Коленчатый вал — Википедия
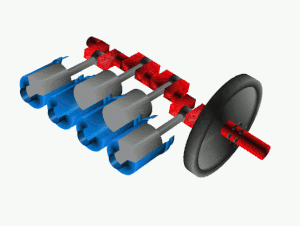
Коленчатый вал — деталь (или узел деталей в случае составного вала) сложной формы, имеющая шейки для крепления шатунов, от которых воспринимает усилия и преобразует их в крутящий момент. Составная часть кривошипно-шатунного механизма (КШМ).
История
Впервые столь важную механическую деталь как коленчатый вал описал и сконструировал средневековый учёный Аль-Джазари в Османской империи в 13 веке. В 1206 году в трактате «Китаб фи марифат аль-хиял аль-хандасийя» (Книга знаний об остроумных механических устройствах) описан механизм вала.
Видео по теме
Основные элементы коленчатого вала
- Коренная шейка — опора вала, лежащая в коренном подшипнике, размещённом в картере двигателя.
- Шатунная шейка — опора, при помощи которой вал связывается с шатунами (для смазки шатунных подшипников имеются масляные каналы).
- Щёки — связывают коренные и шатунные шейки.
- Передняя выходная часть вала (носок) — часть вала на которой крепится зубчатое колесо или шкив отбора мощности для привода газораспределительного механизма (ГРМ) и различных вспомогательных узлов, систем и агрегатов.
- Задняя выходная часть вала (хвостовик) — часть вала соединяющаяся с маховиком или массивной шестернёй отбора основной части мощности.
- Противовесы — обеспечивают разгрузку коренных подшипников от центробежных сил инерции первого порядка неуравновешенных масс кривошипа и нижней части шатуна.
Материал и способы получения заготовок для коленчатых валов
Коленчатые валы изготовляют из углеродистых, хромомарганцевых, хромоникельмолибденовых, и других сталей, а также из специальных высокопрочных чугунов. Наибольшее применение находят стали марок 45, 45Х, 45Г2, 50Г, а для тяжело нагруженных коленчатых валов дизелей — 40ХНМА, 18ХНВА и др. Преимуществом стальных валов является наивысшая прочность, возможность получения высокой твёрдости шеек азотированием, чугунные валы — дешевле.
Заготовки стальных коленчатых валов средних размеров в крупносерийном и массовом производстве изготовляют ковкой в закрытых штампах на молотах или прессах, при этом процесс получения заготовки проходит несколько операций. После предварительной и окончательной ковки коленчатого вала в штампах производят обрезку облоя на обрезном прессе и горячую правку в штампе под молотом.
В связи с высокими требованиями механической прочности вала большое значение имеет расположение волокон материала при получении заготовки во избежание их перерезания при последующей механической обработке. Для этого применяют штампы со специальными гибочными ручьями. После штамповки перед механической обработкой, заготовки валов подвергают термической обработке — нормализация — и затем очистке от окалины травлением или обработкой на дробеметной машине.
Литые заготовки коленчатых валов изготовляют обычно из высокопрочного чугуна, модифицированного магнием. Полученные методом прецизионного литья (в оболочковых формах) валы по сравнению со «штампованными» имеют ряд преимуществ, в том числе высокий коэффициент использования металла и хорошее демпфирование крутильных колебаний, позволяющее часто отказаться от внешнего демпфера на переднем носке вала. В литых заготовках можно получить и ряд внутренних полостей при отливке.
Припуск на обработку шеек чугунных валов составляет не более 2,5 мм на сторону при отклонениях по 5-7-му классам точности. Меньшее колебание припуска и меньшая начальная неуравновешенность благоприятно сказываются на эксплуатации инструмента и «оборудования», особенно в автоматизированном производстве.
Правку валов производят после нормализации в горячем состоянии в штампе на прессе после выемки заготовки из печи без дополнительного подогрева.
Масляные отверстия в коленвалах соединяют обычно соседние коренную и шатунную шейку, и выполняются сверлением. Отверстия в щёках при этом зачеканиваются либо закрываются пробками на резьбе.
Крупноразмерные коленчатые валы, такие как судовые, а также коленвалы двигателей с туннельным картером являются разборными, и соединяются на болтах. Коленвалы могут устанавливаться не только на подшипниках скольжения, но и на роликовых (шатунные и коренные), и шариковых (коренные в маломощных моторах). В этих случаях и к точности изготовления, и к твёрдости предъявляются более высокие требования. Такие валы всегда изготовляют стальными.
Механическая обработка коленчатых валов
Сложность конструктивной формы коленчатого вала, его недостаточная жесткость, высокие требования к точности обрабатываемых поверхностей вызывают особые требования к выбору методов базирования, закрепления и обработки вала, а также последовательности, сочетания операций и выбору оборудования. Основными базами коленчатого вала являются опорные поверхности коренных шеек. Однако далеко не на всех операциях обработки можно использовать их в качестве технологических. Поэтому в некоторых случаях технологическими базами выбирают поверхности центровых отверстий. В связи со сравнительно небольшой жесткостью вала на ряде операций при обработке его в центрах в качестве дополнительных технологических баз используют наружные поверхности предварительно обработанных шеек.
При обработке шатунных шеек, которые в соответствии с требованиями технических условий должны иметь необходимую угловую координацию, опорной технологической базой являются специально фрезерованные площадки на щеках
В большинстве случаев коленчатые валы предусматривают возможность их перешлифовки на ремонтный размер (обычно 4-6 размеров, ранее было до 8). В этом случае коленвалы шлифуют вращающимся наждачным кругом, причём вал проворачивается вокруг осей базирования. Конечно, эти оси для коренных и шатунных шеек не совпадают, что требует перестановки. При перешлифовке требуется соблюсти межцентровое состояние, и согласно инструкции, валы после шлифовки подлежат повторной динамической балансировке. Чаще всего это не выполняют, потому отремонтированные двигатели часто дают большую вибрацию.
При шлифовании важно соблюсти форму галтелей, и ни в коем случае не прижечь их. Неправильная обработка галтелей часто приводит к разрушению коленчатого вала.
Термическая и химико-термическая обработка валов
Коленчатые валы для увеличения прочности и износостойкости шеек подвергают термической, а иногда и химико-термической обработке: закалка ТВЧ, азотирование, закалка поверхностного слоя (стали регламентируемой прокаливаемости 55ПП, 60ПП). Получаемая твёрдость зависит от количества углерода (закалка ТВЧ, обычно не более 50..55 HRC), либо вида ХТО (азотирование даёт твёрдость 60 HRC и выше). Глубина закалённого слоя шеек позволяет обычно использовать 4-6 промежуточных ремонтных размеров шеек вала, азотированные валы не шлифуют. Вероятность задира шейки с ростом твёрдости значительно снижается.
При ремонте коленчатых валов используются также методы напыления, в том числе — плазменного. При этом твёрдость поверхностного слоя может повышаться даже выше заводских значений (для закалки ТВЧ), а заводские диаметры шеек восстанавливают до нулевого размера.
Неисправности и ремонт коленчатых валов
При эксплуатации из-за разных причин могут наблюдаться такие неисправности:
- износ вала по коренным или шатунным шейкам;
- изгиб;
- разрушение вала;
- износ посадочных поверхностей под маховик, сальник (сальники), переднюю шестерню.
При износе шеек выше допустимого или незначительном изгибе, устранимом перешлифовкой, коленчатый вал обрабатывают под следующий ремонтный размер. Однако при больших задирах (например, при выплавлении вкладышей с проворотом) иногда перешлифовывают «через размер», т.е. сразу на 2 размера. Все коренные шейки, а также все шатунные шлифуют в один размер — например, коренные могут быть 2-го ремонтного размера, а шатунные 3-го, в любой комбинации размеров. Коленчатые валы с подшипниками качения и азотированные перешлифовке не подлежат.
Однако руководства по армейскому полевому ремонту (двигатели боевых машин) обычно предписывают индивидуальный ремонт, поэтому шатунные/коренные шейки могут иметь разный диаметр после шлифовки, и даже не иметь стандартного ремонтного размера(!). Вкладыши при этом растачиваются парами, используются заготовки с минимальным внутренним диаметром. Плюсом является наивысшая скорость починки и унификация запчастей (вкладыши).
Разрушение вала происходит от усталостных трещин, возникающих иногда из-за прижога галтелей при шлифовке. Трещины развиваются в некачественном материале (волосовины, неметаллические включения, флокены, отпускная хрупкость) либо при превышении расчётных величин крутильных колебаний (ошибки при проектировании, самостоятельная форсировка по числу оборотов дизеля). Сломанный вал ремонту не подлежит.
При износе посадочных поверхностей могут применяться электрохимическая обработка, плазменная или электродуговая наплавка поверхностей. Коленчатые валы малого размера, возможно, дешевле в таком случае заменить.При образовании канавки от сальника опытные мотористы устанавливают новый так, чтобы он работал по другому месту (например, уменьшив ширину сальника его подтачиванием, или наоборот, садить на меньшую глубину). «Одноразовым» решением при износе посадочной поверхности под шестерню может быть лужение, обычно с предварительным многочисленным кернением поверхности (но шестерню потом трудно или невозможно снять).
См. также
Примечания
Литература
- Кулаев Д. Х. Динамика кривошипно-ползунного механизма с зазорами в шатунных подшипниках // Научный журнал НИУ ИТМО. Серия «Холодильная техника и кондиционирование». — 2009. — ISSN 2310-1148.
Ссылки
Коленчатый вал — Вики
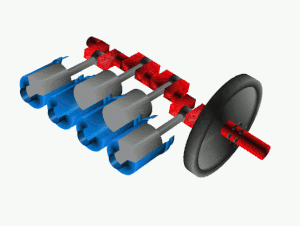
Коленчатый вал — деталь (или узел деталей в случае составного вала) сложной формы, имеющая шейки для крепления шатунов, от которых воспринимает усилия и преобразует их в крутящий момент. Составная часть кривошипно-шатунного механизма (КШМ).
История
Впервые столь важную механическую деталь как коленчатый вал описал и сконструировал средневековый учёный Аль-Джазари в Османской империи в 13 веке. В 1206 году в трактате «Китаб фи марифат аль-хиял аль-хандасийя» (Книга знаний об остроумных механических устройствах) описан механизм вала.
Основные элементы коленчатого вала
- Коренная шейка — опора вала, лежащая в коренном подшипнике, размещённом в картере двигателя.
- Шатунная шейка — опора, при помощи которой вал связывается с шатунами (для смазки шатунных подшипников имеются масляные каналы).
- Щёки — связывают коренные и шатунные шейки.
- Передняя выходная часть вала (носок) — часть вала на которой крепится зубчатое колесо или шкив отбора мощности для привода газораспределительного механизма (ГРМ) и различных вспомогательных узлов, систем и агрегатов.
- Задняя выходная часть вала (хвостовик) — часть вала соединяющаяся с маховиком или массивной шестернёй отбора основной части мощности.
- Противовесы — обеспечивают разгрузку коренных подшипников от центробежных сил инерции первого порядка неуравновешенных масс кривошипа и нижней части шатуна.
Размеры коленчатых валов
Определяются как результат расчётов, причём часть размеров задаётся исходя из выбранной компоновки. Например, количество шатунных шеек определяется в зависимости от числа цилиндров. В многорядных двигателях (V, W, X-образных, звездообразных) одна шатунная шейка воспринимает нагрузки сразу нескольких шатунов (или одного центрального, соединённого с прицепными). Коленчатый вал воспринимает крутящий момент, имеющий переменное значение, а следовательно, работает на скручивание и должен иметь достаточный запас прочности (обычно 2,5) по усталостному напряжению на сдвиг.
Стальные валы (чаще всего) имеют невысокое внутреннее демпфирование крутильных колебаний, что в некоторых случаях угрожает валу разрушением из-за резонанса при прохождении опасной зоны по числу оборотов. Поэтому валы такие снабжают демпферами крутильных колебаний, расположенными на переднем носке вала.
Кроме усталостной прочности, коленвалы должны иметь определённую площадь шеек, задающую контактное давление подшипников скольжения или качения. Максимальное контактное давление и скорость скольжения для антифрикционных материалов может быть несколько повышено при высокой твёрдости шеек и высококачественной смазке. Превышение их выше допустимых ведёт к выплавке/растрескиванию антифрикционного слоя или питтингу роликов (подшипники качения).
Диаметр шатунных шеек (исходя из упомянутых соображений) может быть увеличен косым разъёмом шатуна (что увеличивает его трудоёмкость и стоимость), длину же можно увеличить либо за счёт коренных шеек (что увеличивает контактное давление), либо увеличением расстояния между цилиндрами (что ведёт к увеличению габаритов и массы двигателя). В последние десятилетия, в связи с появлением новых высопрочных антифрикционных сплавов и высококачественных масел, длину шеек валов (а вместе с ним — и межцилиндровое расстояние) конструкторы сокращают.
Материал и технология изготовления заготовок коленчатых валов
Материал и технология изготовления зачастую тесно увязаны между собой. В данном случае, стальные валы (с целью достижения наивысшей прочности и вязкости) получают ковкой, чугунные (материал ковке не поддаётся) — литьём.
Стальные коленчатые валы
Коленчатые валы изготовляют из углеродистых, хромомарганцевых, хромоникельмолибденовых, и других сталей, а также из специальных высокопрочных чугунов. Наибольшее применение находят стали марок 45, 45Х, 45Г2, 50Г, а для тяжело нагруженных коленчатых валов дизелей — 40ХНМА, 18ХНВА и др[1]. Преимуществом стальных валов является наивысшая прочность, возможность получения высокой твёрдости шеек азотированием, чугунные валы — дешевле.
Выбор стали определяется поверхностной твёрдостью шеек, которую нужно получить. Твёрдость около 60 HRC (необходимая для применени
Коленвал ДВС | АВТОСТУК.РУ
Коленчатый вал двигателя внутреннего сгорания, он же коленвал — это однородная деталь (если состоит она из нескольких частей, то это составной вал) сложной формы в виде стержня с коленами, функция которой является преобразование возвратно-поступательного движения в крутящее.
Содержание статьи:
- Металл коленвала.
- Элементы коленевала.
- Назначение коленвала.
- Обработка коленвала.
Металл коленвала
Коленчатый вал ДВС воспринимает большие нагрузки, поэтому он изготавливается с большим запасом прочности. Материалы для изготовления коленвала следующие:
- углеродистая сталь;
- хромомарганцевая сталь;
- хромоникельмолибденовая сталь;
- высокопрочный чугун.
Марки стали состава коленвала в порядке распространенности:
- Сталь 45. Означает, что в сплаве металла содержится от 0,42 до 0,5 % углерода (С).
- Сталь 45Х. Это конструкционный легированный сплав, в котором содержится хром в количестве 1%. Из справочников по ГОСТу хрома содержится в этой марке от 0,8 до 1,1 %.
- Сталь 45Г2. Буква Г в шифре стали означает, что содержится марганец (Mn) в количестве 2%.
- Сталь 50Г. Этот шифр обозначает, что это марганцевая сталь с содержанием 1% марганца (Mn) и 0,5% углерода (С).
Если в шифре сплава металла содержится более, чем 2,14% углерода (С), то — это чугун.
Марки стали коленвалов дизельных двигателей:
- Сталь 40ХНМА.
- Сталь 18ХНВА.
Элементы коленвала
Коленчатый вал (коленвал) ДВС состоит из:
- Коренная шейка.
- Шатунная шейка.
- Щёки.
- Передняя выходная часть вала или, по-другому — носок.
- Задняя выходная часть вала, или, по-другому — хвостовик.
- Противовесы.
Коренная шейка вала коленчатого вала — это специальное посадочное место для коренного подшипника, на котором сидит и вращается коленвал.

Обозначения рисунка «Коленчатый вал ДВС»:
- Фланец маховика.
- Противовесы.
- Шатунные шейки.
- Коренные шейки.
- Щека.
- Отверстия подвода масла к шейкам.
- Противовесы.
- Коренная шейка упорного подшипника.
- Посадочное место звездочки (шестерни) привода распределительного вала.
- Носок коленчатого вала.
В строении коленвала ДВС имеются коренные шейки, соединяющиеся с шатунныйми шейками посредством щёк. Помимо соединительной функции щек, они еще являются балансирами кривошипно-шатунного механизма, то есть выравнивают вес поршней и шатунов. Благодаря сбалансированному вращению коленвалу, двигатель работает плавно, без рывков.
На коренные и шатунные шейки надеваются подшипники скольжения, называемые вкладышами. Вкладыши тонкостенные располовинчатые из стальной ленты с антифрикционным слоем (то есть, устойчивым к трению).
Шатунная шейка является опорой для шатуна. Самой большой нагрузке в строении коленвала ДВС подвергаются места перехода от шеек к щекам.
Чтобы весь коленчатый вал двигателя не перемещался по оси, не имел осевой люфт, используется упорный подшипник скольжения. Подшипник скольжения удерживающий от перемещения по оси коленвала устанавливается на крайней или средней коренных шейках.
В конструкции шеек и щек коленвала конструкторами предусмотрены специальные отверстия для смазки. Через эти отверстия под давлением подается моторное масло к каждой шейке вала. Коренные шейки обеспечены такой индивидуальной смазкой. Через каналы в щеках, масло подается на шатунные шейки.
Задняя часть коленвала — это хвостовик, обеспечивающий передачу крутящего момента маховику, который закрепляется на хвостовике, а маховик, в свою очередь, передает вращение на коробку переключения передач.
Передняя часть коленвала — это носок. На носке монтируются такие детали:
На носке также монтируется, так называемый гаситель крутящих колебаний. Так как коленвал ДВС постоянно испытывает огромные нагрузки на кручение и излом, на носке необходимо подавлять вибрацию (колебания).
Гаситель вибраций коленвала состоит из двух дисков и растягивающегося элемента (резина, силикон, масляная жидкость, пружина). Вибрация на носке вала уменьшается благодаря гасителю крутильных колебаний.
Назначение коленвала
Во всех сложно-технических устройствах происходит возникновение одной одного вида энергии, которая кинематическими схемами преобразуется в другую, например, вращательное — в поступательное, и т.д.
В двигателе ДВС коленчатый вал — это сердце двигателя. Принцип работы коленвала следующий: когда поршень удалился на самое максимальное расстояние — щёки и шатун вытягиваются в одну линию. Далее, в рабочей камере сгорания цилиндра происходит взрыв топливно-воздушной смеси, из-за чего поршень опускается вниз с шатуном. Основание шатуна проворачивается вокруг оси шатунной шейки коленвала, так как шатун сидит на ней. После достижения поворота на 180 градусов, шатун начинает движение вверх и поднимает поршень. Таким образом происходит цикл вращения деталей цилиндро-поршневой группы.
Максимально удаленное и максимально приближенное расстояния от коленвала до поршней называются мертвыми точками, в мертвых точках скорость движения равна нолю.
Обработка коленвала.
Коленвалы ДВС в процессе изготовления подвергаются механической и химико-термической обработкам. Так как коленчатый вал двигателей — это сложное устройство с высокой точностью, оно делается с высокими квалитетами только на заводах. Механобработка вала, в основном, понятна многим — это изменение формы по заданным параметрам.
Химическая обработка коленвалов — это закалка током высокой частоты (ТВЧ), азотирование, закалка поверхностного слоя. Изношенные азотированные валы не шлифуют, они подлежат замене. Благодаря всем этим хим и термическим обработкам повышается прочность и износоустойчивость.
Автор публикации
15 Комментарии: 23Публикации: 322Регистрация: 04-03-2016Конструкция коленчатого вала
Конструкция и размеры коленчатого вала зависят от числа и расположения цилиндров двигателя, числа коренных и шатунных шеек, размещения шатунов, равномерности чередования рабочих ходов и уравновешенности.
Коленчатые валы могут быть как целые, так и составные. Последние применяют в случае использования подшипников качения в качестве шатунных и коренных подшипников.
Коленчатый вал состоит из следующих элементов: переднего конца вала, шатунных и коренных шеек, противовесов и хвостовика.
На коленчатом валу обычно располагаются маховик, ведущая распределительная шестерня, шкив привода вентилятора, гаситель крутильных колебаний, маслоотражатели и другие второстепенные детали.
Общая длина кривошипа, а также размеры составляющих его элементов (коренная и шатунные шейки и щеки) зависят от минимального расстояния между осями двух соседних цилиндров.
В быстроходных дизелях и некоторых карбюраторных двигателях число коренных подшипников коленчатого вала на единицу больше числа колен. Карбюраторные двигатели часто имеют непол-ноопорные коленчатые валы. В «этом случае между двумя коренными подшипниками располагается по два колена, вследствие чего сокращается длина коленчатого вала и габаритные размеры двигателя.
Чтобы повысить жесткость таких коленчатых валов на изгиб, увеличивают диаметры шатунных и коренных шеек, уменьшают их длину и увеличивают толщину щек. В V-образных двигателях применяют полноопорные коленчатые валы.
Современные четырехцилиндровые карбюраторные двигатели с рядным расположением цилиндров обычно имеют три или пять коренных подшипников, а восьмицилиндровые V-образные двигатели — только пять коренных подшипников. Восьмицилиндровые дизели чаще делают с пятью коренными подшипниками. Шестицилиндровые карбюраторные двигатели могут иметь четыре и семь, а дизели — только семь коренных подшипников.
В подавляющем большинстве случаев коленчатые валы изготовляют цельными.
Исходя из условия равномерности чередования вспышек угол между кривошипами вала четырехтактного однорядного двигателя должен быть равен 720°/£ (где i— число цилиндров). Угол между кривошипами двухтактного двигателя согласно тому же условию должен быть 360°/£. При определении порядка работы двигателя из всех возможных вариантов выбирают порядок, при котором вспышки совершаются поочередно в цилиндрах наиболее удаленных друг от друга. Такой порядок работы несколько улучшает условия, в которых находятся коренные подшипники, и препятствует проникновению отработавших газов из одного цилиндра в другой.
Ниже рассматриваются конструктивные элементы коленчатого вала.
Передний конец коленчатого вала имеет ступенчатую форму, что необходимо для установки на нем шкива привода вентилятора, маслоотражающего устройства, распределительной шестерни и в некоторых случаях гасителя крутильных колебаний, который обычно объединяют в один узел со шкивом вентилятора. Все устройства и детали, расположенные на переднем конце коленчатого вала, стягивают болтом, ввернутым в его торец, или гайкой, навернутой на конец коленчатого вала. При установке коленчатого вала в подшипниках качения на его переднем конце должно быть предусмотрено место для устройства, при помощи которого масло подается в коленчатый вал.
Коренные шейки коленчатого вала выполняют одинакового диаметра. Для фиксирования коленчатого вала от осевых перемещений служит одна из крайних или средняя шейка. Упорные подшипники у большинства двигателей (у дизелей в особенности) располагают со стороны маховика. В некоторых двигателях упорные подшипники устанавливают со стороны механизма газораспределения или у среднего коренного подшипника. При цепном приводе желательно упорный подшипник располагать со стороны переднего конца вала, так как при перекосах условия работы цепи ухудшаются.
Для смазки коренных шеек масло подается из общей масляноймагистрали,расположенной в блок-картере, по каналам в стенках верхней части картера со стороны малонагруженной половины вкладыша.
Щеки коленчатого вала могут быть различной формы: призматические овальные и круглые. У коленчатых валов автомобильных двигателей большей части щеки делают прямоугольной и овальной формы.
Если между опорами расположены два колена, то длина щек увеличивается,аформаихусложняется,чтоусложняетконструкцию вала в целом и увеличивают его массу. Для лучшего
использования материала не работающие, наиболее удаленные отоси коленчатого вала,части щек срезают. Жесткость щеки зависит от перекрытия коренных и шатунных шеек е =^* — R .Чем больше перекрытие шеек, тем больше жесткость и прочность щеки. При этом можно уменьшить толщину щеки без увеличения ее ширины. Величина перекрытия шеек зависит от отношения хода поршня к диаметру цилиндра и диаметра шеек.
Переходы (галтели) от щек к коренным и шатунным шейкам во избежание возникновения больших концентраций напряжения выполняют радиусом около (0,035—0,08) d. Для уменьшения опорной поверхности шейки галтель в некоторых конструкциях состоит из двух-трех сопряженных дуг различных радиусов гг, г2, г3 .
Утолщение щек без увеличения длины двигателя ведет с одной стороны к повышению жесткости кривошипа, и с другой — к уменьшению ширины подшипников. При этом ширина подшипника не должна быть меньше 0,25 d.
При наличии на коленчатом валу противовесов форма щек усложняется.
Противовесы служат для разгрузки коренных подшипников от центробежных сил и моментов, вызываемых этими силами. Первые возникают от неуравновешенных масс колена вала. Для уменьшения массы противовесы следует конструировать так, чтобы их центр тяжести располагался на возможно большем расстоянии от оси коленчатого вала. Масса противовеса составляет 70—80%суммарноймассывращающихсячастей.Противовесыо бычно отковывают или отливают как одно целое со щеками. Толщина противовеса не должна превышать толщины щеки, чтобы приремонте шейки коленчатоговаламожнобыло шлифовать.
В некоторых коленчатых валах сложной конструкции для упрощения их штамповки противовесы изготовляют отдельно. В этом случае противовесы к щекам крепятся специальными болтами 1 или шпильками 2 . Для фиксации головки болтов приваривают к противовесам.
Число и установочный угол противовесов определяют из динамического расчета.
В двигателях с кривошипно-камерной схемой газообмена противовесы, заполняя кривошипную камеру, уменьшают вредное пространство и способствуют созданию требуемого давления продувочного воздуха.
Шатунные шейки коленчатых валов обычно имеют меньший диаметр, чем коренные. При увеличении диаметра шатунной шейки увеличивается нижняя головка шатуна, что ведет к возрастанию вращающихся масс. При уменьшении длины шатунной шейки повышается удельная нагрузка, вследствие чего ухудшаются условия работы масляной пленки. Для уменьшения массы шатунные шейки часто высверливают.
Масло к шатунным шейкам подводится от коренных шеек по просверленным в валу каналам или запрессованным трубкам (в случае полых шеек).
Хвостовик (задний конец) коленчатого вала обычно имеет фланец для установки маховика. При наличии гидравлического сцепления роль маховика играет корпус сцепления. Задний конец коленчатого вала уплотняется с помощью отражательных колец вместе с фетровыми или резиновыми кольцами и винтовой нарезкой на валу, имеющей направление, обратное направлению вращения коленчатого вала.
Маховик крепится к фланцу коленчатого вала болтами. Отверстия под болты располагаются несимметрично, чем достигается установка маховика в строго определенном положении.
В торце фланца имеется отверстие для установки подшипника первичного вала коробки передач.
Технология восстановления коленчатого вала двигателя внутреннего сгорания
Автомобиль давно перестал быть источником поклонения. Транспортное средство имеется почти в каждой второй семье. Некоторые владеют двумя и большим количеством автотранспорта. Иногда возникает необходимость восстановить работоспособность всего авто или его отдельных частей. Сердцем автотранспорта является его двигатель. При необходимости ремонта иногда может возникнуть восстановить коленчатый вал ДВС.
Дорогостоящий ремонт проводится разными способами. Предприятия автосервиса чаще предлагают приобрести мотор с разборки, так как капитальный ремонт требует полно разборки двигателя и замены запасных частей. Но никто не даст гарантии, что подобная замена окажется лучшим выходом из ситуации. Достаточно примеров от автомобилистов, которые утверждают, что установленные ДВС с автомобилей с пробегом, служат значительно меньше ожидаемого срока. Поэтому капитальное восстановление родного двигателя позволит эксплуатировать своего «железного коня» в течение всего расчетного срока жизни.
Особенности производства ДВС
Для ремонта двигателей внутреннего сгорания предусмотрены десятки разных способов, способных вернуть их к жизни. Современные моторы производят на заводах, специализирующихся на выпуск только этой продукции.
Используя несколько базовых изделий энергосиловой установки, разные производители автомобилей выпускают различные модели со своим брендом. Внешне авто могут заметно отличаться друг от друга, а силовой агрегат внутри этих транспортных средств будет один и тот же.
- Мотористы выпускают не один тип мотора, у них предусмотрена линейка ДВС, отличающихся системой впуска, количеством клапанов, наличием или отсутствием турбонаддува, присутствием тех или иных опций. Чаще всего блок и ряд корпусных элементов практически не отличаются.
- Из литейного цеха на последующую доработку на территории механических цехов приходят корпуса и крышки. На металлорежущих станках из заготовок изготавливают детали.
- Сборочные участки собирают узлы и агрегаты. Комплектуются будущие изделия.
- Главный конвейер производит окончательную сборку.
- Потом готовые изделия поступают на участок обкатки. Здесь двигатель устанавливается на обкаточный стенд.
- В течение первых двух часов запуск мотора не производится. Выполняется холодное обкатывание. В результате происходит притирка сопрягающихся деталей. Проверяют наличие дисбаланса у коленчатого вала и других механизмов.
- Потом подается топливо. Двигатель запускается. Ему позволяют поработать на разных режимах в течение часа.
- Отработанное моторное масло сливается, заменяется и фильтр очистки.
- Ставится новый фильтр, заливается свежее масло в картер двигателя. Его упаковывают для реализации на автомобилестроительный завод.
Ремонт моторов
Эксплуатационный ремонт сводится только к регулировкам отдельных узлов. Выполняется техническое обслуживание, при котором заменяют фильтрующие элементы и расходные материалы.
Проверяют работоспособность систем питания, искрообразования, охлаждения, смазки. Современные ДВС оборудованы датчиками, которые регистрируют имеющиеся отклонения от номинальных значений. Используя соответствующие диагностические приборы, проводят экспресс-анализ всех систем ДВС. По возможности восстанавливают регулировки, отлаживают режимы работы.
Двигатели при регулярном выполнении технического обслуживания могут гарантированно работать в течение десятка лет и более. Для проведения капитального ремонта производители предусматривают мероприятия по восстановлению работоспособности.
Наибольшему износу подвержены:
- Цилиндры ДВС. Внутри них происходит процесс горения. Температура горючих газов достигает до 2200…2500 ⁰С. Часть металла может выгорать. На внутренней поверхности образуются задиры, повреждается зеркало цилиндра.
- Изнашиваются поршни, они совершают миллионы возвратно-поступательных движений. В результате происходит износ по наружной поверхности. Уплотнение достигается использованием компрессионных и маслосъемных колец, изготавливаемых из ковкого чугуна. Канавки, в которые устанавливают кольца, изнашиваются.
- Нагрузку от поршней получают шатуны. Они опираются на поршневые пальцы и шатунные шейки. В зоне контакта происходит износ. Увеличивается зазор в пальцах и шатунных шейках.
- Коленчатый вал устанавливается на опоры, после совершения нескольких десятков миллионов оборотов изнашиваются коренные шейки. Зазоры увеличиваются. Моторное масло перестает поступать к шатунам и вытекает через неплотности снова в картер.
Двигатель в разрезе:
1 – распределительный вал; 2 – поршень; 3 – цилиндр; 4 – коренная шейка коленчатого вала; 5 – шатунная шейка коленчатого вала.
Многие детали заменяются довольно легко. Производители ДВС, кроме базовых деталей, производят еще дополнительную партию комплектующих, изготовленных с ремонтными размерами:
- На место изношенных поршней устанавливают новые.
- На хонинговальных станках выполняется полировка внутренней поверхности цилиндров, восстанавливается форма. Внимание! Некоторые производители поступают проще, они комплектуют моторы новыми съемными цилиндрами. Остается только приобрести рем-комплект, и заменить поршневую группу.
- Заменяют поршневые пальцы, предварительно растачивают посадочные отверстия в головке шатунов.
- Шлифуют шатунные и коренные шейки коленчатого вала. У большинства производителей предусмотрены по 3…4 ремонтных размера вкладышей. Поэтому реальный моторесурс может быть продлен в 3…4 раза по сравнению с базовым.
После проведения всех операций собирают двигатель. Ставят его на родной автомобиль.
Схема диагностики коленвала:
Теоретически все выглядит довольно прекрасно. При правильной эксплуатации сердце автомобиля способно работать десятилетиями. Но реальность часто доказывает, что после сравнительно небольшого пробега могут возникнуть проблемы, которые устранить простыми способами затруднительно. Требуется восстанавливать самый сложный узел – коленчатый вал. Это самая дорогая деталь в двигателе. Она нагружается сильнее всех. Поэтому необходим сложный дорогостоящий ремонт.
Как отремонтировать коленчатый вал двигателя?
Коленчатый вал устанавливается на станок. С помощью индикаторных головок выполняют диагностику. Проводят анализ биения поверхностей и величину износа:
Большинство производителей предусматривает возможность шлифовки шеек вала на ремонтные размеры. Обычно они отличаются от номинального значения по 0,25…0,50 мм. После переточки под новое значение устанавливают новые вкладыши. Именно они компенсируют изменение параметра на новое. Для шлифовки используют комбинации станков: токарный и центрово-шлифовальный.
На поверхности видны следы износа:
- На токарный станок в центрах устанавливают коленчатый вал. Возможны две установки: в главном центре вала или центрование по шатунам.
- Потом производится проверка биения. Здесь используют индикаторные головки.
- После уточнения реальных размеров производится уточнение возможных размеров после шлифования.
- Включается станок, подается смазывающая охлаждающая жидкость (СОЖ). Выполняется процесс. Все однотипные шейки шлифуют на свой размер.
- После выполнения работы проверяют значения. Если получен ожидаемый результат, заказ отдается заказчику.
Коленчатый вал после проведения шлифовки поверхностей:
Поверхность отполирована:
Возможный вариант полировки поверхностей шеек коленвала:
Наплавка электрической дугой
Когда износ выходит за допустимые значения, то восстановить одной шлифовкой невозможно. Нужно восстановить изначальный диаметр, а только потом приступать к проточкам и шлифовальным работам.
Самый простой способ заключается в наплавке. Используют специальные электроды, изготовленные из легированных сталей. После наплавки получают наплавленный слой высокой твердости.
Наплавляемые швы:
При выполнении этой операции стремятся выполнить несколько основных требований.
- Нужно отрегулировать процесс так, чтобы основной металл, расположенный на шейках, проплавлялся минимально. Здесь возможны варианты изменения наклона электрода. Его позиционируют в разных направлениях.
- При наплавлении поверхностный слой должен минимально перемешиваться с телом детали. Тогда не произойдет перегрев, который может привести к деформации коленвала и нарушению его геометрии.
- При проведении наплавки сразу после завершения наплавления слоя на определенной шейке нужно оперативно охладить деталь. Поэтому производственный цикл может иметь высокую продолжительность, требуется частое охлаждение изделия.
- Выполняя наплавку, необходимо минимизировать толщину наплавляемого слоя. Последующая обработка механическими приспособлениями обязана быть минимальной. Поэтому сварочное оборудование наносит слой, измеряемый долями миллиметра.
Технология наплавки на поверхность детали:
Несколько ремонтных предприятий, разбросанных по стране, производят восстановление коленчатых валов и других деталей методом наплавки. Особенно актуальна подобная работа для импортных автомобилей, у которых возникают трудности с приобретением ремонтных комплектов запасных частей (у некоторых подобные опции не предусмотрены вообще, изготовитель предусматривает полную замену ДВС).
Внимание! Некоторые предприниматели организуют подобные ремонтные подразделения в своих пунктах технического обслуживания автомобилей. Как показывает практика, такие небольшие производства востребованы. Они дают существенную прибыль для основного производства.
Наплавка в среде флюса
Наплавку проводят под защитой флюса. Это порошкообразная среда, которая ограничивает попадание воздуха в зону образования дуги. Флюс расплавляется и образует плотную корку. После наплавки и остывания металла эту корку сбивают и приступают к шлифовальным и полировальным работам.
Схема процесса наплавки под слоем флюса:
Наплавка в среде защитного газа
При использовании электродов защита зоны сварки происходит за счет расплавления обмазки. Покрытие образует слой, который затем нужно сбивать.
Схема процесса дуговой сварки в среде инертных газов:
1 – электрод; 2 – присадочная проволока; 3 – изделие; 4 – сварной шов; 5 – дуга; 6 – поток защитного газа; 7 – горелка.
Получение наплавленного шва более высокого качества достигается наплавлением проволоки в среде защитного газа. Для удаления кислорода из зоны сварки используют углекислый газ, аргон или газовую смесь, в которой аргон составляет 80 %, а остальную представляет углекислота.
При наплавлении стараются перемещать наплавляемый слой по спирали. Специальные приспособления на станке организуют подачу проволоки в автоматическом режиме. Для этого применяют ходовой винт, он согласует перемещение подающей головки в соответствии с вращением вала на станке.
Наплавка напылением
Перспективным способом восстановления коленчатых валов является напыление на поверхность шеек окислов титана. Напыление выполняется порошком, имеющим размер гранул, измеряемый микронами.
Создается разность потенциалов, в результате которой формируется стабильный процесс притяжения между частицами порошка и телом восстанавливаемой детали. Чтобы увеличить интенсивность процесса создается струя, в которой разность потенциалов достигает десятки тысяч Вольт. Попутно происходит разогрев струи, температура повышается до 4000…6000 ⁰С. Длительность процесса составляет всего несколько долей секунды. Поток порошка направляется на поверхность. Между частицами и телом детали возникает диффузия. Частичка припаивается к поверхности.
Газопламенное напыление окиси титана:
Внимание! Твердость окислов титана достигает до HRC 65…75. Такая твердость у стали и ее сплавов недостижима. Поэтому износ порошкового напыления на коленвалах может достигать миллионных пробегов автомобиля. Восстановленная деталь «ходит» в несколько раз дольше, чем планируемый ресурс у нового коленчатого вала.
Электроискровое напыление порошка
При плазменном напылении происходит заметный нагрев детали. Чтобы не перегревать весь коленвал, предусматривают иной способ организации припайки частиц. Подаваемый порошок прикатывается роликом.
Между роликом и деталью создается разность потенциалов. Она небольшая, здесь важна сила тока. Она достигает десятков Ампер. В результате в зоне контакта температура увеличивается до 1900…2200 ⁰С. При таких значениях между частицами и порошком образуется прочная диффузионная связь. Теперь покрытие будет удерживаться довольно прочно.
На практике проверено, что получаемая поверхность не представляет идеальное зеркало. При рассмотрении под микроскопом видны небольшие точки. Оказывается, свободное пространство заполняется смазкой. В результате происходит влажный контакт между сопрягаемыми поверхностями.
Установка для электроискрового напыления:
Внимание! Установлено, что обычный двигатель ВАЗ 2106 (1600 см³) совершил пробег более 1200000 км. Его устанавливали в три кузова автомобилей. Те проработали до полного износа, а сам мотор после разборки показал, что износ коренных и шатунных шеек не превысил 0,01…0,02 мм. При таких параметрах не требуется перетачивание до следующего ремонтного размера.
Детонационное напыление
Самым перспективным способом восстановления параметров коленвала считается детонационное напыление. В этом процессе разгон потока порошка из бункера накопителя до поверхности происходит за счет энергии взрыва, произведенного внутри газового потока.
Используется детонационная пушка. У нее присутствует с одного конца охлаждаемый водой ствол. Его заполняет газовая смесь, которая при достижении нужной концентрации может взорваться.
В результате взрыва в ограниченном пространстве возникает струя, скорость которой 1000…1200 м/с. При соударении с твердой поверхностью в результате удара в зоне контакта температура повышается до 2000…2200 ⁰С. Происходит мгновенное разогревание зоны контакта, частица образует с телом жесткую связь. Ее крайне трудно разрушить механическим путем. Микросварка соединяет разнородные порошок и стальную поверхность.
Детонационное напыление твердых порошков:
После «выстрела» производится продувка ствола негорючим газом. Поток попадает не только на ствол, он направляется в зону сварки, охлаждает ее до 20…30 ⁰С. Затем возобновляется процесс. Происходит очередной выстрел. Еще определенное количество порошка подается на наплавку.
Этот способ наплавки (напыления) превосходит по своим параметрам любой другой вариант.
Внимание! Детонационное напыление может осуществляться не только на металлы. Поток порошка приваривается на пластики, керамику, стекло и другие тугоплавкие материалы.
В настоящее время по заказу заинтересованных предприятий может быть спроектировано и изготовлено индивидуальное высокотехнологичное оборудование. Конечно, цена на него может быть достаточно высокой. Высокое качество восстанавливаемых деталей позволит окупить капиталовложения.
Видео: восстановление коленвала.
Заключение
- Восстановление деталей методом наплавления позволяет восстановить первоначальные размеры деталей.
- Электроискровое и детонационное напыление создают поверхностный слой, покрытый порошком, состоящим из окислов титана. Такое покрытие служит в десятки раз дольше, чем оригинальные детали, изготовленные на заводе-изготовителе.
повреждение, симптомы, ремонт и расходы
Что делать, если коленвал неисправен?
Повреждение коленчатого вала встречается редко в современных автомобилях, но тем не менее все же происходит время от времени. Стоит ли в этом случае ремонтировать автомобиль (стоит ли игра свеч)? Какими затратами обернется ремонт коленвала? Отвечаем на наиболее важные вопросы.
Смотрите также: Сломался датчик положения распредвала: симптомы, ремонт, затраты
Коленчатый вал – важный элемент двигателя внутреннего сгорания. Это та деталь, которая превращает кинетическую энергию, получаемую при сгорании топлива в двигателе, в механическую. Также коленвал служит связующим звеном между двигателем и коробкой передач, которая в свою очередь распределяет крутящий момент на колеса. К сожалению, если коленвал выходит из строя из-за дефекта, дорогостоящего ремонта не избежать.
Дефект коленчатого вала: причины и симптомы
В современных машинах повреждение коленвала стало довольно-таки редким явлением. Обычно коленчатый вал может выйти из строя в основном по двум причинам: нехватка моторного масла и превышение нагрузки на двигатель. Последняя причина современным машинам не грозит, поскольку электроника контролирует все функции двигателя и отключает подачу топлива, когда двигатель начинает испытывать повышенную нагрузку. Особенно эта защита актуальна, когда стрелка на тахометре находится на красной отметке.
Получается, подобная защита является своеобразным электронным ограничением оборотов двигателя, точно так же как работает электронный ограничитель скорости, встроенный во все современные автомобили.
Чаще же всего убить коленвал можно нехваткой моторного масла. Когда коленвалу не хватает смазки, это разрушает шатунные подшипники и затем более крупные основные подшипники, в которых вращается коленвал. Однако для наступления фактического ущерба от нехватки масла требуется довольно много времени – примерно до четверти часа, до тех пор, пока остаточное моторное масло в герметичных подшипниках не будет полностью использовано. В такой ситуации из-за сухого трения начнется разрушение подшипников и износ коленвала.
Но почему в современных автомобилях поломка коленвала – более редкое явление, чем в старых машинах? Все дело в том, что во многих современных машинах двигатели оснащены турбиной, которая быстрее выйдет из строя в случае острой нехватки моторного масла. Так что, по сути, коленвал не успеет получить критичный износ.
Тем не менее в некоторых современных автомобилях все же случается поломка коленвала, которая, как правило, дает о себе знать грохотом (громким стуком).
Ремонт и стоимость поврежденного коленчатого вала
К сожалению, ремонт коленвала – очень сложный процесс, который могут делать не многие технические центры. Ведь в этом случае нужна шлифовка коленчатого вала на специальном оборудовании. Вот виды возможных работ при восстановлении изношенного вала:
- чистка каналов
- замена подшипников
Также в некоторых случаях старый коленвал может нуждаться в термообработке. А иногда нужна балансировка коленвала. К сожалению, для этих работ требуются специалисты высокого класса, а также дорогостоящее оборудование.
Также не забывайте, что, прежде чем приступить к ремонту коленвала, нужно его еще демонтировать, а после ремонта поставить на место. Для многих автомобилей это обходится в круглую сумму, так что в итоге будет проще купить новый коленвал, чем ремонтировать старый. Вот для примера расценки на ремонт коленвала в одном из автосервисов Москвы. Причем это еще не высокие ценники.
Логично, что раз придется разбирать мотор, то вместе с ремонтом коленвала придется также проводить и другие работы. В этом случае восстановление работоспособности коленвала может вылиться автовладельцу в круглую сумму. В некоторых случаях будет проще купить контактный подержанный мотор. Можно также обратиться в специализированные компании, которые занимаются восстановлением моторов. В таких компаниях вы можете приобрести уже готовый восстановленный двигатель на свою машину. В этом случае, чтобы уменьшить стоимость восстановленного мотора, вы можете сдать двигатель со сломанным коленвалом в качестве зачета в стоимость восстановленного.
Структура и функция коленчатого вала
Если вы хотите понять функцию коленвала, то, чтобы это было проще, вспомним, что такое велосипедные педали, которые соединены между собой специальным валом. Ваши ноги при вращении педалей выполняют точно такую же роль, которую играют в двигателе поршни, прикрепленные к шатунам, толкающим коленвал. На велосипеде, чтобы вращать колеса, вам нужно крутить педали вверх и вниз.
По сути, наши ноги на велосипеде (если их сравнивать с конструкцией двигателя) представляют собой два поршня с шатунами, которые ходят вверх и вниз в двухцилиндровом моторе. Вместо же звездочки, которая, вращаясь от движения педалей, передает по цепи крутящий момент на заднее колесо, в двигателях внутреннего сгорания используется коленвал, который и преобразует энергию, получаемую от хода поршней и шатунов, в механическую. С одной стороны коленвала расположен маховик, который передает крутящий момент на коробку передач.
Коленчатый вал должен выдерживать высокие нагрузки
Сегодня в современных автомобилях в двигателях используется коленвал, с каждой стороны которого находится подшипник. Со временем подшипники изнашиваются и между ними и поверхностью коленвала появляется люфт, что приводит к износу коленвала.
К счастью, современная конструкция двигателя способна долгое время выдерживать большие нагрузки. В том числе способны выдерживать нагрузку и современные коленчатые валы. Например, в дизельном современном двигателе каждый ход шатуна испытывает от воспламенения топлива нагрузку в 10 000 кг, которая, естественно, передается на коленвал.
Смотрите также: Двигатели, в которых могут загнуться клапана: Зачем они нужны
Итак, на короткое время в одно мгновенье на шатуне присутствует сила, эквивалентная десяти тоннам, которая воздействует на коленвал. И это мы говорим только об одном шатуне. Вы представляете, какую нагрузку получает коленвал в восьмицилиндровом моторе?
И это еще не все. В зависимости от конструкции двигателя коленчатые валы также подвержены вибрациям. Поэтому многие автопроизводители стараются сделать коленчатые валы достаточно прочными и долговечными. Например, коленвал может быть изготовлен из высококачественной стали. Особенно для мощных турбированных высокооборотистых дизельных двигателей.
Для атмосферного (нетурбированного) бензинового двигателя коленвал может быть уже не столь прочен. Поэтому производители часто еще недавно многие коленчатые валы изготавливали из чугуна. Сегодня же в мире наблюдается тенденция по снижению веса автомобиля. В первую очередь двигателя.
Смотрите также: Почему двигатели автомобилей не плавятся?
В итоге вместо чугунных блоков двигателя во многих современных авто стали использоваться блоки цилиндров из алюминия. Также производители стали использовать облегченные поршни и шатуны. Не обошла эта мода на легкое и коленчатые валы, которые также заметно полегчали. Все это, конечно, не добавляет машине надежности и увы, не гарантирует долгий срок службы двигателя.
Ремонт коленчатого вала двигателя — профессионально в СПб!
Коленчатый вал представляет собой деталь сложной формы, имеющую несколько шеек, на которые крепятся шатуны. Коленвал получает от шатунов усилие и затем преобразовывает его в крутящий момент. Является составной частью кривошипно-шатунного механизма. Ремонт коленчатого вала заключается в перешлифовке его шеек, коренных и шатунных, под ремонтный размер.
Содержание статьи:
Устройство коленвала автомобиля, устройство коленчатого вала
Коленчатый вал состоит из следующих основных элементов:
- Коренные шейки – опоры вала, лежащие в коренных подшипниках, расположенных в картере двигателя;
- Шатунные шейки – опоры, с помощью которых вал соединяется с шатунами;
- Щёки (цапфы) коленвала – соединяют коренные и шатунные шейки;
- Выходная часть коленвала – часть коленчатого вала, на которой устанавливается шестерня или шкив отбора мощности для привода ГРМ (газораспределительного механизма) и других вспомогательных агрегатов, узлов и систем;
- Противовесы – разгружают коренные подшипники от центробежных инерционных сил первого порядка, вызванных неуравновешенными массами кривошипа и нижней части шатуна.
Коленчатые валы бывают разборные и неразборные. В автомобилях применяются неразборные коленчатые валы.
Проверка геометрии коленчатого вала
Перед тем, как отправить коленчатый вал на шлифовку, нужно проверить геометрию вала и, уже исходя из результатов проверки, выбирать соответствующую технологию ремонта.
Перед началом проверки вал устанавливают крайними коренными шейками на призмы и с помощью индикаторной стойки измеряют биение средних шеек. Затем проверяют биение поверхностей сальников и хвостовика, с максимальной тщательностью измеряют диаметры коренных и шатунных шеек. Особое внимание обращают на износ средней и крайних коренных шеек, и на эллипсность шатунных шеек. Эллипсность замеряют в нескольких плоскостях для получения более точных измерений.
Исходя из полученных результатов, выбирают способ ремонта. Если величина биения средних коренных шеек вала относительно крайних не превышает 0,1 мм, то выл можно отшлифовать. В случае превышения этого показателя вал необходимо править.
Перед тем, как приступить к ремонту, нужно проконтролировать несколько важных моментов.
Если вал шлифовали ранее, нужно проверить соосность хвостовика и поверхностей сальников коренным шейкам и уточнить наличие вкладышей нужного ремонтного размера. Особенно необходимо такое уточнение при ремонте валов двигателей многих иномарок, так как нередки ситуации, когда вкладышей нужного ремонтного размера нет в продаже, они существуют только в каталогах.
Если вал имеет шейки, сильно перегретые после разрушения подшипников, его следует проверить магнитным дефектоскопом на отсутствие трещин. Трещины, уходящие глубоко в тело вала или явно заметные невооруженным взглядом являются основанием для его выбраковки.
Коленчатый вал также выбраковывается в случае, когда износ шеек превышает максимальный ремонтный размер. В крайнем случае, изношенные шейки вала можно попытаться восстановить методами наварки или наплавки.
Завершает подготовку к ремонту коленчатого вала операция по удалению заглушек и промывке внутренних каналов. Это процедура носит обязательный характер, так как во внутренних каналах скапливается большое количество грязи, которая способна испортить самый качественный ремонт коленчатого вала.
Шлифовка коленчатого вала
Коленчатые валы шлифуют на специализированных шлифовальных станках, имеющих приспособления, которые позволяют смещать ось коренных шеек относительно оси вращения вала в станке. Это нужно для шлифования шатунных шеек. Кроме того, результат ремонта во многом зависит от состояния шлифовального станка и точности его наладки.
До начала шлифовки необходимо провести еще одну проверку. Вал устанавливают в центрах и замеряют биение хвостовика и поверхности заднего сальника, которое не должно превышать 0,01-0,02 мм. Если биение превышает допуск, то будет невозможно шлифовать коренные шейки вала, в этом случае необходима правка центровых фасок вала. Фаски правятся несколькими способами: протачиванием, притиркой и шабрением.
Шлифовать коленчатый вал начинают с шатунных шеек. Это связано с тем, что после обработки шатунных шеек могут резко изменить значение внутренние напряжения в их поверхностном слое, что может быть причиной деформации всего вала. И если сначала были зашлифованы коренные шейки, то их ось изогнется, а шейки получат взаимное, иногда совсем не малое, биение. То есть, вся работа пойдет насмарку.
Таким деформациям особенно подвержены валы, шатунные шейки которых имеют малый диаметр и не имеющие полноценных противовесов. Такие валы стоят на некоторых двигателях Mercedes, Volvo, Chrysler, Lincoln и на многих «японцах».
Иногда перед началом шлифования шатунных шеек необходимо предварительно обработать поверхности вала, которые зажимаются кулачками. Это происходит в случаях, когда такие поверхности являются некондиционными (например, восстановлены наваркой металла). Это нужно для того, чтобы не «потерять» базу для обработки шатунных шеек.
И это опять еще далеко не все. Установив вал в патроны станка необходимо устранить дисбаланс, вызванный смещение вала. Для этого на планшайбах против патронов станка закрепляются специальные балансировочные грузы, масса и расположение которых подбирается исходя из массы самого вала и радиуса кривошипа. Затем нужно добиться совпадения оси вращения вала с осью шейки, подвергаемой обработке. А еще лучше, если получится добиться совпадения с осью «парных» шеек. Это позволит достигнуть наивысшего качества шлифовки. И лишь только после этого можно начинать шлифовать шатунные шейки вала.
Следующий этап ремонта заключается в обработке коренных шеек. Для их обработки коленчатый вал устанавливают в центрах, Задний центр при этом неподвижно фиксируется стопором, чтобы избежать проскальзывания вала в центровой фаске. Также важно, чтобы центра зажимали вал с минимальным усилием, иначе вал в станке деформируется.
Остается только проверить и отрегулировать величину биения различных поверхностей и можно начинать обработку коренных шеек.
Шатунные и коренные шейки начинают шлифовать с тех, которые имеют максимальный износ, чтобы определить в какой они выйдут ремонтный размер.
При грамотном выполнении всех операций по шлифованию коленчатого вала можно добиться того, что конусность, эллипсность и взаимное биение шеек будут иметь лучшие значения, чем у новых валов.
После обработки коленчатого вала на шлифовальном станке обязательно необходимо удалить микронеровности и сгладить острые кромки смазочных отверстий. Такая операция называется доводкой.
Осуществляют доводку двумя способами: суперфинишной обработкой и полировкой.
В первом случае достигается более высокий результат, но процесс довольно сложный, требует применения специального оборудования и применяется в основном в массовом производстве.
Процесс полировки проще и гораздо доступнее. Отшлифованные шейки вала вручную полируют сначала мелкозернистой наждачной бумагой, вставленной в специальные захваты, а затем абразивной пастой.
Конечный результат – надежная и долговечная работа коленчатого вала – во многом зависит профессионализма механика-моториста, характеристик и точности шлифовального оборудования и, конечно, от мастерства специалиста-шлифовщика.
Правка коленвала профессионально!
Править коленчатый вал следует в том случае, когда, как было написано выше, биение средних шеек коленвала превышает 0,1 мм относительно крайних.
Специалистам известно несколько способов правки коленчатого вала, но большинство из них имеют различные недостатки, которые были учтены при разработке уникального способа, получившего название «метод поэлементной холодной правки» или метод Буравцева.
Данный метод позволяет править коленчатые валы, имевшие изначальное биение шеек более 1 мм с конечным результатом всего 0,01 мм! Такой результат не давал ни один из ранее известных способов правки коленчатых валов. Более того, качественная правка способна заменить шлифовку, особенно это касается новых «заводских» коленчатых валов, которые часто имеют недопустимо большое биение (от 0,05 мм и более).
Достижение высокого качества ремонта коленчатого вала возможно только при правильном выполнении всех технологических приемов во время шлифования и доводки рабочих поверхностей шеек и гаптелей коленвала.
Специалисты Автопрайд качественно выполнят необходимые работы по ремонту, шлифовке коленчатых валов двигателей любых автомобилей иностранного производства не старше 2000 года выпуска. Капитальный ремонт двигателя требует серьезного подхода.