло создание семейства перспективных грузовиков с кабиной над двигателем, включавших модели с колесной формулой 6×4 для работы в составе автопоездов полной массой 26,5–32 тонны и автомобилей (6х6) для 24‑тонных автопоездов.
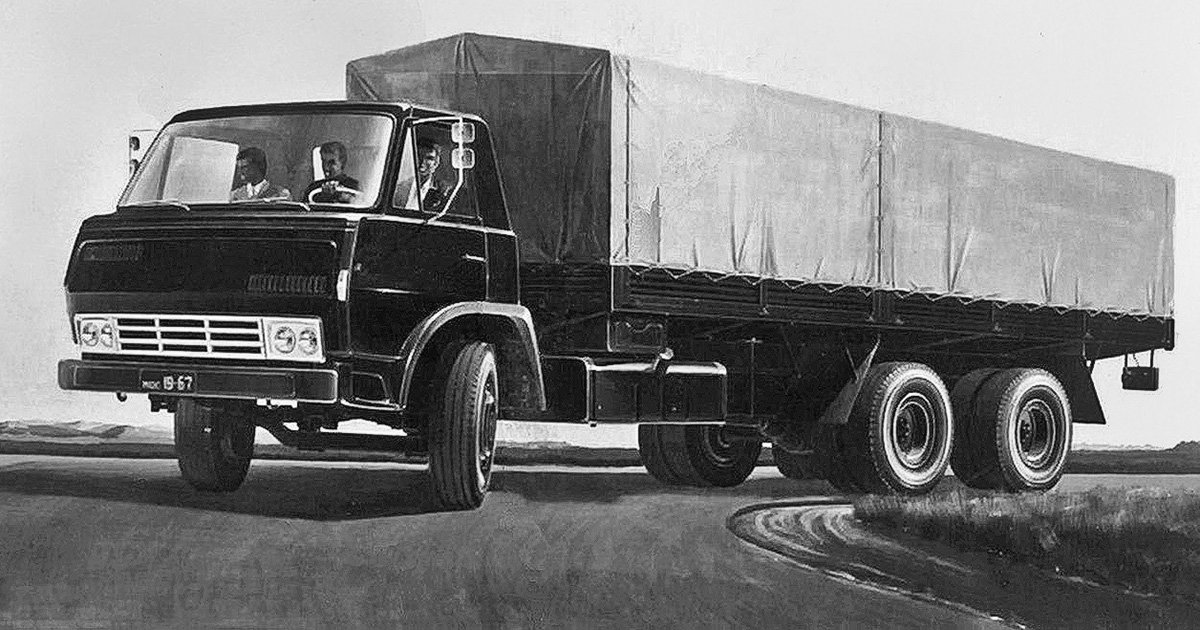
Как раз к 1968 году на столичном заводе построили первый опытный образец седельного тягача ЗИЛ-2Э170В с дизельным двигателем ЯМЗ-6Э641 мощностью 210 л. с. Эти разработки и легли в основу будущих грузовиков КАМАЗ. Новые грузовики 6×4 предназначались для эксплуатации на большей сети дорог с несущей способностью: 6 тонн — на одиночную ось и 11 тонн — на тележку.
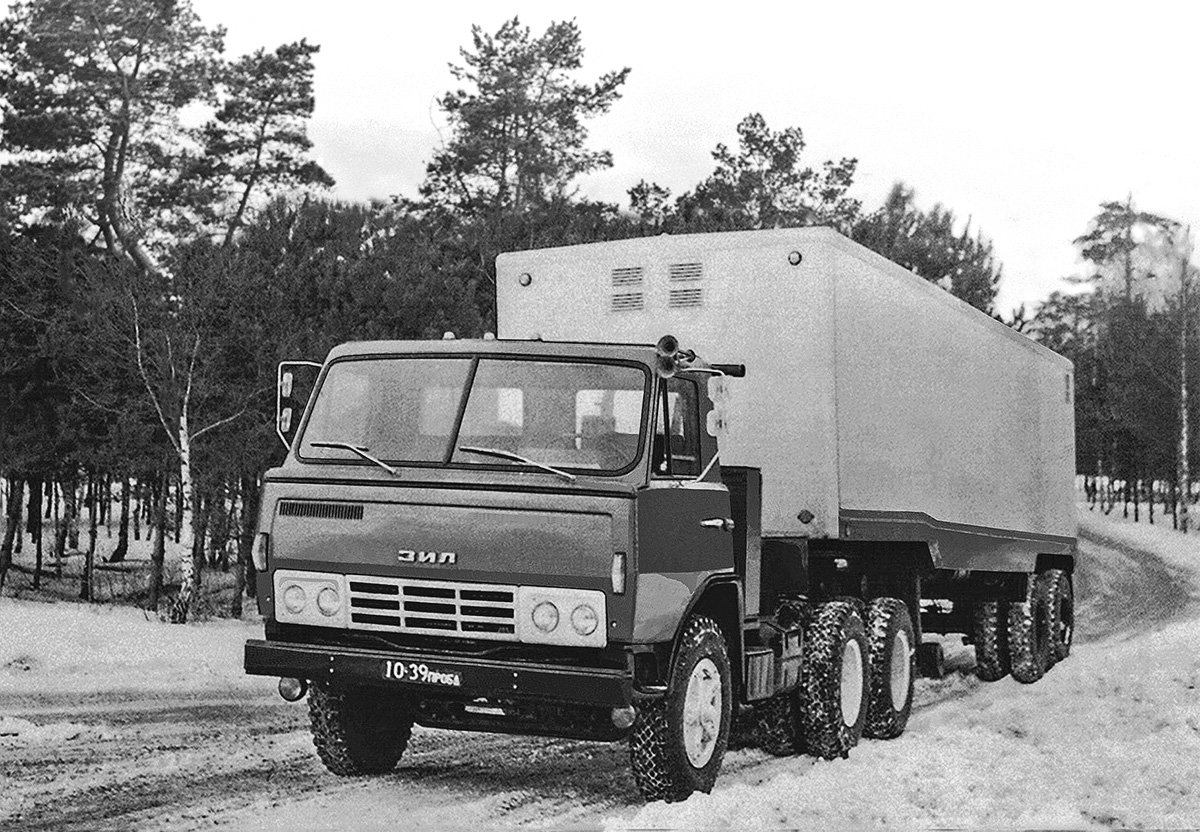
Кроме ЗИЛа участие в проекте приняли и другие предприятия страны. Ярославский моторный завод разрабатывал V-образные дизели КАМАЗ-740 и КАМАЗ-741 мощностью 180, 210 и 260 л. с., сцепления и коробки передач. Одесский автосборочный завод трудился над конструкциями полуприцепов к седельным тягачам, Головное конструкторское бюро по прицепам в Балашове работало над прицепами к автомобилям-тягачам, а Минский автозавод занимался созданием самосвальных установок.
С 1969 по 1978 годы на ЗИЛе построили более 50 опытных образцов автомобилей КАМАЗ, суммарный пробег которых в ходе дорожных испытаний составил 4,5 млн км. Для Камского автозавода создали обширную линейку грузовиков с колесными формулами 6х4 и 6х6 (седельные тягачи, бортовые автомобили, самосвалы), которые потом десятилетиями выпускались предприятием. При этом новички по своему уровню не уступали лучшим зарубежным аналогам.
Надо сказать, что на стройке века в Набережных Челнах работало более 100 тысяч человек. Заказы КАМАЗа на стройматериалы и оборудование выполняли свыше 2000 предприятий СССР. Будущий автозавод обеспечивался самым современным технологическим оборудованием. В его оснащении приняли участие свыше 700 иностранных фирм. Благодаря беспрецедентным объемам финансирования работы велись невероятно высокими темпами. Так, если осенью 1970 года уложили первые кубометры бетона в фундамент ремонтно-инструментального завода, то уже в 1973 году возвели корпуса практически всех объектов первой очереди КАМАЗа.
В результате челнинский первенец — бортовой 8‑тонный КАМАЗ-5320 сошел с главного сборочного конвейера 16 февраля 1976 года. Чуть позже госкомиссия подписала акт о вводе в эксплуатацию первой очереди Камского комплекса заводов по производству большегрузов. Объемы производства также росли рекордными темпами. Летом 1979 года преодолели рубеж в 100 тысяч грузовиков.
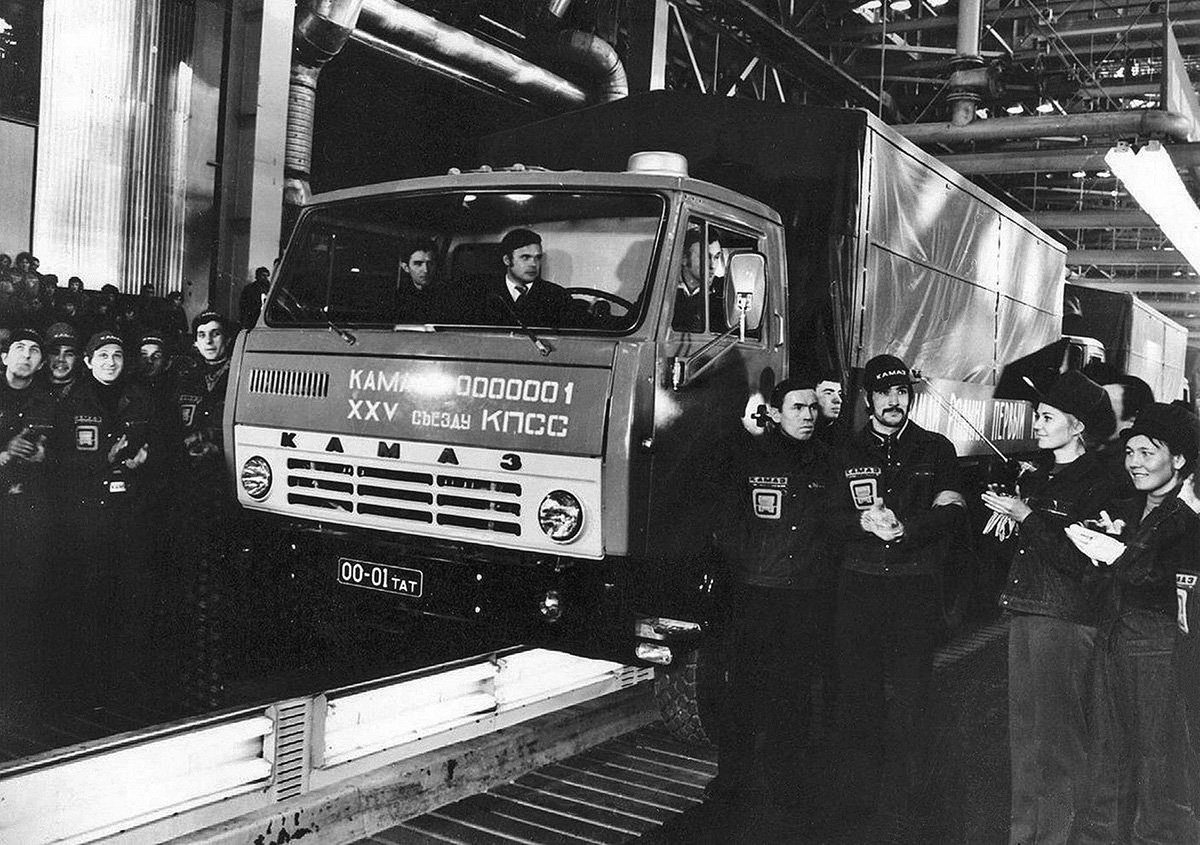
В 1976–1978 годах производственная программа включала три базовые модели. Наряду с КАМАЗ-5320 выпускались 10‑тонный самосвал КАМАЗ-5511 и седельный тягач КАМАЗ-5410 для работы в составе автопоезда полной массой 26 тонн. В последующие годы появились бортовой 10‑тонный грузовик КАМАЗ-53212 с удлиненной колесной базой, шасси КАМАЗ-53211 и КАМАЗ-53213 грузоподъемностью 11 тонн, сельскохозяйственный 7‑тонный самосвал КАМАЗ-55102 с боковой разгрузкой и седельный тягач КАМАЗ-54112 для 33‑тонного автопоезда.
В 1981 году заработала вторая очередь завода. Здесь наладили выпуск 6‑тонной армейской версии КАМАЗ-4310 (6х6) с лебедкой, двумя топливными баками и системой регулирования давления воздуха в шинах. Для аграриев предлагали 7‑тонный вариант КАМАЗ-43105. В те же годы все базовые модели оснащались моторами с возросшей до 220 л. с. мощностью и 10‑ступенчатой коробкой передач. В октябре 1988 года конвейер покинул миллионный грузовик.
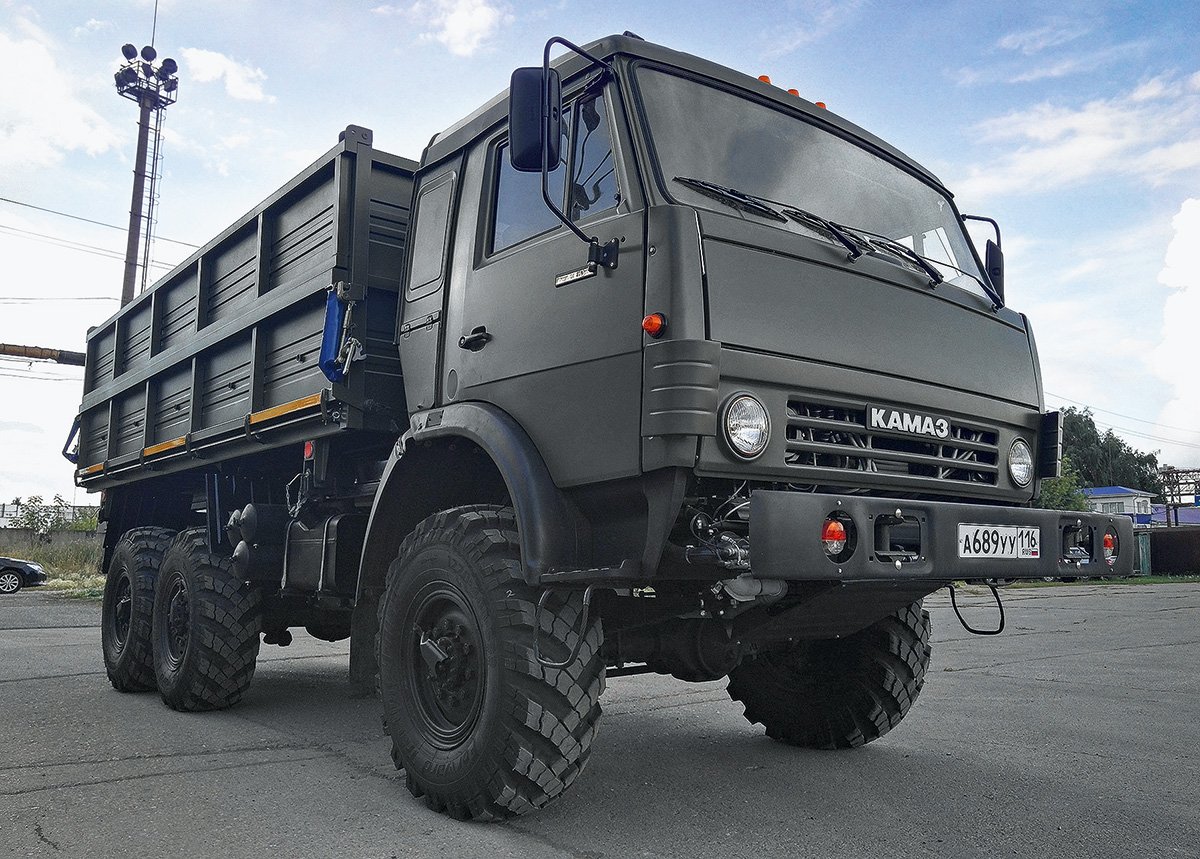
В конце 1980‑х годов предприятие начало разработку автомобилей второго поколения. Обновленные модели комплектовались отечественными турбодизелями, а также импортными моторами и комплектующими. Комфорт кабины улучшили за счет более высокой крыши и ряда технических доработок. Тогда же появляются бортовой КАМАЗ-5325 и седельный тягач КАМАЗ-5425 (4×2). В 1987‑м в производство пошла малолитражка ВАЗ-1111 «Ока», которую выпускали до 1994 года.

23 августа 1990 года производственное объединение КАМАЗ преобразовали в АО. С переходом на рыночные рельсы и появлением на российском рынке импортной техники начались проблемы со сбытом, огромные мощности фактически простаивали, финансовое состояние предприятия резко ухудшилось.
Картину еще больше усугубил пожар, случившийся в апреле 1993 года на заводе двигателей КАМАЗа, который полностью его разрушил. Но, опираясь на поддержку всей страны, предприятие восстановило мощности по выпуску двигателей, а также ввело в эксплуатацию новейшее технологическое оборудование. Изготовление моторов возобновили в декабре 1993‑го.
С 1995 года в серию пошло третье поколение грузовиков, базировавшееся на модернизированном семействе машин 6×4. Среди этих моделей были 11‑тонный бортовой КАМАЗ-53215, 6,6‑кубовый самосвал КАМАЗ-55111.02, седельный тягач для 36‑тонного автопоезда КАМАЗ-54115, длиннобазное шасси КАМАЗ-53229 грузоподъемностью 17 тонн, шасси КАМАЗ-5513 для бетоносмесителей и сменных кузовов.
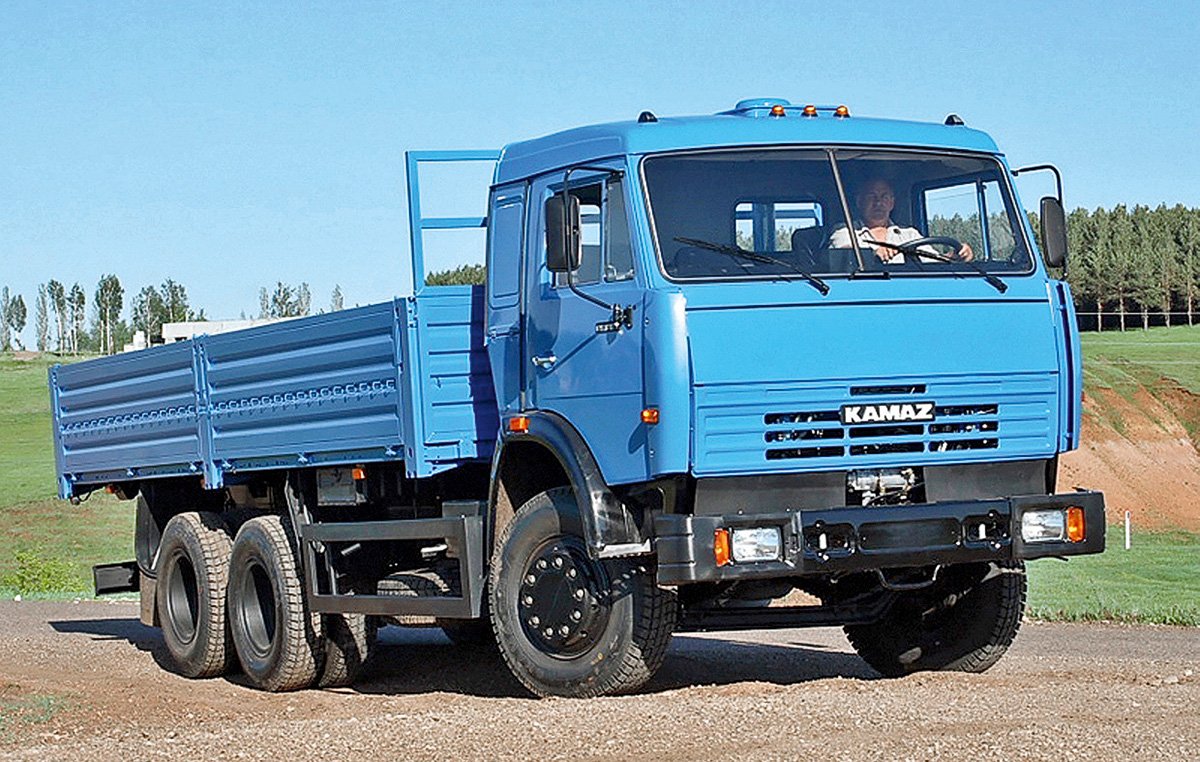
В конце 1990‑х появились новые модели самосвалов — 13‑тонный КАМАЗ-55112 и 15‑тонный КАМАЗ-65115. Двухосный дорожный грузовик КАМАЗ-4325 оснастили 240‑сильным мотором. Его полноприводным вариантом стал 4‑тонный автомобиль КАМАЗ-4326.
Одновременно завод разработал новые модели, ставшие дальнейшим развитием прежних образцов. На трехосном шасси базировались 13‑тонный лесовоз КАМАЗ-53228 и самосвал КАМАЗ-65111 (6х6) грузоподъемностью 14 тонн. В 1996 году представили шасси КАМАЗ-6520 (6х4) грузоподъемностью 20–22 тонны для установки надстроек, а также 19‑тонный самосвал КАМАЗ-6522 (6х6) с 12‑кубовым кузовом. Они оснащались новым турбодизелем КАМАЗ-740.51 мощностью 320 л. с., 8‑ступенчатой КП. Развитием этих машин стало шасси КАМАЗ-6340 (8х4) грузоподъемностью 16 тонн для монтажа надстроек, на базе которого с 1996 года выпускался 18,5‑тонный самосвал КАМАЗ-6540.
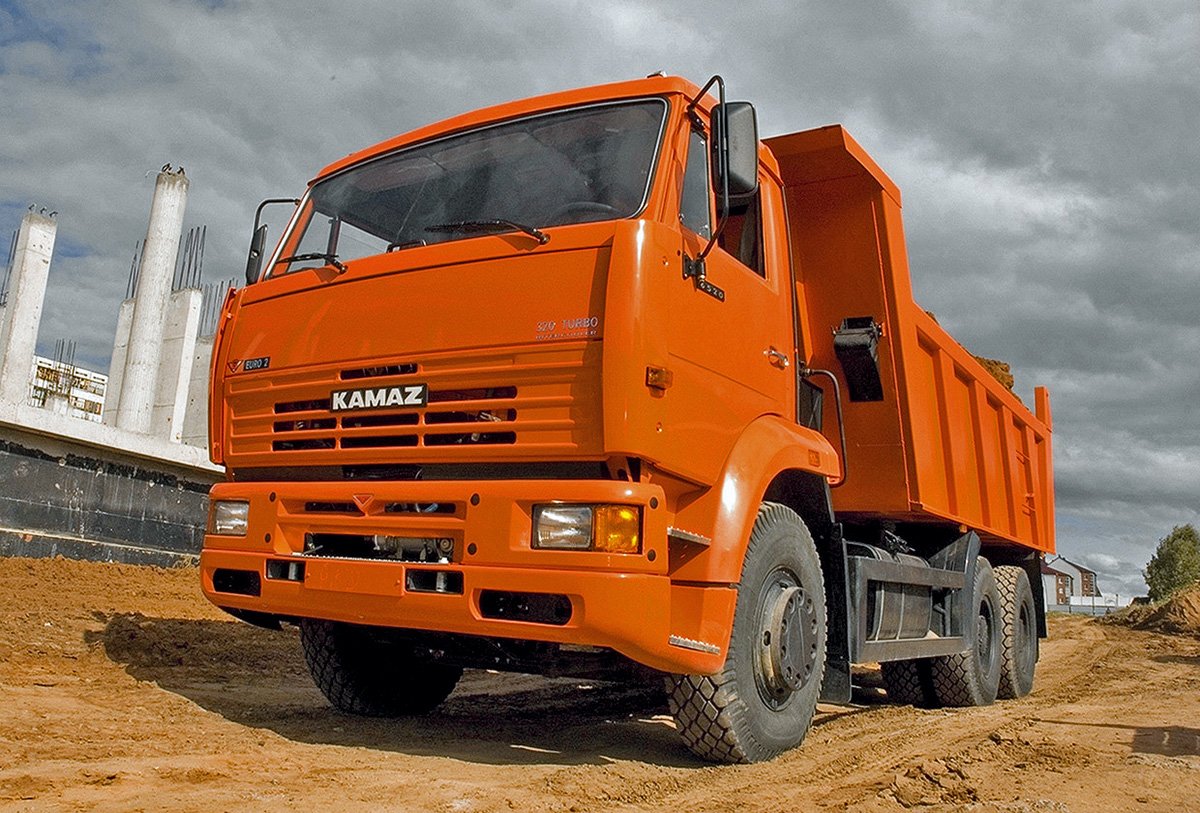
В 2000 году появились экономичные автомобили 6х4 — 14‑тонный бортовой КАМАЗ-65117 (260 л. с.) и седельный тягач КАМАЗ-65116 — преемники моделей КАМАЗ-53212 и КАМАЗ-54112 соответственно, а также 14,5‑тонный самосвал КАМАЗ-45231 с трехсторонней разгрузкой. Тогда же прошла презентация нового автобуса НефАЗ-5299 на базе КАМАЗ-5297, а в ноябре 2003 года в серию запустили городской развозной автомобиль КАМАЗ-4308.
С 2005 по 2009 годы КАМАЗ создал совместные предприятия с компаниями ZF, Cummins, Knorr-Bremse, Federal Mogul и Daimler по выпуску агрегатов трансмиссий, дизельных двигателей, тормозных систем, деталей цилиндро-поршневой группы и сборке грузовиков Fuso. Несколько ранее, в декабре 2008 года, концерн Daimler AG приобрел 10 % КАМАЗа.
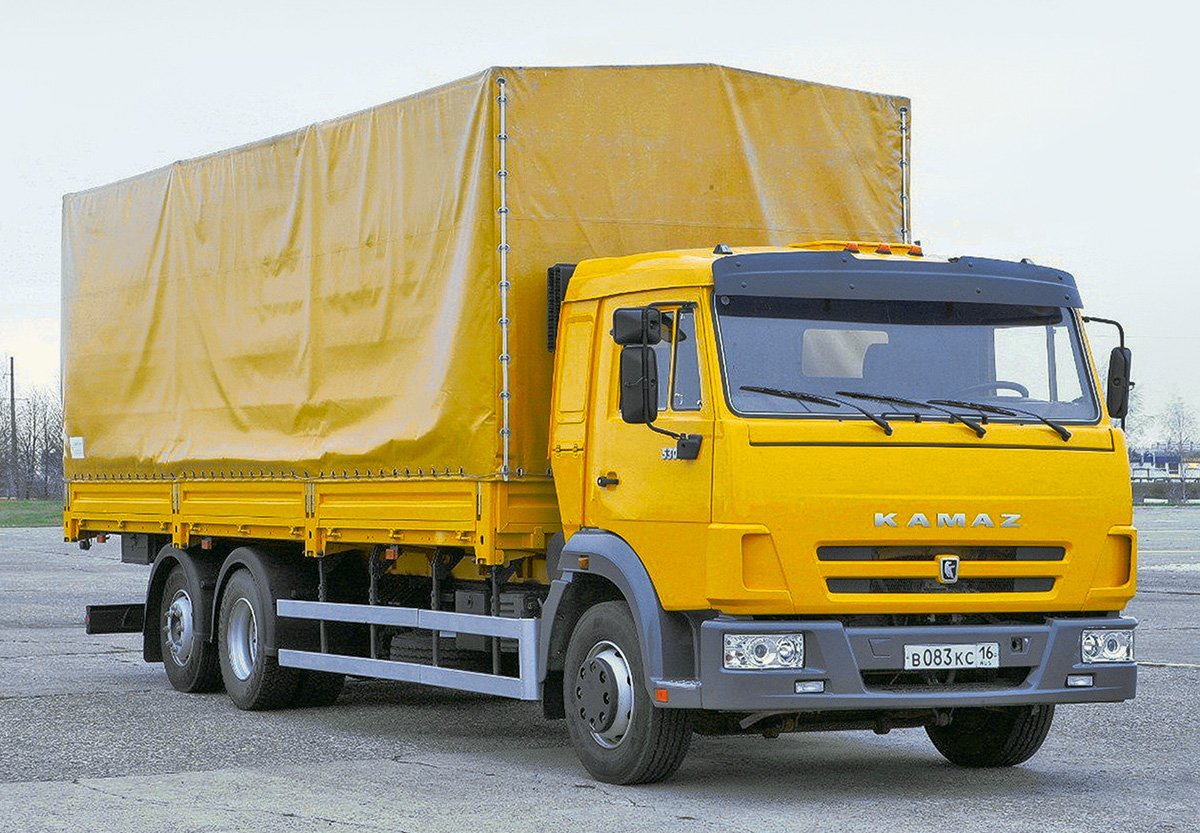
В начале 2010 года завод освоил серийное производство автомобилей с рестайлинговыми кабинами, а в 2012 году с конвейера сошел 2‑миллионный грузовик. Тогда же подписали соглашение с Daimler Trucks, согласно которому КАМАЗу передали технологию производства кабин Axor для установки на грузовики нового поколения. Результатом стал серийный выпуск в конце 2013 года нового флагмана модельного ряда — магистрального тягача КАМАЗ-5490.
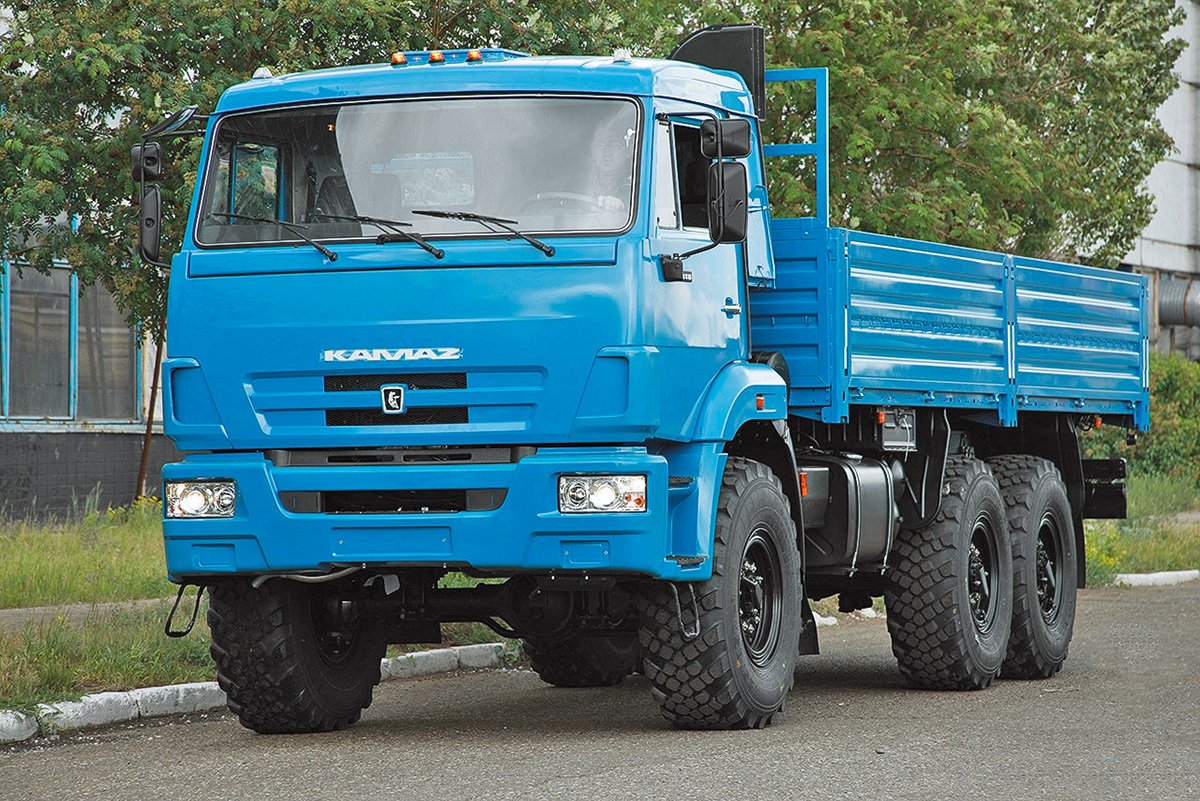
В 2014 году путевку в жизнь получили седельный тягач КАМАЗ-65206 и бортовой магистральный грузовик КАМАЗ-65207, а еще тогда открыли корпус по производству автомобилей КАМАЗ и автобусных шасси с газовыми двигателями, приступили к испытаниям беспилотника, разработанного совместно с «ВИСТ Групп» и Cognitive Technologies.
В 2017 году предприятие разработало и вывело на рынок свыше 100 комплектаций грузовиков и шасси, в том числе пять новых моделей поколения К-4 — седельный тягач, самосвалы и шасси. Наряду с этим продемонстрировали первый образец магистрального тягача КАМАЗ-54901 поколения К5, а в декабре 2017 года на заводе двигателей собрали первые образцы рядного 6‑цилиндрового дизеля КАМАЗ910.10 для грузовиков серии К5. Предприятие стало первой отечественной компанией, освоившей производство электробуса КАМАЗ-6282, заряжаемого от станции ультрабыстрой подзарядки.
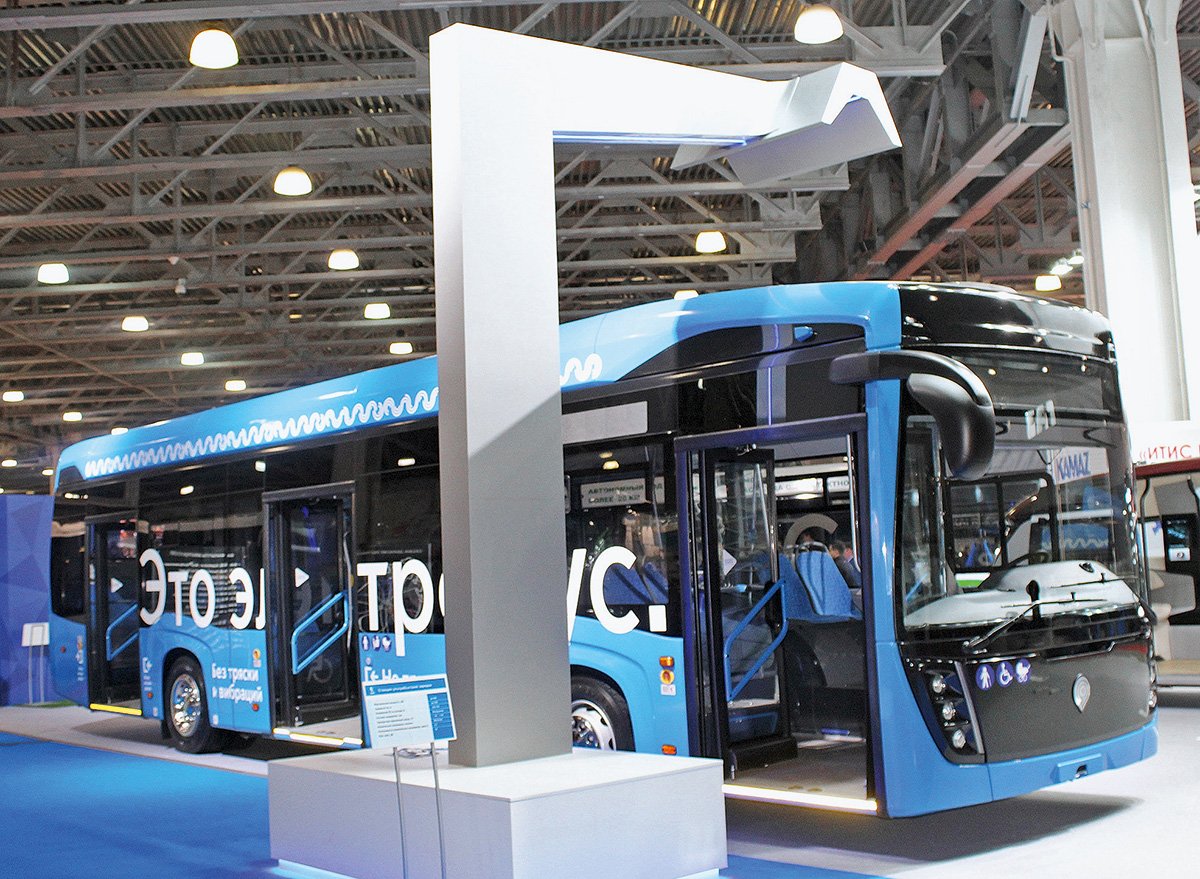
Нынешний год отмечен началом серийного производства каркасов кабин поколения К5 на заводе, построенном совместно с компанией Daimler AG, выпуском промышленной партии магистральных тягачей КАМАЗ-54901, а также премьерами седельного тягача КАМАЗ-65659 (6х4), обновленного тягача KAMAЗ-5490 NEO2, электромобиля КАМАЗ-53198, самосвала КАМАЗ-6595, опытного образца сочлененного вездехода КАМАЗ-6355 (8х8) «Арктика». Ближайшие перспективы челнинцы связывают с многоосными самосвалами семейства «Самсон» грузоподъемностью 55 и 70 тонн, автопилотируемым электробусом ШАТЛ, энергоэффективным магистральным тягачом КАМАЗ-2020.
За свою 50‑летнюю историю Камский автозавод изготовил около 2,3 млн автомобилей и порядка 2,9 млн двигателей. Неудивительно, что каждый третий грузовик полной массой 14‑40 тонн на дорогах России и стран СНГ — это КАМАЗ. К тому же машины из Набережных Челнов работают более чем в 80 странах мира.
Хочу получать самые интересные статьи
Двигатель КАМАЗ серии 740.11-240 — фото, характеристики, схема, описание
Руководство по ремонту и обслуживанию КПП КАМАЗ 740.11-240
Содержание
Состав двигателя, устройство и работа
Блок цилиндров
Блок цилиндров является основной корпусной деталью двигателя и представляет собой отливку из чугуна СЧ25 ГОСТ 1412-85.
Отливку подвергают искусственному старению для снятия термических напряжений, что позволяет блоку сохранить правильные геометрические формы и размеры в процессе эксплуатации.
Два ряда цилиндровых гнезд, отлитых как одно целое с верхней частью картера, расположены под углом 90° один к другому.
Левый ряд цилиндров смещен относительно правого вперед на 29.5 мм, что обусловлено установкой на каждую шатунную шейку коленчатого вала двух шатунов рядом.
В каждом ряду имеется по четыре цилиндровых гнезда, выходящих на верхние обработанные плоскости, которые служат привалочными поверхностями для головок цилиндров.
Пpивaлочныe поверхности отличаются высокой плоскостностью и параллельностью оси расточек под подшипники коленчатого вала.
Каждое цилиндровое гнездо имеет два соосных цилиндрических отверстия, выполненных в верхнем и нижнем поясах блока, по которым центрируются гильза цилиндра, и выточки в верхнем поясе, образующие кольцевые площадки под бурты гильз. Чтобы обеспечить правильную посадку гильзы в гнезде, параметры плоскостности и перпендикулярности опорной площадки под бурт гильзы к общей оси центрирующих расточек должны быть выполнены с высокой точностью.
На нижнем поясе выполнены две канавки под уплотнительные кольца, которые предотвращают попадание охлаждающей жидкости из полости охлаждения блока в полость масляного картера двигателя.
К поперечным стенкам блока, образующим рубашку охлаждения для каждого цилиндра, равномерно (вокруг цилиндра) прилиты четыре бобышки для крепления головки цилиндров болтами.
Крышки коренных подшипников связаны с картерной частью блока коренными и стяжными болтами.
Крышка пятой коренной опоры центрируется в продольном направлении по двум вертикальным штифтам, обеспечивая точность совпадения расточек под упорные полукольца коленчатого вала на блоке и на крышках.
Расточка блока цилиндров под вкладыши коренных подшипников производится в сборе с крышками, поэтому крышки коренных подшипников не взаимозаменяемы и устанавливаются в строго определенном положении. На каждой крышке нанесен порядковый номер опоры, нумерация опор начинается с переднего торца блока.
Параллельно оси расточек под подшипники коленчатого вала выполнены расточки, в которые запрессованы и расточены втулки распределительного вала увеличенной размерности по сравнению с втулками серийного распределительного вала.
В картерной части развала блока цилиндров прилиты направляющие толкателей клапанов.
Ближе к заднему торцу, между четвертым и восьмым цилиндрами, выполнена перепускная труба полости охлаждения для улучшения циркуляции охлаждающей жидкости. Одновременно она придает блоку еще и дополнительную жесткость.
С целью увеличения циркуляционного запаса масла, на двигатель устанавливается масляный насос увеличенной производительности. Поэтому диаметры масляных каналов в блоке цилиндров существенно увеличены.
В нижней части цилиндров заодно с блоком отлиты бобышки под форсунки охлаждения поршней.
С целью установки на блок фильтра с теплообменником на правой стороне увеличены площадка и выполнены два дополнительных крепежных отверстия, а также сливное отверстие из фильтра.
Гильзы цилиндров
Гильзы цилиндров «мокрого» типа, легкосъемные. На конусной поверхности в нижней части, гильзы цилиндров имеют следующую маркировку: устанавливаемые на двигатели 740.11-240 и 740.14-300 — 7406.1002021, на двигатель 740.13-260 — 740.13-1002021.
Гильза цилиндра 7406.1002021 изготавливается из серого специального чугуна, упрочненного объемной закалкой, она отличается уменьшенной (по высоте) зоной отпуска бурта от термообработки гильз, имеющих маркировку 740.1002021-20. Гильза 740.13-1002021 изготавливается из специального, легированного серого чугуна и не термообрабатывается
Установка на двигатели гильз с несоответствующей рекомендациям маркировкой ведет к ускорению износа гильз и поршневых колец.
Зеркало гильзы представляет собой редкую сетку впадин и площадок под углом к оси гильзы. При работе двигателя масло удерживается во впадинах, что улучшает прирабатываемость деталей цилиндропоршневой группы
В соединении гильза — блок цилиндров полость охлаждения уплотнена резиновыми кольцами круглого сечения. В верхней части установлено кольцо в проточке гильзы, в нижней части — два кольца в расточки блока цилиндров.
Привод агрегатов
Привод агрегатов осуществляется шестернями, имеющими прямые зубья, служит для передачи крутящего момента на валы механизма газораспределения, топливного насоса высокого давления, компрессора и насоса гидроусилителя руля автомобиля.
Механизм газораспределения приводится в действие от ведущей шестерни, установленной на коленчатый вал, через блок промежуточных шестерен, которые вращаются на сдвоенном коническом роликовом подшипнике, расположенном на оси, закрепленной на заднем торце блока цилиндров. Шестерня напрессована на конец распределительного вала, причем угловое расположение относительно кулачков вала определяется шпонкой.
Шестерня привода ТНВД установлена на вал привода ТНВД увеличенной размерности.
Поэтому вал привода ТНВД двигателей моделей 740.10 и 7403.10 не взаимозаменяем с валом привода двигателей моделей 740.11; 740.13 и 740.14.
Шестерни устанавливаются на двигатель в строго определенном положении по меткам «Е». «0» и рискам, выбитым на шестернях.
Привод ТНВД осуществляется от шестерни, находящейся в зацеплении с шестерней распределительного вала. Вращение от вала к ГНВД передается через ведущую и ведомую полумуфты с упругими пластинами, которые компенсируют несоосность установки валов ТНВД и шестерни. С шестерней привода ТНВД находятся в зацеплении шестерни привода пневмокомпрессора и насоса гидроусилителя руля.
Привод агрегатов закрыт картером маховика, закрепленным на заднем торце блока цилиндров.
Справа на картере размещен фиксатор маховика, применяемый для установки угла опережения впрыскивания топлива и регулирования тепловых зазоров в механизме газораспределения.
Ручка фиксатора при эксплуатации установлена в верхнем положении. В нижнее положение ее переводят при регулировочных работах, в этом случае фиксатор находится в зацеплении с маховиком. В верхней части картера маховика есть расточки, в которые устанавливаются пневмокомпрессор и насос гидроусилителя руля.
Конструкция картера маховика выполнена под установку одноцилиндрового пневмокомпрессора.
В картере маховика, в отличие от картера маховика, эксплуатируемого с двухцилиндровым пневмокомпрессором, отсутствуют вставка картера маховика и боковой подводящий масляный канал в пневмокомпрессор. Поэтому установка на двигатель двухцилиндрового пневмокомпрессора возможна только с обязательной заменой картера маховика.
По бокам картера маховика в средней части выполнены две бобышки с отверстиями диаметром 21.3 мм для слива масла из турбокомпрессора. Внизу в левой части картера имеется расточка, в которую устанавливается стартер. В середине картера выполнена расточка под манжету коленчатого вала. Со стороны заднего торца выполнена расточка под картер сцепления.
В левой части картера маховика выполнен прилив с фланцем и люком для установки коробки отбора мощности от двигателя. При отсутствии коробки отбора мощности люк закрывается заглушкой, установленной на жидкую прокладку.
Назад к содержанию
Кривошипно-шатунный механизм
Коленчатый вал
Коленчатый вал изготовлен из высококачественной стали и имеет пять коренных и четыре шатунные шейки, закаленных ТВЧ, которые связаны между собой щеками и сопрягаются с ними переходными галтелями. Для равномерного чередования рабочих ходов расположение шатунных шеек коленчатого вала выполнено под углом 90°.
К каждой шатунной шейке присоединяются два шатуна: один для правого и один для левого рядов цилиндров.
Подвод масла к шатунным шейкам производится от отверстий в коренных шейках прямыми отверстиями.
Для уравновешивания сил инерции и уменьшения вибраций коленчатый вал имеет шесть противовесов, отштампованных заодно со щеками коленчатого вала. Кроме основных противовесов, имеются два дополнительных съемных противовеса, напрессованных на вал, при этом их угловое расположение относительно коленчатого вала определяется шпонками.
В расточку хвостовика коленчатого вала запрессован шариковый подшипник.
В полость переднего носка коленчатого вала ввернут жиклер, через калибровонное отверстие которого осуществляется смазка шлицевого валика отбора мощности на привод гидромуфты.
От осевых перемещений коленчатый вал зафиксирован двумя верхними полукольцами и двумя нижними полукольцами, установленными в проточках задней коренной опоры блока цилиндров так, что сторона с канавками прилегает к упорным горцам вала. На переднем и заднем носках коленчатого вала установлены шестерня привода масляного насоса и ведущая шестерня привода распределительного вала. Задний торец коленчатого вала имеет восемь резьбовых отверстий для болтов крепления маховика, передний носок коленчатого вала имеет восемь отверстий для крепления гасителя крутильных колебаний.
Уплотнение коленчатого вала осуществляется резиновой манжетой с дополнительным уплотняющим элементом — пыльником. Манжета размещена в картере маховика. Манжета изготовлена из фторкаучука по технологии формования рабочей уплотняющей кромки непосредственно в прессформе.
Для восстановления двигателя предусмотрены восемь ремонтных размеров вкладышей.
Вкладыши 7405.1005170 РО, 7405.1005171 РО, 7405.1005058 РО применяются при восстановлении двигателя без шлифовки коленчатого вала. При необходимости шейки коленчатого вала заполировываются. Допуски на диаметры шеек коленчатого вала, отверстий в блоке цилиндров и отверстий в нижней головке шатуна при проведении ремонта двигателя должны быть такими же. как у номинальных размеров новых двигателей.
Коренные и шатунные подшипники
Коренные и шатунные подшипники изготовлены из стальной ленты, покрытой слоем свинцовистой бронзы толщиной 0.3 мм, слоем свинцовооловянистого сплава толщиной 0,022 мм и слоем олова толщиной 0.003 мм. Верхние и нижние вкладыши коренных подшипников не взаимозаменяемы.
В верхнем вкладыше имеется отверстие для подвода масла и канавка для его распределения.
Оба вкладыша нижней головки шатуна взаимозаменямы. От проворачивания и бокового смещения вкладыши фиксируются выступами (усами), входящими в пазы, предусмотренные в постелях блока, крышках подшипников и в постелях шатуна. Вкладыши имеют конструктивные отличия, направленные на повышение их работоспособности при форсировке двигателя турбонаддувом, при этом изменена маркировка вкладышей на 7405.1004058 (шатунные), 7405.1005170 и 7405.1005171 (коренные). Поэтому при проведении ремонтного обслуживания не рекомендуется замена вкладышей на серийные с маркировкой 740.100.., так как при этом произойдет существенное сокращение ресурса двигателя.
Крышки коренных подшипников
Крышки коренных подшипников изготовлены из высокопрочного чугуна марки ВЧ50. Крепление крышек осуществляется с помощью вертикальных и горизонтальных стяжных болтов 3, 4, 5, которые затягиваются по определенной схеме регламентированным моментом.
Шатун
Шатун стальной, кованый, стержень имеет двутавровое сечение. Верхняя головка шатуна неразъемная, нижняя выполнена с прямым и плоским разъемом. Шатун окончательно обрабатывают в сборе с крышкой, поэтому крышки шатунов невзаимозаменяемы.
В верхнюю головку шатуна запрессована сталебронзовая втулка, а в нижнюю установлены сменные вкладыши. Крышка нижней головки шатуна крепится с помощью гаек, навернутых на болты предварительно запрессованные в стержень шатуна.
На крышке и стержне шатуна нанесены метки спаренности — трехзначные порядковые номера. Кроме того на крышке шатуна выбит порядковый номер цилиндра.
Маховик
Маховик закреплен восемью болтами, изготовленными из легированной стали с двенадцатигранной головкой, на заднем торце коленчатого вала и точно зафиксирован двумя штифтами и установочной втулкой.
С целью исключения повреждения поверхности маховика под головки болтов устанавливается шайба.
На обработанную цилиндрическую поверхность маховика напрессован зубчатый венец, с которым входит в зацепление шестерня стартера при пуске двигателя.
При выполнении регулировочных работ по установке угла опережения впрыска топлива и величин тепловых зазоров в клапанах маховик фиксируется при помощи фиксатора.
При этом конструкция имеет следующие основные отличия от серийной;
- изменен угол расположения паза под фиксатор на наружной поверхности маховика;
- увеличен диаметр расточки для размещения шайбы под болты крепления маховика.
Рассматриваемые двигатели могут комплектоваться различными типами сцеплений.
Гаситель крутильных колебаний
Гаситель крутильных колебаний закреплен восемью болтами на переднем носке коленчатог о вала. С целью исключения повреждения поверхности корпуса гасителя под болты устанавливается шайба. Гаситель состоит из корпуса, в который установлен с зазором маховик.
Снаружи корпус гасителя закрыт крышкой. Герметичность обеспечивается закаткой (сваркой) по стыку корпуса гасителя и крышки. Между корпусом гасителя и маховиком находится высоковязкостная силиконовая жидкость, дозированно заправленная перед заваркой крышки. Центровка гасителя осуществляется шайбой, приваренной к корпусу. Гашение крутильных колебаний коленчатого вала происходит путем торможения корпуса гасителя, закрепленного на носке коленчатого вала, относительно маховика в среде силиконовой жидкости. При этом энергия торможения выделяется в виде теплоты.
При проведении ремонтных работ категорически запрещается деформировать корпус и крышку гасителя.
Гаситель с деформированным корпусом или крышкой к дальнейшей эксплуатации не пригоден.
Поршень
Поршень отлит из алюминиевого сплава со вставкой из износостойкого чугуна под верхнее компрессионное кольцо.
В головке поршня выполнена тороидальная камера сгорания с вытеснителем в центральной части, она смещена относительно оси поршня в сторону от выточек под клапаны на 5 мм.
Боковая поверхность представляет собой сложную овально-бочкообразную форму с занижением в зоне отверстий под поршневой палец. На юбку нанесено графитовое покрытие.
В нижней ее части выполнен паз, исключающий при правильной сборке контакт поршня с форсункой охлаждения при нахождении в НМТ.
Поршень комплектуется тремя кольцами, двумя компрессионными и одним маслосъемным.
Отличительной его особенностью является уменьшенное расстояние от днища до нижнего торца верхней канавки, которое составляет 17 мм. На двигателях, с целью обеспечения топливной экономичности и экологических показателей, применен селективный подбор поршней для каждого цилиндра по расстоянию от оси поршневого пальца до днища. По указанному параметру поршни разбиты на четыре группы 10, 20, 30 и 40. Каждая последующая группа от предыдущей отличается на 0,11 мм. В запасные части поставляются поршни наибольшей высоты, поэтому во избежание возможного контакта между ними и головками цилиндров в случае замены необходимо контролировать надпоршневой зазор. Если зазор между поршнем и головкой цилиндра после затяжки болтов ее крепления будет менее 0,87 мм , необходимо подрезать днище поршня на недостающую до этого значения величину. Поршни двигателей 740.11, 740.13 и 740.14 отличаются друг от друга формой канавок под верхнее компрессионное и маслосъемное кольца, (см. разделы компрессионное и маслосъемное кольца). Установка поршней с двигателей КАМАЗ 740.10 и 7403.10 недопустима. Допускается установка поршней с поршневыми кольцами двигателей 740.13 и 740.14 на двигатель 740.11.
Компрессионные кольца
Компрессионные кольца изготавливаются из высокопрочного, а маслосъемное из серого чугунов. На двигателе 740.11 форма поперечного сечения компрессионных колец односторонняя трапеция, при монтаже наклонный торец с отметкой «верх» должен располагагься со стороны днища поршня. На двигателях 740.13 и 740.14 верхнее компрессионное кольцо имеет форму сечения двухсторонней трапеции с выборкой на верхнем торце, который должен располагаться со стороны днища поршня.
Рабочая поверхность верхнего компрессионного кольца 4 покрыта молибденом и имеет бочкообразную форму. На рабочую поверхность второго компрессионного и маслосъемного колец нанесен хром. Ее форма на втором кольце представляет собой конус с уклоном к нижнему торцу, по этому характерному признаку кольцо получило название «минутное».
Минутные кольца применены для снижения расхода масла на угар, их установка в верхнюю канавку недопустима.
Маслосъемное кольцо
Маслосъемное кольцо коробчатого типа с пружинным расширителем, имеющим переменный шаг витков и шлифованную наружную поверхность. Средняя часть расширителя с меньшим шагом витков при установке на поршень должна располагаться в замке кольца. На двигателе модели 740.11 высота кольца — 5 мм а на двигателях 740.13 и 740.14 высота кольца — 4 мм.
Установка поршневых колец с других моделей двигателей КАМАЗ может привести к увеличению расхода масла на угар.
Для исключения возможности применения не взаимозаменяемых деталей цилиндропоршневой группы при проведении ремонтных работ рекомендуется использовать ремонтные комплекты:
- 7405.1000128-42 — для двигателя 740.11-240;
- 740.13.1000128 и 740.30-1000128 — для двигателей 740.13-260 и 740.14-300.
В ремонтный комплект входят:
- поршень;
- поршневые кольца;
- поршневой палец;
- стопорные кольца поршневого пальца
- гильза цилиндра;
- уплотнительные кольца гильзы цилиндра.
Форсунки охлаждения
Форсунки охлаждения устанавливаются в картерной части блока цилиндров и обеспечивают подачу масла из главной масляной магистрали при достижении в ней давления 0,8 — 1,2 кг/см2 (на такое давление отрегулирован клапан, расположенный в каждой из форсунок) во внутреннюю полость поршней.
При сборке двигателя необходимо контролировать правильность положения трубки форсунки относительно гильзы цилиндра и поршня. Контакт с поршнем недопустим.
Поршень с шатуном
Поршень с шатуном соединены пальцем плавающего типа, его осевое перемещение ограничено стопорными кольцами. Палец изготовлен из хромоникелевой стали, диаметр отверстия 22 мм. Применение пальцев с отверстием 25 мм недопустимо, так как это нарушает балансировку двигателя.
Назад к содержанию
Механизм газораспределения
Механизм газораспределения предназначен для обеспечения впуска в цилиндры свежего воздушного заряда и выпуска из них отработавших газов. Впускные и выпускные клапаны открываются и закрываются в определенных положениях поршня, что обеспечивается совмещением меток на шестернях привода агрегатов при их монтаже.
Механизм газораспределения — верхнеклапанный с нижним расположением распределительного вала. Кулачки распределительного вала в соответствии с фазами газораспределения приводят в действие толкатели. Штанги сообщают качательное движение коромыслам, а они, преодолевая сопротивление пружин, открывают клапаны. Закрываются клапаны под действием силы сжатия пружин.
Распределительный вал
Распределительный вал стальной, кулачки и опорные шейки подвергнуты термообработке ТВЧ; устанавливается в развале блока цилиндров на пяти подшипниках скольжения, представляющих собой стальные втулки, залитые антифрикционным сплавом.
Диаметр втулок на 6 мм больше по сравнению со втулками двигателя мод. 740.10. Распределительный вал увеличенной размерности, измененными фазами газораспределения и ходом клапанов по сравнению с распредвалом двигателя мод. 740.10. На задний конец распределительного вала напрессована прямозубая шестерня. Привод распределительного вала осуществляется от шестерни коленчатого вала через промежуточные шестерни. Шестерни стальные, штампованные с термообработанными зубьями. Для обеспечения заданных фаз газораспределения шестерни при сборке устанавливаются по меткам, выбитым на торцах. От осевого перемещения вал фиксируется корпусом подшипника задней опоры, который крепится к блоку цилиндров тремя болтами. Посадочный диаметр корпуса подшипника задней опоры больше по сравнению с корпусом подшипника двигателя мод. 740.10. Установка корпуса подшипника задней опоры распределительного вала двигателя мод. 740.10 недопустима, так как приведет к аварийному снижению давления масла в системе и преждевременному выходу из строя двигателя.
Клапаны
Клапаны из жаропрочной стали. Угол рабочей фаски клапанов 90°. Диаметр тарелки впускного клапана 51,6 мм, выпускного — 46,6 мм, высота подъема впускного клапана 14,2 мм, выпускного — 13,7 мм. Геометрия тарелок впускных и выпускных клапанов обеспечивают соответствующие газодинамические параметры впуска-выпуска газов и поэтому их замена на клапаны двигателя мод. 740.10 не рекомендуется.
Клапаны перемещаются в направляющих втулках изготовленных из металлокерамики.
Для предотвращения попадания масла в цилиндр и снижения его расхода на угар, на направляющих клапанов устанавливаются резиновые уплотнительные манжеты.
Толкатели
Толкатели тарельчатого типа с профилированной направляющей частью, изготовлены из стали с последующей наплавкой поверхности тарелки отбеленным чугуном. Толкатель подвергнут химико-термической обработке.
Коромысла
Коромысла клапанов стальные, штампованные, представляют собой двуплечий рычаг, у которого отношение большого плеча к меньшему составляет 1.55. Коромысла впускного и выпускного клапанов устанавливаются на общей стойке и фиксируются в осевом направлении пружинным фиксатором. Коромысла клапанов двигателя 740.11-240. в отличие от коромысел двигателя мод. 740.10. не имеют бронзовой втулки.
Направляющие толкателей
Направляющие толкателей отлиты заодно с блоком цилиндpoв.
Штанги
Штанги толкателей стальные, пустотелые с запрессованными наконечниками. Штанги на 3 мм короче штанг двигателя мод. 740.10 и не взаимозаменяемы с ними.
Стойка коромысел
Стойка коромысел чугунная, её цапфы гюдвергнуты термической обработке ТВЧ.
Диаметр цапф на 2 мм больше по сравнению с цапфами стойки коромысел двигателя мод. 740.10.
Пружины
Пружины клапанов винтовые, устанавливаются по две на каждый клапан. Пружины имеют различные направления навивки. Диаметр проволоки наружной пружины 4.8 мм, внутренний — 3,5 мм. Предварительно устанавливаемое усилие пружин 355 Н, суммарное рабочее — 821 Н. Пружины взаимозаменяемы с пружинами двигателя мод. 740.10.
Порядок регулировки зазоров между носиками коромысел и клапанами описан в разделе «Техническое обслуживание».
Головки цилиндров
Головки цилиндров отдельные на каждый цилиндр, изготовлены из алюминиевого сплава. Головка цилиндра имеет полость охлаждения, сообщающуюся с полостью охлаждения блока.
Для усиления днища головки увеличена ее толщина в зоне выпускного канала и выполнено дополнительное ребро по сравнению с головкой цилиндра двигателя мод. 740.10.
Каждая головка цилиндров устанавливается на два установочных штифта, запрессованные в блок цилиндров, и крепится четырьмя болтами из легированной стали. Один из установочных штифтов одновременно служит втулкой для подачи масла на смазку коромысел клапанов. Втулка уплотнена резиновыми кольцами. В головке, по сравнению с головкой двигателя 740.10, увеличено отверстие слива моторного масла из-под клапанной крышки в штанговую полость. Окна впускного и выпускного каналов расположены на противоположных сторонах головки цилиндров. Впускной канал имеет тангенциальный профиль для обеспечения оптимального вращательного движения воздушного заряда, определяющего параметры рабочего процесса и экологические показатели двигателя, поэтому замена на головки цилиндров двигателя мод. 740.10 не допускается.
В головку запрессованы чугунные седла и металлокерамические направляющие втулки клапанов. Седла клапанов имеют увеличенный натяг в посадке по сравнению с седлами двигателя мод. 740.10, и фиксируются острой кромкой. Выпускное седло и клапан профилированы для обеспечения меньшего сопротивления выпуску отработавших газов.
Применение выпускного клапана мод. 740.10 не рекомендуется.
Стык «головка цилиндра — гильза» (газовый стык) — беспрокладочный. В расточенную канавку на нижней плоскости головки запрессовано стальное уплотнительное кольцо. Посредством этого кольца головка цилиндра устанавливается на бурт гильзы. Герметичность уплотнения обеспечивается высокой точностью обработки сопрягаемых поверхностей уплотнительного кольца и гильзы цилиндра. Уплотнительное кольцо дополнительно имеет свинцовистое покрытие для компенсации микронеровностей уплотняемых поверхностей.
Для уменьшения вредных объемов в газовом стыке установлена фторопластовая прокладка-заполнитель. Прокладка-заполнитель фиксируется на выступающем пояске кольца газового стыка за счет обратного конуса с натягом. Применение прокладки заполнителя снижает удельный расход топлива и дымность отработавших газов. Прокладка-заполнитель разового применения.
Для уплотнения перепускных каналов охлаждающей жидкости в отверстия днища головки установлены уплотнительные кольца из силиконовой резины.
Пространство между головкой и блоком, отверстия стока моторного масла и отверстия прохода штанг уплотнены прокладкой головки цилиндра из термостойкой резины.
Перед ввертыванием смазать резьбу болтов слоем графитовой смазки.
После затяжки болтов необходимо отрегулировать зазоры между клапанами и коромыслами. Клапанный механизм закрыт алюминиевой крышкой. Для шумоизоляции и уплотнения стыка «крышка — головка цилиндра» применены виброизоляционная шайба и резиновая уплотнительная прокладка.
Назад к содержанию
Смазочная система двигателя
Смазочная система комбинированная с «мокрым» картером. Система включает масляный насос, фильтр очистки масла, водомасляный теплообменник, картер масляный, маслоналивную горловину, трубку указателя и указатель уровня масла.
Из картера масляный насос подает масло в фильтр очистки масла и через водомасляный теплообменник в главную магистраль, и далее к потребителям. В смазочную систему также включены клапан системы, обеспечивающий давление в главной масляной магистрали 400-550 кПа (4,0-5,5 кгс/см2) при номинальной частоте вращения коленчатого вала двигателя, предохранительный клапан, отрегулированный на давление 931-1127 кПа (9.5-11,5 кгс/см2), перепускной клапан, отрегулированный на срабатывание при перепаде давления на фильтре 150-220 кПа (1,5-2,2 кгс/см2) и термоклапан включения водомасляного теплообменника. При температуре масла ниже 95 °С, клапан открыт и основной поток масла поступает в двигатель минуя теплообменник.
При температуре масла более 110 °С, термоклапан закрыт и весь поток масла проходит через теплообменник, где охлаждается водой. Тем самым обеспечивается быстрый прогрев двигателя после запуска и поддержание оптимального температурного режима в процессе эксплуатации.
Конструктивно термоклапан расположен в корпусе масляного фильтра.
Масляный насос
Масляный насос закреплен на нижней плоскости блока цилиндров. Ведущее зубчатое колесо напрессовано на передний конец коленчатого вала и имеет 64 зуба, ведомое — 52, то есть передаточное отношение 0.8125. Зазор в зацеплении приводных зубчатых колес регулируется прокладками, устанавливаемыми между привалочными плоскостями насоса и блока, который должен быть 0.15-0,35 мм, момент затяжки болтов крепления масляного насоса к блоку должен быть 49-68.6 Н.м (5-7 кгс.м).
Масляный насос шестеренчатый, односек-ционный. Содержит корпус, крышку и шестерни. В крышке расположен клапан смазочной системы, с пружиной. В нагнетающем канале установлен предохранительный клапан, состоящий из шарика, пружины и регулировочных шайб.
Масляный фильтр
Масляный фильтр закреплен на правой стороне блока цилиндров и состоит из корпуса, двух колпаков и, в которых установлены полнопоточный и частично-поточный фильтроэлементы.
Колпаки на резьбе вворачиваются в корпус. Уплотнение колпаков в корпусе осуществляются кольцами.
В корпусе фильтра также расположен перепускной клапан и термоклапан включения водомасляного теплообменника. Очистка масла в фильтре комбинированная. Через полнопоточный фильтроэлемент проходит основной поток масла перед поступлением к потребителям, тонкость очистки масла от примесей при этом составляет 40 мкм. Через частично-поточный фильтроэлемент проходит 3-5 л/мин. где удаляются примеси рашерами более 5 мкм. Из частично-паточного элемента масло сливается в картер. При такой схеме достигается высокая степень очистки масла от примесей.
Масляный картер
Масляный картер штампованный, крепится к блоку цилиндров через резинопробковую прокладку.
Термоклапан
Термоклапан включения водомасляного теплообменника состоит из подпружиненного поршня с термосиловым датчиком. При температуре ниже 93 °С поршень находится в верхнем положении и основная часть потока масла, минуя теплообменник, поступает в двигатель. При достижении температуры масла (95+2) °С омывающего термосиловой датчик, активная масса, находящаяся в баллоне, начинает плавиться и, увеличиваясь в объеме, перемещает шток датчика и поршень. При температуре масла (110+2) °С поршень 13 разобщает полости в фильтре до и после теплообменника и весь поток масла идет через теплообменник.
При превышении температуры масла выше 115 °С срабатывает датчик температуры и на щитке приборов загорается сигнальная лампочка.
Водомасляный теплообменник установлен на масляном фильтре, кожухотрубного типа, сборный. Внутри трубок проходит охлаждающая жидкость из системы охлаждения двигателя, снаружи — масло. Со стороны масла трубки имеют оребрение в виде охлаждающих пластин. Поток масла в теплообменнике четыре раза пересекает трубки с водой, чем достигается высокая эффективность охлаждения масла. На двигатели 740.11-240, 740.13-260 и 740.14-300 устанавливаются два типа теплообменников:
- 740.11-1013200 на двигатель 740.11 -240;
- 740.20-1013200 на двигатели 740.13-260 и 740.14-300, которые отличаются длиной.
Система вентиляции картера
Система вентиляции картера открытая, циклонного типа. Картерные газы отводятся из штанговой полости второго цилиндра, через угольник, в котором установлен завихритель. При работе двигателя картерные газы, проходя через завихритель, получают винтовое движение. За счет действия центробежных сил капли масла, содержащиеся в газах, отбрасываются к стенке трубы и через трубку сливаются обратно в картер.
Очищенные картерные газы удаляются в атмосферу.
Назад к содержанию
Система газотурбинного наддува
Система газотурбинного наддува, за счет использования части энергии отработавших газов, обеспечивает подачу предварительно сжатого воздуха в цилиндры двигателя.
Наддув позволяет увеличить плотность воздуха, поступающего в цилиндры, в том же рабочем объеме сжечь большее количество топлива и, как следствие, повысить литровую мощность двигателя.
Система газотурбинного наддува двигателя состоит из двух взаимозаменяемых турбокомпрессоров, выпускных и впускных коллекторов и патрубков.
Турбокомпрессоры устанавливаются на выпускных патрубках по одному на каждый ряд цилиндров. Выпускные коллекторы и патрубки изготовлены из высокопрочного чугуна ВЧ50. Уплотнение газовых стыков между установочными фланцами турбины турбокомпрессоров, выпускных патрубков и коллекторов осуществляется прокладками из жаростойкой стали. Прокладки являются деталями одноразового использования и при переборках системы подлежат замене. Газовый стык между выпускным коллектором и головкой цилиндра уплотняется прокладкой из асбостального листа, окантованного металлической плакированной лентой.
Выпускные коллекторы выполняются цельнолитыми, крепятся к головкам цилиндров болтами и контрятся замковыми шайбами. Для компенсации угловых перемещений головки болта крепления выпускного коллектора, возникающих при нагреве, под головку болта устанавливается специальная сферическая шайба.
Впускные коллекторы и патрубки выполняются литыми из алюминиевого сплава АК9ч и соединяются между собой при помощи болтов. Стыки между коллекторами и патрубками уплотняются паронитовыми прокладками. Для выравнивания давления между двумя рядами цилиндров впускные коллекторы соединяются объединительным патрубком.
Система турбонаддува двигателя должна быть герметична. При нарушении герметичности выпускного тракта снижается частота вращения ротора турбокомпрессора, а следовательно уменьшается количества воздуха, нагнетаемого в цилиндры, что приводит к увеличению теплонапряженности деталей, снижению мощности и ресурса двигателя. Негерметичность впускного тракта приводит также к вышеперечисленным недостаткам и «пылевому» износу цилиндро-поршневой группы, следовательно преждевременному выходу двигателя из строя.
Смазка подшипников турбокомпрессоров осуществляется от системы смазки двигателя через фторопластовые трубки с металлической оплеткой. Слив масла из турбокомпрессоров осуществляется через стальные трубки в картер двигателя. Трубки слива между собой соединяются резиновым рукавом, который стягивается хомутами.
Воздух в центробежный компрессор поступает из воздухоочистителя, сжимается и подается под давлением во впускной патрубок двигателя. Выпускной патрубок компрессора и впускной патрубок коллектора между собой соединяются теплостойким резиновым рукавом, который стягивается хомутами.
На двигателях устанавливается турбокомпрессор ТКР7Н-1, ТКР7С-9 или его зарубежный аналог S2B/7624TAE/1.00 D9 фирмы «Schwitzer».
Турбокомпрессоры ТКР7С-9 иТКР7Н-1 являются модификациями базовых моделей турбокомпрессоров ТКР7С и ТКР7Н соответственно. В тексте и рисунках приведены описания и изображения базовых моделей, которые являются общими для всех модификаций ТКР.
Турбокомпрессор ТКР7С-9
Турбокомпрессор ТКР7С-9 состоит из центростремительной турбины и центробежного компрессора, соединенных между собой подшипниковым узлом. Турбина с двухзаходным корпусом из высокопрочного чугуна ВЧ40 преобразовывает энергию выхлопных газов в кинетическую энергию вращения ротора турбокомпрессора, которая затем в компрессорной ступени превращается в работу сжатия воздуха.
Ротор турбокомпрессора ТКР7С состоит из колеса турбины с валом, колеса компрессора, маслоотражателя и втулки, закрепленных на валу гайкой. Колесо турбины отливается из жаропрочного сплава по выплавляемым моделям и сваривается с валом из стали трением. Колесо компрессора с загнутыми по направлению вращения назад лопатками выполняется из алюминиевого сплава и после механической обработки динамически балансируется до величины 0,4 г.мм. Подшипниковые цапфы вала ротора закаливаются ТВЧ на глубину 1-1,5 мм до твердости 52-57 HRCэ.
После механической обработки ротор динамически балансируется до величины 0,5 г.мм.
Втулка, маслоотражатель, колесо компрессора устанавливаются на вал ротора и затягиваются гайкой крутящим моментом 7,8-9,8 Н.м (0,8-1 кгс.м). После сборки ротор дополнительно не балансируется, лишь проверяется радиальное биение цапф вала. При значении радиального биения не более 0,03 мм на детали ротора наносятся метки в одной плоскости и ротор допускается на сборку турбокомпрессора.
При установке ротора на корпус подшипников необходимо совместить метки на деталях ротора.
Ротор вращается в подшипниках, представляющих собой плавающие вращающиеся втулки. Осевые перемещения ротора ограничиваются упорным подшипником, защемленным между корпусом подшипников и крышкой. Подшипники выполняются из бронзы БрО10С10.
Корпус подшипников турбокомпрессора с целью уменьшения теплопередачи от турбины к компрессору выполнен составным из чугунного корпуса ВЧ50 и крышки из алюминиевого сплава. Для уменьшения теплопередачи между корпусом турбины и корпусом подшипников устанавливается экран из жаростойкой стали.
В корпусе подшипников устанавливается маслосбрасывающий экран, который вместе с упругими разрезными кольцами предотвращает утечку масла из полости корпуса.
Для устранения утечек воздуха в соединении «корпус компрессора — корпус подшипников» устанавливается резиновое уплотнительное кольцо.
Корпусы турбины и компрессора крепятся к корпусу подшипников с помощью болтов и планок. Такая конструкция позволяет устанавливать их под любым углом друг к другу, что в свою очередь облегчает установку ТКР на двигатель.
Турбокомпрессор ТКР7Н
В отличие от турбокомпрессора ТКР7С, в конструкции турбокомпрессора ТКР7Н применяется изобарный однозаходный корпус турбины и в качестве подшипника бронзовая моновтулка качающегося типа. Ротор турбокомпрессора состоит из колеса турбины с валом, колеса компрессора и маслоотражателя, закрепленных на валу гайкой. Ротор вращается в подшипнике, удерживающемся от осевого и радиального перемещений фиксатором, который с переходником является одновременно и маслоподводящим каналом.
В корпусе подшипника устанавливаются стальные крышки и маслосбрасывающий экран, который вместе с упругими разрезными кольцами предотвращает течь масла из полости корпуса подшипника.
Для уменьшения теплопередачи от корпуса турбины к корпусу подшипника между ними установлен чугунный экран и две стальные прокладки или чугунный экран и окантованная асбостальная прокладка.
Ввиду того, что ротор турбокомпрессора балансируется с высокой точностью, полная разборка и обслуживание агрегата должны осуществляться на специализированных предприятиях, имеющих необходимое оборудование, инструменты и приборы.
Рекомендуемые режимы работы двигателя с турбонаддувом
Во избежание подсоса масла из турбокомпрессоров и попадания его в цилиндры двигателя, на проточные части компрессора и турбины, не рекомендуется длительная, более 10 минут, работа двигателя на режиме холостого хода с частотой вращения коленчатого вала менее 700 мин-1. Это приводит к закоксовыванию поршневых колец, загрязненности проточной част
Новый двигатель КАМАЗ Р6 перешёл в стадию подготовки производства
Портал «Колёса.ру» побывал в Набережных Челнах на заводе КАМАЗ, где выяснил новые подробности о ходе проекта по созданию отечественного двигателя для грузовых автомобилей.
Прежде всего, стоит отметить высокий процент локализации нового КАМАЗ Р6. В настоящее время всего 25% от общего количества деталей и компонентов составляют импортные закупки. Главный инженер КАМАЗа Фёдор Назаров сообщил, что в числе иностранных позиций находятся топливная аппаратура, аналогов которой в России не выпускают, турбокомпрессор и распредвал. Ведутся переговоры по этим наименованиям с Китаем, «чтобы обеспечить санкционную устойчивость продукту». КАМАЗ также ведёт работу с отечественными компаниями: по распредвалу — с саратовским предприятием «Серп и молот», которое и на данный момент является партнёром челнинского завода.
Когда проект только стартовал в 2013 году, по словам Фёдора Назарова, планировалось, что производство будет осуществляться с использованием практически 100% компонентов из-за границы. Сейчас удалось добиться значительных успехов по данному направлению: на долю иностранных позиций деталей приходится 25%. Пул поставщиков для нового двигателя на 90% состоит из компаний, с которыми КАМАЗ работает и в настоящее время. На самом КАМАЗе уже локализовано порядка 100 позиций (к примеру, шестерни ГРМ и масляного поддона; ведутся работы по изготовлению поддона из пластика), 290 — изготавливаются и будут изготавливаться на российских профильных предприятиях.
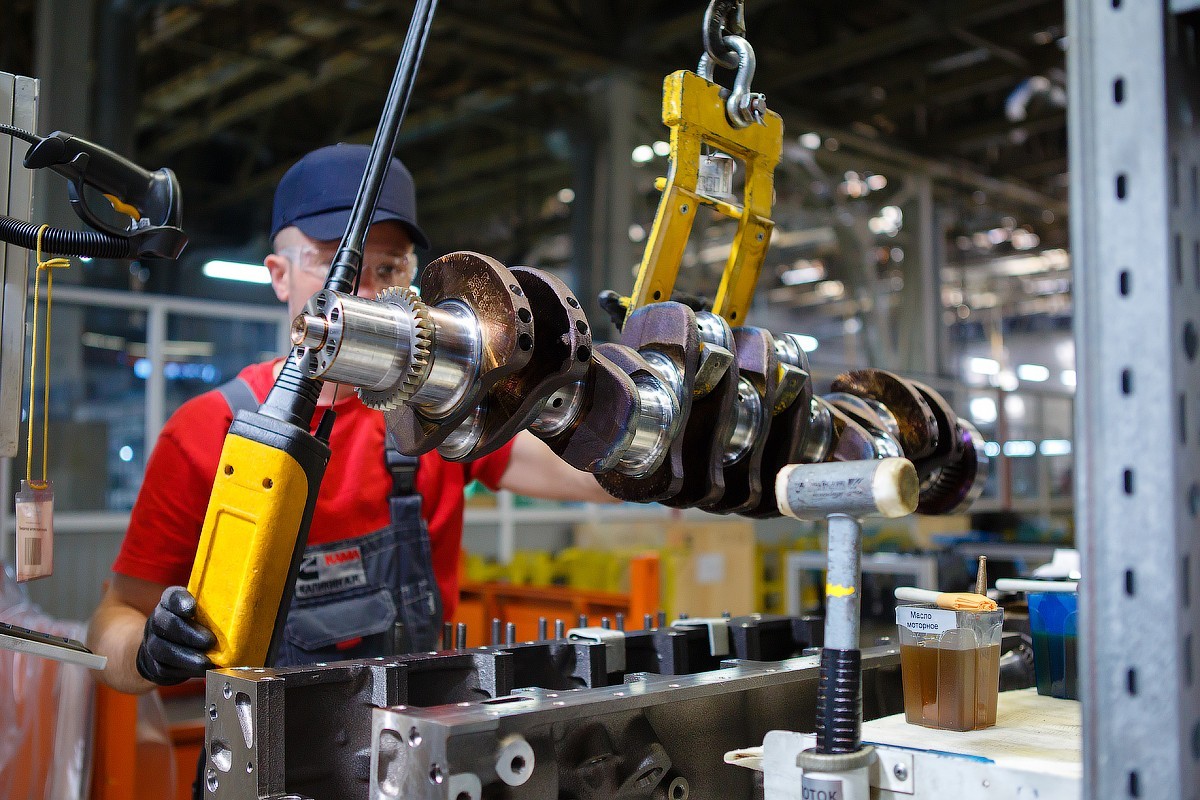
Согласно производственной карте, сейчас проект по созданию нового рядного двигателя для КАМАЗа находится в стадии «подготовка производства». Получена и проработана вся техническая документация серии прототипов двигателей, по которой, собственно, и начинается подготовка. Двигатели, изготовленные в соответствии с этими нормативами, проходят длительные испытания на подтверждение надежности.
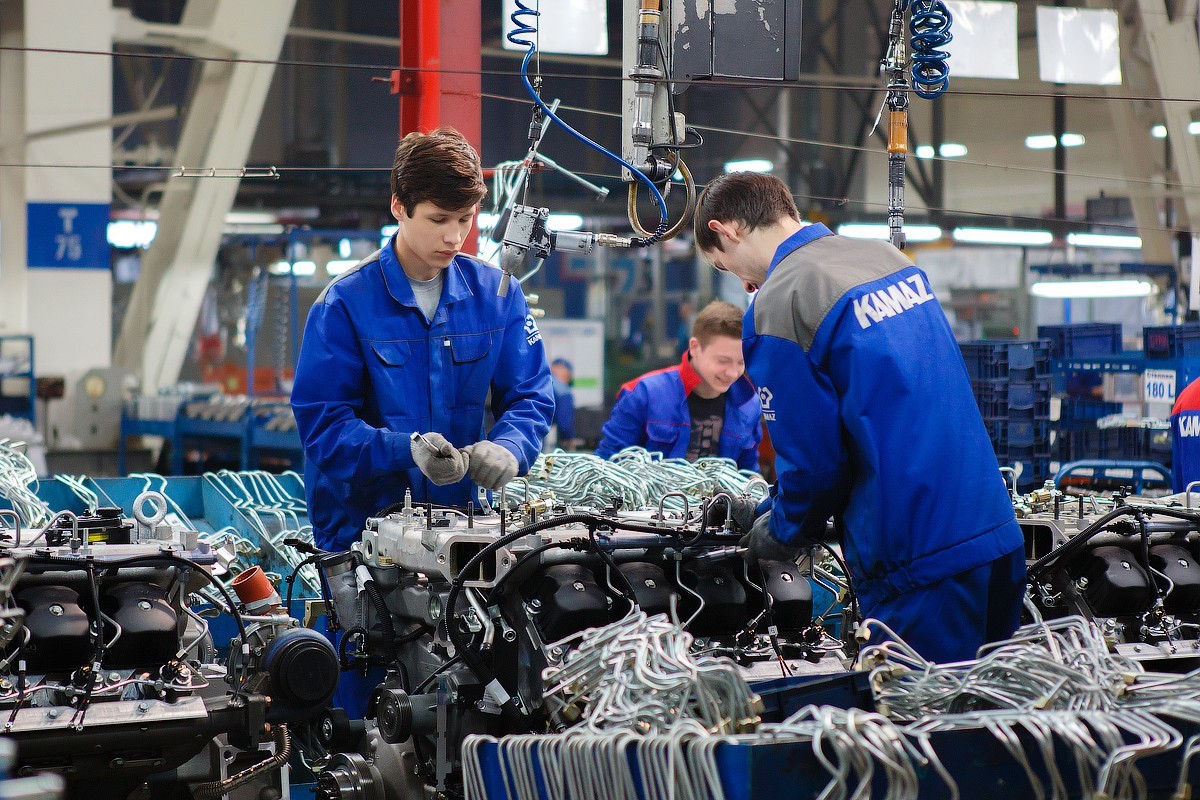
Как сообщал портал «Колёса.ру» ранее, ресурс новой рядной «шестёрки» КАМАЗа составит 1.5 миллиона километров, а межсервисный интервал — 150 000 км (при эксплуатации на дорогах класса «А»). Максимальная мощность КАМАЗ Р6 тоже называлась: двигатель можно будет форсировать до 750 л.с. без внесения существенных изменений в конструкцию. В списке заявленных трансмиссий присутствуют МКП, «робот» и «автомат».
По планам, серийное производство семейства шестицилиндровых двигателей стартует в 2019 году.
Двигатель КАМАЗ серии 7403.10-260 — фото, характеристики, схема, описание
Технические характеристики КПП КАМАЗ 7403.10-260
Руководство по ремонту и обслуживанию КПП КАМАЗ 7403.10-260
Содержание
Сборочные единицы и системы силового агрегата
Двигатель
На автомобили КАМАЗ устанавливаются двигатели моделей КАМАЗ-740.10; КАМАЗ-7403.10 или КАМАЗ-740.11-240.
Особенности конструкции, технического обслуживания и ремонта двигателей КАМАЗ-740.11-240 изложены в руководстве по эксплуатации 740.11-3902006РЭ.
Двигатели КАМАЗ-740.10 и КАМАЗ-7403.10 имеют следующие конструктивные особенности:
- поршни, отлитые из высококремнистого алюминиевого сплава, с чугунной упрочняющей вставкой под верхнее компрессионное кольцо и коллоидно-графитным приработочным покрытием юбки;
- гильзы цилиндров, объемно закаленные и обработанные плосковершинным хонингованием;
- поршневые кольца с хромовым и молибденовым покрытием боковых поверхностей;
- трехслойные тонкостенные сталебронзовые вкладыши коренных и шатунных подшипников;
- закрытую систему охлаждения, заполняемую низко-замерзающей охлаждающей жидкостью, с автоматическим регулированием температурного режима, гидромуфтой привода вентилятора и термостатами;
- высокоэффективную фильтрацию масла, топлива и воздуха бумажными фильтрующими элементами;
- электрофакельное устройство подогрева воздуха, обеспечивающее надежный пуск двигателя при отрицательных температурах окружающего воздуха до минус 25°С.
Назад к содержанию
Блок цилиндров и привод агрегатов
Блок цилиндров отлит из легированного серого чугуна заодно с верхней частью картера. Картерная часть блока связана с крышками коренных опор поперечными болтами-стяжками, что придает прочность конструкции. Для увеличения продольной жесткости наружные стенки блока выполнены криволинейными. Бобышки болтов крепления головок цилиндров представляют собой приливы на поперечных стенках, образующих водяную рубашку блока.
Техническая характеристика
Фазы газораспределения впускного клапана:
- открытие (до в.м.т.) — 13°
- закрытие (после в.м.т.) — 49°
То же выпускного клапана:
- открытие (до в. м.т.) — 66°
- закрытие (после в.м.т.) — 10°
Давление масла в прогретом двигателе, кПа (кгс/см 2 ):
- при номинальной частоте вращения — 400,2-550,4 (4,0…5,5)
- при минимальной частоте вращения холостого хода, не менее — 98,1 (1,0)
Форсунки (закрытого типа) мод. 33 мод. 271
Давление начала подъема иглы форсунки, МПа (кгс/см 2 ):
- бывшей в эксплуатации …. 20 (200) <21,5 (215)
- новой (заводской 22,0…22,7 23,5…24,2 регулировки) — (220…227) (235…242)
Система наддува — газотурбинная с двумя турбокомпрессорами.
Левый ряд цилиндров смещен относительно правого вперед на 29,5 мм, что вызвано установкой на одной кривошипной шейке коленчатого вала двух шатунов.
Спереди к блоку крепится крышка, закрывающая гидромуфту привода вентилятора, сзади — картер маховика, который служит крышкой механизма привода агрегатов, расположенного на заднем торце блока.
Гильзы цилиндров «мокрого» типа легкосъемные, изготовлены из специального чугуна, объемно закалены для повышения износостойкости.
Зеркало гильзы обработано плосковершинным хонингованием для получения сетки впадин и площадок под углом к оси гильзы. Такая обработка способствует удержанию масла во впадинах и лучшей прирабатываемости гильзы.
В соединении гильза — блок цилиндров водяная полость уплотнена резиновыми кольцами круглого сечения. В верхней части установлено кольцо под бурт в проточку гильзы, в нижней части два кольца установлены в расточки блока.
Привод агрегатов шестереночный с прямозубыми шестернями, газораспределительный механизм приводится в действие от ведущей шестерни, установленной с натягом на хвостовике коленчатого вала, через блок промежуточных шестерен. Блок промежуточных шестерен вращается на сдвоенном коническом роликоподшипнике. Шестерня распределительного вала установлена на хвостовик вала с натягом. При сборке надо следить, чтобы метки на торце шестерен, находящихся в зацеплении, были совмещены.
Привод топливного насоса высокого давления осуществляется от шестерни, находящейся в зацеплении с шестерней распределительного вала. Вращение к топливному насосу высокого давления передается через ведущую и ведомую полумуфты с упругими пластинами, которые компенсируют несоосность.
С шестерней привода топливного насоса находятся в зацеплении шестерня привода компрессора и шестерня привода насоса гидроусилителя руля.
Моменты затяжки болтов крепления оси промежуточных шестерен 49,1…60,8 Н . м (5…6,2 кгс.м), болта крепления роликоподшипника 88,3… 98,1 Нм (9…10 кгс.м).
Окружной зазор в шестернях привода агрегатов — 0,1…0,3 мм.
Назад к содержанию
Кривошипно-шатунный механизм
Коленчатый вал стальной, изготовлен горячей штамповкой, упрочен азотированном или закалкой токами высокой частоты шатунных и коренных шеек.
Коленчатый вал имеет пять коренных опор и четыре шатунные шейки. В шатунных шейках вала выполнены внутренние полости, закрытые заглушками, где масло подвергается дополнительной центробежной очистке. Полости шатунных шеек сообщаются наклонными отверстиями с поперечными каналами в коренных шейках.
На носке и хвостовике коленчатого вала установлены шестерня привода масляного насоса и ведущая шестерня в сборе с маслоотражателем. Выносные противовесы съемные, закреплены на валу прессовой посадкой.
Осевые перемещения коленчатого вала ограничены четырьмя сталеалюминиевыми полукольцами, установленными в проточках задней коренной опоры так, чтобы сторона с канавками прилегала к упорным торцам вала, а ус входил в паз на крышке заднего коренного подшипника.
Хвостовик коленчатого вала уплотнен резиновым самоподжимным сальником, установленным в картере маховика.
Маховик из серого специального чугуна, закреплен болтами на заднем торце коленчатого вала и зафиксирован двумя штифтами и установочной втулкой. Зубчатый венец посажен на маховик по горячепрессовой посадке и служит для пуска двигателя стартером. Число зубьев венца маховика 113.
На наружной поверхности маховика имеется паз под фиксатор маховика, который используется при регулировании двигателя.
Шатуны стальные, двутаврового сечения; нижняя головка выполнена с прямым и плоским разъемом. Шатун окончательно обработан в сборе с крышкой, поэтому крышки шатунов невзаимозаменяемы. На крышке и шатуне нанесены метки спаренности в виде трехзначных порядковых номеров. При сборке метки на шатуне и крышке должны находиться с одной стороны. Кроме того, на крышке шатуна выбит порядковый номер цилиндра. На каждой шатунной шейке коленчатого вала установлено по два шатуна. Подшипниками скольжения служат втулка из биметаллической ленты в верхней головке шатуна и съемные взаимозаменяемые вкладыши — в нижней. Крышка шатуна закреплена двумя шатунными болтами с гайками.
Поршни из высококремнистого алюминиевого сплава со вставкой (специальный чугун) под верхнее компрессионное кольцо и коллоидно-графитным покрытием юбки. На поршне установлены два компрессионных кольца L2 и одно маслосъемное кольцо L1. Компрессионные кольца в сечении представляют одностороннюю трапецию, изготовлены из чугуна специального химического состава. Рабочая поверхность верхнего компрессионного кольца покрыта хромом, нижнего — молибденом.
Подбор поршня по расстоянию от образующей шатунной шейки коленчатого вала в верхнем ее положении до уплотнительного бурта гильзы цилиндра | ||
Индекс варианта исполнения поршня | L | L1 |
10 | 260,12… 260,24 | 75,67… 75,71 |
20 | 260,24… 260,35 | 75,78… 75,82 |
30 | 260,35… 260,46 | 75,89… 75,93 |
40 | 260,46… 260,57 | 76,00… 76,04 |
Маслосъемное кольцо прямоугольного сечения с витым пружинным расширителем и хромированной рабочей поверхностью.
В головке поршня расположена камера сгорания. Подбором варианта исполнения поршня, с целью уменьшения надпоршневого зазора, при сборке двигателя обеспечено выступание поршня над уплотнительным торцом гильзы в пределах 0,5…0,7 мм. Индекс варианта поршня нанесен на его днище: 10; 20; 30; 40, а также на нерабочем торце выступа гильзы. В запасные части поставляются поршни с индексом «10», которые при ремонте допускается устанавливать в гильзы с любым индексом.
Поршень с шатуном соединен пальцем плавающего типа, осевое перемещение пальца в поршне ограничено стопорными кольцами. Поршневой палец изготовлен из хромоникелевой стали в виде пустотелого цилиндрического стержня, упрочнен цементацией и закалкой.
Вкладыши подшипников коленчатого вала и нижней головки шатуна сменные, тонкостенные, трехслойные, с рабочим слоем из свинцовистой бронзы. Верхний и нижний вкладыши коренного подшипника колечатого вала невзаимозаменяемы. В верхнем вкладыше имеются отверстие для подвода масла и канавка для его распределения.
Назад к содержанию
Механизм газораспределения
Механизм газораспределения предназначен для впуска в цилиндры воздуха и выпуска отработавших газов. Открытие и закрытие впускных и выпускных клапанов происходит в строго определенных положениях по отношению к верхней и нижней мертвым точкам, которые соответствуют углам поворота шейкиколечатого вала, указанным в диаграмме фаз газораспределения.
Механизм газораспределения двигателя — верхнеклапанный. Кулачки распределительного вала в определенной последовательности приводят в действие толкатели. Штанги сообщают качательные движения коромыслам, которые, преодолевая сопротивление пружин, открывают клапаны. Клапаны закрываются под действием силы сжатых пружин.
Крутящий момент на распределительный вал передается от коленчатого вала через шестерни привода агрегатов.
Головки цилиндров, отлитые из алюминиевого сплава, имеют полости для охлаждающей жидкости, сообщающиеся с рубашкой блока. Стыки головки цилиндра и гильзы, головки и блока уплотнены прокладками. В канавку на привалочной плоскости головки запрессовано кольцо газового стыка, которым головка непосредственно устанавливается на бурт гильзы цилиндра. Герметичность уплотнения обеспечивается высокой точностью обработки сопрягаемых поверхностей кольца и гильзы цилиндра и, дополнительно, нанесением на поверхность кольца свинцовистого покрытия для компенсации микронеровностей уплотняемых поверхностей. Уплотнение перепускных каналов для охлаждающей жидкости осуществляется уплотнительными кольцами из силиконовой резины, устанавливаемыми хвостовиками в отверстия головки цилиндра. Подголовочное пространство, отверстие стока моторного масла и прохода штанг уплотнены формованной прокладкой головки цилиндра.
Впускные и выпускные каналы расположены на противоположных сторонах головки. Впускной канал имеет тангенциальный профиль для завихрения воздуха в цилиндре.
В головку запрессованы чугунные седла и металло-керамические направляющие втулки клапанов, которые растачиваются после запрессовки. Каждая головка закреплена на блоке четырьмя болтами. Клапанный механизм закрыт алюминиевой крышкой, под которой размещена уплотнительная прокладка.
Распределительный вал стальной, поверхности кулачков и опорных шеек цементированы и закалены токами высокой частоты. Вал установлен в развале блока на пяти подшипниках скольжения.
Подшипник задней опоры представляет собой втулку, плакированную бронзой и запрессованную в съемный чугунный корпус. Втулки из биметаллической ленты, запрессованные в поперечные перегородки блока, служат подшипниками для остальных опор вала.
Осевое перемещение распределительного вала ограничено корпусом подшипника, в торцы которого упираются с одной стороны ступица шестерни, с другой — упорный бурт задней опоры шейки вала. Корпус подшипника задней опоры закреплен на блоке тремя болтами.
Толкатели — грибкового типа, пустотелые, с цилиндрической направляющей частью, изготовлены холодной высадкой из стали с последующей наплавкой тарелки отбеленным чугуном. Внутренняя цилиндрическая часть толкателя заканчивается сферическим гнездом для упора нижнего конца штанги.
Клапаны впускной и выпускной изготовлены из жаропрочных сталей. Диаметр головки выпускного клапана меньше диаметра головки впускного клапана. Стержни обоих клапанов на длине 125 мм от торца покрыты графитом для улучшения приработки.
Во время работы двигателя стержни клапанов смазываются маслом, вытекающим из сопряжений коромысел с осями и разбрызгиваемым пружинами клапанов. Для предотвращения попадания масла в цилиндр по зазору стержень клапана — направляющая втулка на втулке впускного клапана установлена резиновая манжета.
Направляющие толкателей, отлитые из серого чугуна, выполнены съемными для повышения ре-монтоспособности и технологичности блока. На двигатель установлены четыре направляющие, в которых перемещаются по четыре толкателя. Каждая направляющая установлена на двух штифтах и прикреплена к блоку цилиндров двумя болтами. Болты застопорены отгибными шайбами.
Штанги толкателей — стальцые, трубчатые, с запрессованными и обжатыми наконечниками. Нижний наконечник имеет выпуклую сферическую поверхность, верхний — выполнен в виде сферической чашечки для упора регулировочного винта коромысла.
Коромысло клапана — стальное, кованое, с бронзовой втулкой, представляет собой двуплечий рычаг, имеющий передаточное отношение 1,55. В короткое плечо коромысла для регулирования зазора в клапанном, механизме ввернут регулировочный винт с контргайкой. Коромысла впускного и выпускного клапанов установлены консольно на осях, выполненных заодно со стойкой коромысел; стойка установлена на штифт и закреплена на головке двумя шпильками. Осевое перемещение коромысел ограничено пружинным фиксатором. К каждому коромыслу через отверстия в стойке коромысла подводится смазка.
Пружины клапанов цилиндрические с равномерным шагом витков и разным направлением навивки. На каждом клапане установлены две пружины. Нижними торцами пружины опираются на головку через стальную шайбу, верхними — в тарелку. Тарелки упираются во втулку, которая соединена со стержнем клапана двумя конусными сухарями. Разъемное соединение втулка — тарелка дает возможность клапанам проворачиваться относительно седла.