Ремонт и сборка двигателя ГАЗ-53 своими руками: видео и пошаговая инструкция
Иногда авто выходит из строя, требуя проведения восстановительных мероприятий. Одной из подобных процедур служит ремонт двигателя ГАЗ 53, который уже давно исчерпал свой гарантийный срок службы. Без автомобилей наша жизнь была бы не только менее интенсивной, но и более скучной. Кроме того, перевозка грузов является одной из приоритетных задач, которая выполняется при помощи автотранспорта. Ярким представителем отечественного автопрома является ГАЗ 53, который прекрасно известен каждому из нас и применяется для различного рода грузоперевозок.


Так выглядит классический грузовик ГАЗ 53
Эта машина представляет собой образец надежности и практичности, что дает возможность использовать ее уже в течении десятков лет. Вернуться к оглавлению
Эксплуатация двигателя и характерные для него неисправности
Легендарный автомобиль ГАЗ 53 во времена своего создания оборудовался двумя вариантами моторов, имеющих множество модификаций. Первым из них был 6-цилиндровый ГАЗ 11, который не нашел своего широкого примечания в данной модели машины. В свою очередь, второй вариант двигателя ЗМЗ 53, имеющий объем 4,25 л, устанавливался гораздо большее число раз. Поэтому на сегодняшний день часто двигатель ГАЗ 53 представляет собой именно ЗМЗ 53. Этот мотор является своеобразным эталоном надежности и долговечности автомобильного двигателя.


Двигатель змз 53 для автомобиля Газ 53
Однако в большинстве случаев он уже давно исчерпал свой запас прочности и попросту самортизировался. Подобное положение вещей нередко приводит к выходу агрегата из строя и необходимости его последующего ремонта. Наиболее часто поломка мотора сопряжена с наличием следующих неисправностей:
- стук шатунных вкладышей;
- прогорание выпускных клапанов;
- увеличение расхода топлива и масла;
- истирание поршневых колец;
- стук верхних втулок или поршней;
- прогорание прокладок блока цилиндров.
Именно эти неполадки наиболее часто приводят к сбою работы двигателя, способному вызвать полную его остановку. Практически все они связаны с нарушениями эксплуатации агрегата. Так, истирание поршневых колец и появление стука в шатунных вкладышах является следствием пренебрежения инструкцией по эксплуатации автомобиля.

В свою очередь, прогорание различных клапанов и прокладок служит прямым следствием перегрева системы, а повышение расхода масла возникает в результате игнорирования профилактических мероприятий. Вернуться к оглавлению
Профилактические мероприятия для двигателя ЗМЗ 53
Профилактика работы двигателя ЗМЗ 53 является гарантией сохранения его оптимальной функциональности и призвана поддерживать работу устройства на должном уровне.
Кроме того, аналогичные мероприятия дают возможность своевременно определить образование каких-либо серьезных повреждений мотора и ликвидировать их с наименьшими затратами.
Именно поэтому данные процедуры имеют огромную важность и позволяют предотвратить образование мелких неисправностей, список которых был приведен выше. В целом, обслуживание двигателя ГАЗ 53 заключается в проведении следующих мероприятий:
- замена смазочной жидкости;
- подтяжка головок блока цилиндров;
- проверка креплений выпускного коллектора;
- контроль количества охлаждающей жидкости;
- регулировка клапанов;
- проверка уровня масла в системе.
Своевременное проведение всех приведенных выше процедур способно послужить залогом успешной работы автомобильного мотора и гарантировать его оптимальную функциональность. Обслуживание машины имеет свои тонкости, которые должны быть непременно учтены.


Система смазки двигателя Газ 53
Как правило, смена смазки должна осуществляться через каждые 5-6 тыс. км для минеральных масел, 10-12 тыс. км — для синтетических. Подтяжка головок имеет смысл лишь после замены прокладок ГБЦ и должна проводиться каждые 2-3 тыс. км точно так же, как и регулировка клапанов. В свою очередь, проверку уровня масла и воды требуется осуществлять ежедневно. Лишь соблюдение этих требований и своевременное их выполнение служит залогом оптимальной функциональности мотора и его эффективности.
Вернуться к оглавлению
Восстановление мотора ГАЗ 53: наиболее серьезные повреждения и проведение капитального ремонта
Пренебрежение профилактическими средствами и игнорирование первичных признаков неисправности двигателя могут привести к достаточно плачевным последствиям, в особенности если он заглохнет в дороге. Подобными факторами, способными полностью вывести автомобиль из строя и даже сказаться на безопасности людей, находящихся в нем, служат следующие состояния:
- стук в моторе;
- клин движущихся элементов двигателя;
- нехарактерный металлический звук при работе;
- критическое понижение уровня масла.
Приведенные выше критерии являются сигналом для немедленного прекращения работы мотора и его полной остановки. В дальнейшем восстановить его работу можно лишь путем капитального ремонта, подразумевающего полную разборку двигателя и замену поврежденной его части.


Ремонт мотора грузовика Газ 53
Наиболее часто капремонт предполагает проведение операций, направленных на реставрацию двигателя. Выглядит перечень этих мероприятий так:
- реставрация поршневой группы;
- замена шатунных и коренных вкладышей коленвала;
- полная замена всех уплотнителей, заглушек и сальников;
- установка нового масляного насоса;
- смена шестеренок коленчатого и распредвала;
- обновление маслосъемных колпачков.
Капитальный ремонт двигателя является достаточно сложным процессом, который способен привести к серьезным материальным затратам. В первую очередь, они заключаются в покупке новых деталей, которые иногда довольно сложно достать. При этом даже проведение полноценной реставрации мотора может не дать положительного результата в виду того, что все остальные системы машины также находятся в крайне изношенном состоянии.


Схема устройство двигателя Газ 53
Вернуться к оглавлениюСамостоятельный ремонт двигателя ГАЗ 53
Починить двигатель ГАЗ 53 своими руками можно, но этот процесс требует определенной подготовки и наличия профессиональных навыков. При этом без теоретических аспектов и четкого понимания структуры работ начинать подобное мероприятие даже не стоит. Мотор является одной из самых сложных систем, присущих автомобилю. Поэтому для того, чтобы полноценно отремонтировать его и получить положительный результат, нужно быть полностью уверенным в собственных силах. В целом, ремонт двигателя ГАЗ 53 заключается в проведении следующих манипуляций:
- снятие двигателя с машины;
- прочистка всех внутренних и внешних поверхностей;
- разборка узлов и конструктивных элементов системы;
- замена поврежденных деталей;
- профилактический осмотр всех соединений и крепежа;
- сборка;
- обкатка;
- монтаж в машину.
Как правило, проблемы с ремонтом двигателя возникают еще на первом этапе, который заключается в снятии мотора с машины. Обусловлены подобные трудности большим весом агрегата, что делает его передвижение крайне сложным и трудоемким процессом. Для того чтобы снять двигатель, необходимо наличие лебедки и помощь 2-3 человек, иначе выполнить действие просто не удастся.


Собранный двигатель на Газ 53
Разобрать и почистить его просто, а вот вернуть все детали на место достаточно сложно. Довольно часто при неумелой сборке некоторые элементы деформируются, а их части не становятся на положенные им места.
Такой мотор не сможет работать в принципе, а все время, ушедшее на проведение ремонтных работ, просто потрачено впустую. Сборка двигателя ГАЗ 53 является наиболее ответственной и кропотливой процедурой, от которой в полной мере зависит работоспособность самосвала ГАЗ 53. Исходя из этого проводить ее следует не спеша, согласно технической документации изделия, плотно устанавливая все детали по своим местам и фиксируя их.
Только так можно быть уверенным в получении положительного результата и функциональности двигателя. По завершении сборки устройства его необходимо обкатать и лишь потом устанавливать обратно под капот легендарного ГАЗ 53. При этом нужно подсоединить все шланги и патрубки и проверить надежность их закрепления. Как видим, процедура ремонта двигателя ЗМЗ 53 является достаточно сложной, но при наличии определенных навыков выполнить ее своими руками все-таки возможно.
Переборка двигателя газ 53
Сборка двигателя автомобиля ГАЗ-53-12
Для сборки двигателя, как и для его разборки, блок цилиндров закрепляют на вращающемся стенде, чтобы обеспечить свободный доступ ко веем деталям и узлам двигателя.
ремонта, из блока предварительно удаляют два установочных штифта, затем картер крепят к блоку болтами. В блок на двух коренных подшипниках устанавливают коленчатый вал. На задний фланец коленчатого вала крепят на специальной стойке индикатор.
Вращая вал, проверяют биение отверстия для центрирующего бурта коробки передач и перпендикулярность заднего торца картера сцепления относительно оси коленчатого вала (рис. 70 и 71). Биение отверстия и торца картера не должно превышать 0,08 мм. Если биение отверстия превышает указанную величину, ослабляют крепление картера к блоку и легкими ударами по фланцу картера добиваются правильной его установки, а затем затягивают крепежные болты. После затяжки болтов отверстия для установочных штифтов в картере сцепления и блоке цилиндров развертывают одновременно до ремонтного размера. Диаметр отверстия должен быть таким, чтобы в развернутых отверстиях не оставалось черноты. Затем в отверстия запрессовывают штифты, диаметр которых на 0,015 — 0,051 мм больше диаметра отверстий. Биение торца картера устраняют шабровкой.
Рис. 70. Проверка концентричности установочного отверстия:
1 — картер сцепления; 2 — приспособление коробки передач в картере сцепления с осью коленчатого вала
Рис. 71. Проверка перпендикулярности заднего торца картера сцепления к оси коленчатого вала
Рис. 72. Проверка величины утопания гильзы в блоке цилиндров
При сборке двигателя соблюдают следующий порядок операций.
Устанавливают в блок цилиндров гильзы цилиндров. Под каждую гильзу устанавливают уплотнительную прокладку. Точность изготовления блока, гильзы цилиндра и толщины прокладки обеспечивают выступание верхнего торца гильзы над привалочной поверхностью блока под головку цилиндров в пределах 0,02 — 0,10 мм.
Примечание. На отдельных двигателях применялся набор уплотнительных прокладок для обеспечения требуемого выступания гильзы. В этом случае перед установкой гильз в блок их подбирают с помощью металлической линейки и щупа следующим образом: гильза, установленная в блок без уплотнительной прокладки, должна утопать относительно привалочной поверхности головки. Линейку устанавливают на привалочную плоскость, а щуп вводят в зазор между линейкой и торцом гильзы (рис. 72). Толщина набора прокладок должна обеспечивать выступание гильзы над привалочной плоскостью в пределах 0,02 — 0,10 мм.
После установки гильз в блок их закрепляют от выпадания специальными втулками-зажимами (см. рис. 46).
Устанавливают в выточки заднего гнезда коренного подшипника блока и сальникодержателя сальник коленчатого вала (асбестовый шнур длиной 120 мм, пропитанный маслографитовой смесью). С помощью специальной оправки шнур опрессовывают в выточках гнезда легким постукиванием молотка, как указано на рис. 73. Не снимая приспособления, подрезают концы шнура, выступающие над плоскостью разъема на 0,5 — 1,0 мм.Срез должен быть ровным.
Сборка коленчатого вала: запрессовывают в гнездо коленчатого вала подшипник первичного вала коробки передач;
устанавливают на вал маховик и закрепляют его, завернув четыре гайки крепления моментом, равным 76 — 83 Н-м. Зашплинтовывают гайки крепления маховика;
привертывают к маховику нажимной диск с кожухом в сборе, предварительно сцентрировав ведомый диск сцепления с помощью оправки по подшипнику в заднем торце коленчатого вала (в качестве оправки может быть использован первичный вал коробки передач). Метки, выбитые на кожухе нажимного диска и маховике около одного из отверстий для болтов крепления кожуха, совмещают (рис. 74).
Рис. 73. Установка сальниковой набивки в саль никодержатель
Болты крепления кожуха затягивают ключом крутящим моментом 20 — 25 Н-м. Ведомый диск сцепления устанавливают демпфером к нажимному диску. Коленчатый вал в сборе с маховиком и сцеплением балансируют на заводе-изгоговителе, поэтому после замены одной из этих деталей вал вновь динамически балансируют. Дисбаланс не должен превышать 30 гс • см. Перед балансировкой коленчатого вала на шатунные шейки надевают грузы массой 2372 г. При балансировке допускается сверление металла маховика на расстоянии 6 мм от зубчатого обода сверлом диаметром 8 мм На глубину не более 10мм, расстояние между центрами отверстий не менее 15 мм.
Если дисбаланс собранною коленчатого вала превышает 180 гс-см, то вал разбирают и балансируют каждую деталь отдельно. Коленчатый вал балансируют динамически. Допустимый дисбаланс 15 гс-см. Остальные детали балансируют статически. Допустимый дисбаланс маховика 35 с-см, ведомого диска сцепления 18 с — см, нажимного диска сцепления с кожухом в сборе 36 гс-см.
Устанавливают вкладыши коренных подшипников в гнезда блока и крышки коренных подшипников. Надевают на переднюю коренную шейку коленчатого вала заднюю шайбу упорного подшипника стороной, залитой антифрикционным сплавом к щеке коленчатого вала. Смазывают чистым моторным маслом вкладыши коренных подшипников и шейки коленчатого вала и укладывают вал в блок цилиндров.
Надевают крышки коренных подшипников на шпильки так, чтобы фиксирующие выступы на верхнем и нижнем вкладышах каждого подшипника были с одной стороны, а номера, выбитые на крышках, соответствовали номерам подшипников блока. При установке передней крышки следят за тем, чтобы фиксирующий усик задней шайбы упорного подшипника вошел в паз крышки и чтобы не было ступеньки между торцами крышки и блока.
Устанавливают крышки на свои места, слегка постукивая по ним резиновым молотком. Устанавливают стопорные пластины. Наворачивают гайки крепления крышек и затягивают их равномерно, следя за тем, чтобы не было перекосов. Окончательно затягивают эти гайки специальным динамометрическим ключом моментом 100— 120 Н * м. Шплинтуют гайки стопорными пластинами, загибая на грань гайки усик стопорной пластины. После затяжки гаек коленчатый вал должен легко вращаться от небольших усилий.
Устанавливают на место сальникодержатель. Перед установкой в пазы сальникодержателя вкладывают резиновые уплотнительные прокладки. На шпильки надевают фасонные плоские и пружинные шайбы и навертывают специальные гайки сальникодержателя.
Ставят переднюю шайбу упорного подшипника стороной, залитой антифрикционным сплавом к носку коленчатого вала так, чтобы своими пазами она установилась на штифты, запрессованное в блок и крышку переднего коренного подшипника.
Надевают стальную упорную шайбу на носок коленчатого вала. Если шайба имеет следы выработки, то ее устанавливают неизношенной стороной к передней шайбе упорного подшипника.
Рис. 75. На прессовка шестерни коленчатого вала
Рис. 76. Проверка осевого зазора коленчатого вала
Устанавливают в паз сегментную шпонку шестерни коленчатого вала и напрессовывают шестерню до упора (рис. 75).
Проверяют осевой зазор коленчатого вала. Для проверки отжимают коленчатый вал к заднему концу двигателя и с помощью щупа определяют зазор между торцом шайбы упорного подшипника и плоскостью бурта первой коренной шейки (рис. 76). Зазор должен быть в пределах 0,075 —0,175 мм.
Порядок сборки шатунно-поршневой группы:
аккуратно подбирают поршни по гильзам;
подбирают поршневые пальцы к шатунам так, чтобы при нормальной комнатной температуре слегка смазанный палец плавно перемещался в отверстии верхней головки шатуна под легким усилием большого пальца (рис. 77). Цвет маркировки пальца должен соответствовать цвету маркировки на бобышках поршня. Подбирать пальцы из другой группы не разрешается;
на специальном приспособлении собирают шатун, поршень и палец. Перед сборкой поршень нагревают в горячей воде до температуры 70 °С. Запрессовка пальца в холодный поршень не допускается, так как это может привести к повреждению поверхности отверстия бобышки поршня, а также к деформации самого поршня. Шатуны и поршни перед сборкой(рис. 78)ориентиру ют следующим образом: для поршней 1, 2, 3 и 4-го цилиндров (см. поз. 1) надпись на поршне ’’Перед” и номер, выштампованный на стержне шатуна, должны находиться на противоположных сторонах, а для поршней 5, б, 7 и 8-го цилиндров (см. поз. II) надпись на поршне и номер на стержне шатуна должны находиться на одной стороне;
устанавливают стопорные кольца поршневых пальцев в канавки бобышек таким образом, чтобы отгиб усика был направлен наружу;
подбирают по гильзам поршневые кольца;
с помощью специального приспособления надевают на поршни поршневые кольца. В одну канавку устанавливают хромированное компрессионное кольцо, во вторую — луженое. Компрессионные кольца внутренней выточкой устанавливают к днищу поршня, Все кольца должны свободно перемещаться в своих канавках.
Рис. 77. Подбор поршневого пальца к шатуну
Рис. 78. Соединение шатуна с поршнем:
I — для установки в 1, 2, 3 и 4-й цилиндры;
II — для установки в 5, 6, 7 и 8-й цилиндры;
1—номер на шатуне;2—метка на крышке шатуна
Вставляют поршни с шатунами в сборе в гильзы цилиндров. Для этого:
перед установкой тщательно протирают салфеткой нижние головки шатунов и шейки коленчатого вала. Устанавливают в нижние головки шатунов вкладыши шатунных подшипников. Прилегание вкладыша к гнезду должно быть плотным. Попадание между вкладышем и шатуном масла или инородных частиц не допускается;
устанавливают коленчатый вал в положение, соответствующее н.м.т. в том цилиндре, куда устанавливается поршень;
разводят замки плоских кольцевых дисков под углом 180° один к другому, а замки осевого и радиального расширителей — под углом 90° по отношению к замкам кольцевых дисков; надевают на шатунные болты предохранительные латунные колпачки, смазывают чистым моторным маслом вкладыши, поршень, шатунную шейку коленчатого вала и гильзу цилиндра и с помощью оправки устанавливают поршень в цилиндр (рис. 79). Перед установкой поршней убеждаются в том, что номер, выбитый на шатуне, соответствует номеру цилиндра, а надпись на поршне ’’Перед” направлена к переднему торцу блока;
Рис. 79. Установка поршня с кольцами в цилиндр
подтягивают шатун за нижнюю головку к шатунной шейке, снимают с болтов предохранительные колпачки, надевают крышку шатуна, проверив соответствие номеров крышки и шатуна. Крышку ставят таким образом, чтобы фиксирующие усики вкладышей были направлены в одну сторону;
затягивают гайки шатуна динамометрическим ключом моментом 68 — 75 Н • м и законтривают их. Стопорную гайку затягивают поворотом на 1,5 — 2 грани от положения соприкосновения торца стопорной гайки с торцом основной гайки или моментом 3 — 5 Н-м. Стопорение гаек шатуна может осуществляться и другим способом: поверхность резьбы болта шатуна смазывается универсальным герметиком ”Унигерм-9”, резьба болта и гайки должны быть тщательно обезжирены. Таким же образом устанавливают остальные поршни.
В СССР самой распространенной моделью грузовых автомобилей стал ГАЗ-53 и его модификации. За более чем тридцать лет, с момента выпуска первой машины, с конвейеров сошло свыше 4 миллионов экземпляров.
Выпускался автомобиль с 1961 по 1992 годы на мощностях Горьковского автозавода.
Двигатель ГАЗ-53
На автомобили ГАЗ-53 устанавливались две основные модели силовых агрегатов: шестицилиндровый ГАЗ-11 и восьмицилиндровый ЗМЗ-53. Второй мотор имел несколько различных модификаций, однако особой разницы в их конструкции нет.
Несмотря на высокое качество сборки и надежность, двигатель ГАЗ-53 со временем требует проведения ремонтных работ.
Обслуживание мотора
Двигатели внутреннего сгорания, относящиеся к семейству ЗМЗ-53, отличаются неплохим рабочим ресурсом и надежностью, однако, как и любые другие силовые агрегаты, требуют проведения регулярного технического обслуживания. К числу подобных профилактических мер можно отнести:
- Смену смазочного материала. Масло в двигатель ГАЗ-53 заливается как минеральное, так и синтетика с полусинтетикой. Менять его приходится каждые 5-6 тысяч километров пробега для первого типа, для второго – каждые 10-12 тысяч. Впрочем, синтетические масла не совсем подходят для такого двигателя, и использовать их нежелательно.
- Регулярная подтяжка креплений впускного коллектора и головок блока цилиндров. В других ситуациях проверяется затяжка раз в 30 тысяч километров, однако можно и чаще. У двигателя слабым местом является именно впускной коллектор, который зачастую идет «винтом». Подтягиваются его гайки очень просто и находятся в свободном доступе.
- Проверка уровня охлаждающей жидкости. Проводить ее желательно перед каждым выездом на автомобиле. Ремонт двигателя ГАЗ-53 зачастую становится последствием недостаточного уровня жидкости в системе охлаждения.
- Проверка клапанов. Их регулировку проводят только после смены прокладок ГБЦ либо если двигатель ГАЗ-53 подвергался серьезному ремонту. В остальных случаях корректировка их работы происходит только если они начинают стучать. Сами по себе клапаны, как правило, из строя не выходят, так что в большинстве случаев их слишком сильно пережимают мастера во время работы. Как показывает практика, лучше, если они будут немного стучать.
Чтобы двигатель ГАЗ-53 работал как можно больше без неисправностей, необходимо регулярно проводить его диагностику, вовремя устранять неполадки и заливать только качественное моторное масло.
Двигатель ГАЗ-53: технические характеристики
Транспортные средства данной марки комплектуются несколькими модификациями силовых агрегатов. Начиная с 1966 года, на автомобили ГАЗ производилась установка двигателя ГАЗ-53. Модель комплектовалась карбюратором К-126Б и имела верхнее расположение клапанов. Нескольким позднее характеристика двигателя ГАЗ-53 изменилась, поскольку карбюратор был заменен на К-135.
У этого мотора небольшой ход поршня и объем цилиндров. Многие придерживаются мнения, что детали других ДВС из одной линейки можно установить на двигатель ГАЗ-53. Технические характеристики этих моторов несколько разные, поэтому их элементы не являются взаимозаменяемыми. Отличаются не только блоки цилиндров, но и ГБЦ, поршневая группа и коленчатый вал.
Диагностика двигателя
Регулярная проверка необходима для блока цилиндров. Если его крепления ослабевают, подтягивают гайки. Прежде чем проводить такие работы, из системы сливается вся охлаждающая жидкость и ослабевается крепление впускной трубы — это позволяет не допускать воздействия подтяжки одной головки цилиндра на остальные.
После проведения таких процедур динамометрическим ключом закручиваются гайки. Такую работу производитель рекомендует осуществлять первые три технических обслуживания, затем ее частоту можно сократить до каждого второго.
Двигатель ГАЗ-53 не требует проведения ремонта при условии использования смазочных материалов и топлива высокого качества. В таком случае образующийся на поршнях и внутри камеры сгорания нагар будет небольшим и не станет оказывать никакого влияния на работу мотора.
Несоблюдение банальных правил может привести к детонации, увеличению расхода и понижению мощности.
Удаление нагара
Двигатель ГАЗ-53 очень просто избавляется от нагара. Для этого необходимо провести чистку стенок камеры сгорания и днища поршней. Нагар содержит большое количество вредных веществ, поэтому при проведении такой процедуры желательно защитить дыхательные пути. С этой целью его нередко промазывают керосином.
Смена деталей коленчатого вала
С целью повышения потенциала двигателя желательно регулярно производить замену вкладышей коленчатого вала и поршневых колец.
Основной причиной обновления вкладышей является резкое снижение давления масла. Если возникает необходимость, замене подлежат и шатунные вкладыши.
Замена поршневых колец
Главным признаком того, что пришла пора менять поршневые кольца, становится увеличение расхода смазочного материала. В норме он составляет 400 г на 100 километров пробега. В комплект поршневых колец входят стальные диски и компрессионное кольцо из чугуна.
С гильз цилиндров во время замены удаляют неизношенный участок пояска, а ГБЦ очищаются от нагара.
Газораспределительный механизм также требует регулярной диагностики. Зазоры клапанов проверяются только при работающем вхолостую двигателе и опущенном до упора толкателе.
Возможные неисправности ДВС ГАЗ-53
У силового агрегата встречаются поломки и неисправности, характерные для любого другого мотора. Для их устранения производится полная разборка и сборка двигателя ГАЗ-53. Причины появления поломок могут быть различными:
- Появление стука латунных вкладышей. Является самой серьезной неисправностью. Приводит к ней низкий уровень масла, износ всех деталей либо сниженное или полностью отсутствующее давление в системе.
- Повышенный расход смазочного материала. Масло может либо протекать через сальники и соединения, либо через поршневые кольца. Также причиной этого может быть забивка сапуна.
- Стуки втулок или поршней шатуна. Для поршней характерно перегорание днища либо выход из строя перегородок между кольцами. Основная причина этого — перегрев двигателя.
- Прогорание выпускных клапанов. Сами по себе они не прогорают, но зачастую можно столкнуться с износом направляющих втулок. Причин этого может быть несколько: попадание моторного масла, низкое качество топлива или отсутствие в клапанах зазора.
- Прогорание прокладок блока цилиндров. Причина — перегрев двигателя, который может привести к искривлению поверхности головок.
Капитальный ремонт двигателя
Мотор ГАЗ-53 при должном уходе крайне редко нуждается в капитальном ремонте, но если это все же случается, то причинами могут быть следующие неисправности:
- Увеличение расхода смазочного материала, причем с заменой колец проблема осталась актуальной.
- Низкое давление в смазочной системе и появление стуков в двигателе.
- Износ всего силового агрегата с исчерпыванием его рабочего ресурса.
- Заклинивание мотора из-за коленчатого вала.
Ремонт двигателя может производиться самостоятельно — производителем выпускается полное руководство по эксплуатации, в котором все действия по смене деталей и возможные неисправности и методы их устранения подробно описаны.
Несмотря ни на что, двигатели, устанавливаемые на ГАЗ-53, отличаются неплохой выносливостью. Учитывая различные «доработки» ДВС и масла, которые порой в него заливают, остается только удивляться его работоспособности. Нередко такой движок может спокойно функционировать годами даже при условии наличия непонятных стуков.
Иногда авто выходит из строя, требуя проведения восстановительных мероприятий. Одной из подобных процедур служит ремонт двигателя ГАЗ 53, который уже давно исчерпал свой гарантийный срок службы. Без автомобилей наша жизнь была бы не только менее интенсивной, но и более скучной. Кроме того, перевозка грузов является одной из приоритетных задач, которая выполняется при помощи автотранспорта. Ярким представителем отечественного автопрома является ГАЗ 53, который прекрасно известен каждому из нас и применяется для различного рода грузоперевозок.
Так выглядит классический грузовик ГАЗ 53
Эксплуатация двигателя и характерные для него неисправности
Легендарный автомобиль ГАЗ 53 во времена своего создания оборудовался двумя вариантами моторов, имеющих множество модификаций. Первым из них был 6-цилиндровый ГАЗ 11, который не нашел своего широкого примечания в данной модели машины. В свою очередь, второй вариант двигателя ЗМЗ 53, имеющий объем 4,25 л, устанавливался гораздо большее число раз. Поэтому на сегодняшний день часто двигатель ГАЗ 53 представляет собой именно ЗМЗ 53. Этот мотор является своеобразным эталоном надежности и долговечности автомобильного двигателя.
Двигатель змз 53 для автомобиля Газ 53
- стук шатунных вкладышей;
- прогорание выпускных клапанов;
- увеличение расхода топлива и масла;
- истирание поршневых колец;
- стук верхних втулок или поршней;
- прогорание прокладок блока цилиндров.
Именно эти неполадки наиболее часто приводят к сбою работы двигателя, способному вызвать полную его остановку. Практически все они связаны с нарушениями эксплуатации агрегата. Так, истирание поршневых колец и появление стука в шатунных вкладышах является следствием пренебрежения инструкцией по эксплуатации автомобиля.
В свою очередь, прогорание различных клапанов и прокладок служит прямым следствием перегрева системы, а повышение расхода масла возникает в результате игнорирования профилактических мероприятий.
Профилактические мероприятия для двигателя ЗМЗ 53
Профилактика работы двигателя ЗМЗ 53 является гарантией сохранения его оптимальной функциональности и призвана поддерживать работу устройства на должном уровне.
Кроме того, аналогичные мероприятия дают возможность своевременно определить образование каких-либо серьезных повреждений мотора и ликвидировать их с наименьшими затратами.
Именно поэтому данные процедуры имеют огромную важность и позволяют предотвратить образование мелких неисправностей, список которых был приведен выше. В целом, обслуживание двигателя ГАЗ 53 заключается в проведении следующих мероприятий:
- замена смазочной жидкости;
- подтяжка головок блока цилиндров;
- проверка креплений выпускного коллектора;
- контроль количества охлаждающей жидкости;
- регулировка клапанов;
- проверка уровня масла в системе.
Своевременное проведение всех приведенных выше процедур способно послужить залогом успешной работы автомобильного мотора и гарантировать его оптимальную функциональность. Обслуживание машины имеет свои тонкости, которые должны быть непременно учтены.
Система смазки двигателя Газ 53
Восстановление мотора ГАЗ 53: наиболее серьезные повреждения и проведение капитального ремонта
Пренебрежение профилактическими средствами и игнорирование первичных признаков неисправности двигателя могут привести к достаточно плачевным последствиям, в особенности если он заглохнет в дороге. Подобными факторами, способными полностью вывести автомобиль из строя и даже сказаться на безопасности людей, находящихся в нем, служат следующие состояния:
- стук в моторе;
- клин движущихся элементов двигателя;
- нехарактерный металлический звук при работе;
- критическое понижение уровня масла.
Приведенные выше критерии являются сигналом для немедленного прекращения работы мотора и его полной остановки. В дальнейшем восстановить его работу можно лишь путем капитального ремонта, подразумевающего полную разборку двигателя и замену поврежденной его части.
Ремонт мотора грузовика Газ 53
- реставрация поршневой группы;
- замена шатунных и коренных вкладышей коленвала;
- полная замена всех уплотнителей, заглушек и сальников;
- установка нового масляного насоса;
- смена шестеренок коленчатого и распредвала;
- обновление маслосъемных колпачков.
Капитальный ремонт двигателя является достаточно сложным процессом, который способен привести к серьезным материальным затратам. В первую очередь, они заключаются в покупке новых деталей, которые иногда довольно сложно достать. При этом даже проведение полноценной реставрации мотора может не дать положительного результата в виду того, что все остальные системы машины также находятся в крайне изношенном состоянии.
Схема устройство двигателя Газ 53
Самостоятельный ремонт двигателя ГАЗ 53
Починить двигатель ГАЗ 53 своими руками можно, но этот процесс требует определенной подготовки и наличия профессиональных навыков. При этом без теоретических аспектов и четкого понимания структуры работ начинать подобное мероприятие даже не стоит. Мотор является одной из самых сложных систем, присущих автомобилю. Поэтому для того, чтобы полноценно отремонтировать его и получить положительный результат, нужно быть полностью уверенным в собственных силах. В целом, ремонт двигателя ГАЗ 53 заключается в проведении следующих манипуляций:
- снятие двигателя с машины;
- прочистка всех внутренних и внешних поверхностей;
- разборка узлов и конструктивных элементов системы;
- замена поврежденных деталей;
- профилактический осмотр всех соединений и крепежа;
- сборка;
- обкатка;
- монтаж в машину.
Сборка двигателя автомобиля ГАЗ-66, ГАЗ-53
Для сборки двигателя, так же как и для его разборки, блок цилиндров двигателя в сборе с картером сцепления закрепляют на стенде (см. рис. 1).
Все детали двигателя перед сборкой подбирают по размерам, тщательно промывают, продувают сжатым воздухом и протирают чистыми салфетками. Все резьбовые соединения (шпильки, пробки, штуцера и т. д.), если они вывертывались при разборке или были заменены, необходимо ставить на сурике или свинцовых белилах, разведенных натуральной олифой.
Неразъемные соединения (заглушки блока и головок цилиндров) ставят на нитролаке.
К постановке на ремонтируемый двигатель не допускаются:
— шплинты и шплинтовочная проволока, бывшие в употреблении;
— пружинные шайбы, потерявшие упругость;
— болты и шпильки с вытянувшейся резьбой;
— гайки и болты с изношенными гранями;
— детали, имеющие на резьбе более двух забоин или вмятин или сорванные нитки резьбы;
— поврежденные прокладки.
Собирают двигатель в порядке, обратном разборке.
Ниже приводятся отдельные рекомендации и дополнительные требования по сборке двигателя.
При замене гильз цилиндров перед установкой гильзу подбирают по гнезду в блоке цилиндров.
Гильзы подбирают при помощи точной металлической линейки и набора щупов следующим образом:
— гильза, установленная на свое место в блоке цилиндров без уплотнительных прокладок, должна утопать относительно привалочной поверхности блока цилиндров.
Линейку устанавливают на привалочную поверхность, а щуп вводят в зазор между линейкой и торцом гильзы (рис. 2).
Толщину прокладки выбирают таким образом, чтобы после установки гильзы с прокладкой было обеспечено возвышение ее над поверхностью блока цилиндров в пределах 0,02—0,09 мм.
Уплотнительные прокладки выпускают различной толщины:
0,3; 0,2; 0,15 и 0,1 мм. В зависимости от зазора на гильзу цилиндра надевают ту или иную прокладку, иногда необходимую величину получают набором прокладок различной толщины.
После установки в блок цилиндров гильзы закрепляют втулками-зажимами (см. рис. 3).
В качестве заднего сальника на двигателях применяют асбестовый шнур, пропитанный масляно-графитовой смесью. В гнезда блока цилиндров и сальникодержателя укладывают шнур длиной 140 мм. При помощи приспособления шнур опрессовывают в своих гнездах легкими ударами молотка, как указано на рис. 4. Не снимая приспособления, подрезают концы шнура заподлицо с плоскостью разъема сальникодержателя. Срез должен быть ровным, разлохмачивание концов и неровный срез не допускаются.
При сборке коленчатого вала с маховиком и сцеплением соблюдают следующие требования.
Гайки крепления маховика затягивают, обеспечивая момент 7,6—8,3 кГм.
При сборке сцепления ведомый диск устанавливают демпфером к нажимному диску и центрируют по подшипнику коленчатого вала (в качестве оправки может быть использован ведущий вал коробки передач).
Метки «О», выбитые на кожухе нажимного диска и маховика около одного из отверстий для болтов крепления кожуха, необходимо совместить.
Коленчатый вал в сборе с маховиком и сцеплением должны быть динамически сбалансированы. Допустимый дисбаланс 70 Гсм.
При балансировке снимают лишнюю массу с тяжелой стороны высверливанием металла маховика на расстоянии 6 мм от зубчатого венца сверлом диаметром 8 мм на глубину не более 10 мм.
Если дисбаланс собранного вала превышает 180 Гсм, вал разбирают и балансируют каждую деталь отдельно. Дисбаланс маховика не должен превышать 35 Гсм; дисбаланс нажимного диска в сборе с кожухом — 36 Гсм; Дисбаланс ведомого диска— 18 Гсм.
Крышки коренных подшипников устанавливают так, чтобы фиксирующие выступы вкладышей находились с одной стороны, а номера или метки, выбитые на крышках, соответствовали номерам постелей. При установке передней крышки необходимо следить, чтобы фиксирующий усик задней шайбы упорного подшипника вошел в паз крышки, и чтобы не образовывалось ступеньки между торцом крышки и торцом блока цилиндров.
Гайки крепления крышек коренных подшипников затянуть (момент 11—12 кГм). После затяжки и шплинтовки гаек крышек коренных подшипников коленчатый вал должен легко вращаться от небольших усилий.
После напрессовки шестерни коленчатого вала (рис. 5) при помощи съемника и упорной втулки проверить осевой зазор коленчатого вала, для чего отжать коленчатый вал к заднему концу двигателя и при помощи щупа определить зазор между торцом задней шайбы упорного подшипника и торцом передней коренной шейки коленчатого вала (рис. 6). Зазор должен быть в пределах 0,075 — 0,175 мм.
При сборке деталей шатунно-поршневой группы необходимо соблюдать следующие требования.
Поршневые пальцы подбирают к шатунам так, чтобы при комнатной температуре (+180 С) слегка смазанный палец плавно перемещался в отверстии шатуна под легким усилием большого пальца руки.
Перед сборкой поршни нагревают в горячей воде до +700 С.
Запрессовка пальца в холодный поршень не допускается, так как это может привести к порче поверхностей отверстий бобышек поршня, а также к деформации самого поршня.
Шатуны и поршни при сборе ориентируют следующим образом: для поршней первого, второго, третьего и четвертого цилиндров надпись на поршне «перед» и номер, выштампованный на стержне шатуна, должны быть направлены в противоположные стороны, а для поршней пятого, шестого, седьмого и восьмого цилиндров — в одну сторону (рис. 7).
Стопорные кольца поршневого пальца устанавливают в канавки бобышек поршня так, чтобы отгиб усика был направлен наружу.
Поршневые кольца подбирают по гильзам, в которых они будут работать. Зазор, замеренный в стыке кольца, уложенного в гильзу, должен быть в пределах 0,3—0,5 мм для компрессионных и маслосъемных колец. В верхнюю поршневую канавку устанавливают хромированное, а во вторую — луженое компрессионное кольцо выточкой на внутренней стороне к днищу.
Перед установкой в гильзы цилиндров стыки поршневых колец расположить под углом в 120° друг к другу, а на шатунные болты следует надеть защитные латунные колпачки, чтобы избежать случайной порчи поверхности шатунных шеек.
При установке поршней в гильзы цилиндров следить за тем, чтобы надпись на поршне «перед» была направлена к переднему торцу блока цилиндров. Гайки болтов шатуна затянуть (момент 6,8 — 7,5 кгм) и законтрить.
После запрессовки шестерни на распределительный вал (рис. 8) проверить щупом осевой зазор между упорным фланцем и торцом шестерни распределительного вала. Зазор должен быть в пределах 0,08 — 0,2 мм.
При зацеплении шестерен газораспределения зуб шестерни коленчатого вала с меткой «О» должен войти во впадину зубьев шестерни распределительного вала, отмеченную риской. Шестерни заменять комплектно, так как их подбирают на заводе по боковому зазору и по шуму при работе. Боковой зазор в зацеплении должен быть в пределах 0,03—0,08 мм.
Чтобы не ошибиться при сборке и установке шестерен нужно учитывать, что метка на шестерне коленчатого вала находится на 12-том зубе, считая от зуба напротив прорези под шпонку против часовой стрелки (рисунок 11).
При установке на блок цилиндров крышку распределительных шестерен сцентрировать по переднему концу коленчатого вала при помощи конусной оправки для предохранения переднего сальника коленчатого вала от работы одной стороной.
Надеть на передний конец коленчатого вала конусную справку и прижать ею крышку распределительных шестерен к блоку цилиндров при помощи храповика, после этого затянуть гайки крепления крышки.
Уплотнительную прокладку трубки маслоприемника следует уложить в гнездо в блоке цилиндров, а не надевать на трубку.
Перед установкой на двигатель масляный насос заполняют маслом.
При сборке головки цилиндров стержни новых клапанов обмазывают смесью, состоящей из семи частей коллоидно-графитового препарата и трех частей авиационного масла.
Оси коромысел собирают таким образом, чтобы отверстия под шпильки крепления в оси и стойках были смещены в противоположную сторону от регулировочных болтов коромысел.
Гайки крепления впускного трубопровода затягивают с умеренным усилием, так как резиновые прокладки не могут ограничить затяжки до упора и при перетяжке гаек возможно раздавливание резиновых прокладок.
Привод прерывателя-распределителя необходимо устанавливать в такой последовательности.
Установить поршень 1-го цилиндра в положение верхней мертвой точки (в.м.т.) в такте сжатия.
Вставить привод прерывателя-распределителя в отверстие в блоке цилиндров так, чтобы прорезь в валике привода была направлена вдоль оси двигателя и смещена влево, считая по ходу автомобиля.
Закрепить корпус привода держателем и гайкой так, чтобы кронштейн с резьбовым отверстием для крепления прерывателя-распределителя был направлен назад, и повернут на угол 23˚ влево от продольной оси двигателя, как показано на рис. 10.
Перед установкой прерывателя-распределителя на двигатель следует проверять зазор в контактах прерывателя и, если необходимо, отрегулировать его. Зазор в контактах должен быть в пределах 0,З—0,4 мм.
Гайками октан-корректора повернуть корпус прерывателя-распределителя так, чтобы стрелка установилась на нулевое деление шкалы.
Повернуть ротор распределителя так, чтобы он был обращен в сторону клеммы первого цилиндра. Клемма первого цилиндра на крышке распределителя зажигания отмечена цифрой «1».
Надеть крышку распределителя с проводами и присоединить последние к свечам зажигания в порядке работы цилиндров двигателя (1-5-4-2-6-3-7-8). Порядок зажигания отлит на впускном трубопроводе двигателя.
2.5. ГАЗ. Эксплуатация, обслуживание и ремонт автомобилей ГАЗ-53А и ГАЗ-66. Сборка двигателя — «ВАЖНО ВСЕМ»
Для сборки двигателя, так же как и для его разборки, блок цилиндров двигателя в сборе с картером сцепления закрепляют на стенде (см. рис. 11 раздела «2.3.1. ГАЗ-53А и ГАЗ-66. Разборка двигателя»).
Все детали двигателя перед сборкой подбирают по размерам (табл. 4 см. раздела «2.5.1. ГАЗ-53А и ГАЗ-66. Размеры основных деталей, зазоры и натяги в сопряжениях двигателей»). тщательно промывают, продувают сжатым воздухом и протирают чистыми салфетками. Все резьбовые соединения (шпильки, пробки, штуцера и т. д.), если они вывёртывались при разборке или были заменены на новые, необходимо ставить на сурике или свинцовых белилах, разведенных натуральной олифой. Неразъёмные соединения (заглушки блока и головок цилиндров) ставят на нитролаке.
К постановке на ремонтируемый двигатель не допускаются:
- шплинты и шплинтовочная проволока, бывшие в употреблении;
- пружинные шайбы, потерявшие упругость;
- болты и шпильки с вытянувшейся резьбой;
- гайки и болты с изношенными гранями;
- детали, имеющие на резьбе более двух забоин или вмятин или сорванные нитки резьбы;
- поврежденные прокладки.
Собирают двигатель в порядке, обратном разборке.
Ниже приводятся отдельные рекомендации и дополнительные требования по сборке двигателя.
При замене гильз цилиндров перед установкой гильзу подбирают по гнезду в блоке цилиндров.
Гильзы подбирают при помощи точной металлической линейки и набора щупов следующим образом: гильза, установленная на своё место в блоке цилиндров без уплотнительных прокладок, должна утопать относительно привалочной поверхности блока цилиндров. Линейку устанавливают на привалочную поверхность, а щуп вводят в зазор между линейкой и торцом гильзы (рис. 23). Толщину прокладки выбирают таким образом, чтобы после установки гильзы с прокладкой было обеспечено возвышение её над поверхностью блока цилиндров в пределах 0,02 — 0,09 мм.
Рис. 23. Определение положения гильзы в блоке цилиндров
Уплотнительные прокладки выпускают различной толщины: 0,3; 0,2; 0,15 и 0,1 мм. В зависимости от зазора на гильзу цилиндра надевают ту или иную прокладку, иногда необходимую величину получают набором прокладок различной толщины.
После установки в блок цилиндров гильзы закрепляют втулками-зажимами (см. рис. 13 раздела «2.3.1. ГАЗ-53А и ГАЗ-66. Разборка двигателя» ).
В качестве заднего сальника на двигателях применяют асбестовый шнур, пропитанный маслянографитовой смесью. В гнёзда блока цилиндров и сальникодержателя укладывают шнур длиной 140 мм. При помощи приспособления шнур опрессовывают в своих гнездах лёгкими ударами молотка, как указано на рис. 24. Не снимая приспособления, подрезают концы шнура заподлицо с плоскостью разъёма сальникодержателя. Срез должен быть ровным, разлохмачивание концов и неровный срез не допускаются.
Рис. 24. Укладка заднего сальника коленчатого вала в сальникодержатель
При сборке коленчатого вала с маховиком и сцеплением соблюдают следующие требования.
Гайки крепления маховика затягивают, обеспечивая момент 7,6 — 8,3 кГм.
При сборке сцепления ведомый диск устанавливают демпфером к нажимному диску и центрируют по подшипнику коленчатого вала (в качестве оправки может быть использован ведущий вал коробки передач),
Метки <О>, выбитые на кожухе нажимного диска и маховика около одного из отверстий для болтов крепления кожуха, необходимо совместить.
Коленчатый вал в сборе с маховиком и сцеплением должны быть динамически сбалансированы. Допустимый дисбаланс— 70 Гсм. При балансировке снимают лишнюю массу с тяжелой стороны высверливанием металла маховика на расстоянии 6 мм от зубчатого венца сверлом диаметром 8 мм на глубину не более 10 мм.
Если дисбаланс собранного вала превышает 180 Гсм, вал разбирают и балансируют каждую деталь отдельно. Дисбаланс маховика не должен превышать 35 Гсм; дисбаланс иажнмного днска в сборе с кожухом — 36 Гсм; дисбаланс ведомого диска— 18 Гсм.
Крышки коренных подшипников устанавливают так, чтобы фиксирующие выступы вкладышей находились с одной стороны, а номера или метки, выбитые на крышках, соответствовали номерам постелей. При установке передней крышки необходимо следить, чтобы фиксирующий усик задней шайбы упорного подшипника вошёл в паз крышки и чтобы не образовывалось ступеньки между торцом крышки и торцом блока цилиндров.
Гайки крепления крышек коренных подшипников затянуть (момент 11—12 кГм). После затяжки и шплинтовки гаек крышек коренных подшипников коленчатый вал должен легко вращаться от небольших усилий.
Рис.25. Напрессовка шестерни коленчатого вала
После напрессовки шестерни коленчатого вала (рис. 25) при помощи съёмника и упорной втулки проверить осевой зазор коленчатого вала, для чего отжать коленчатый вал к заднему концу двигателя и при помощи щупа определить зазор между торцом задней шайбы упорного подшипника и торцом передней коренной шейки коленчатого вала (рис. 26). Зазор должен быть в пределах 0,075 — 0,175 мм.
Рис. 26. Проверка осевого зазора
При сборке деталей шатунно-поршневой группы необходимо соблюдать следующие требования.
- Поршневые пальцы подбирают к шатунам так, чтобы при комнатной температуре (+18°С) слегка смазанный палец плавно перемещался в отверстии шатуна под лёгким усилием большого пальца руки.
- Перед сборкой поршни нагревают в горячей воде до +70°С.
Запрессовка пальца в холодный поршень не допускается, так как это может привести к порче поверхностей отверстий бобышек поршня, а также к деформации самого поршня.
Рис. 27. Соединение шатуна с поршнем:
а — для установки в 1, 2, 3 и 4-й цилиндры; б — 5,6, 7 и 8-й цилиндры;
1-надпись на поршне; 2-номер на шатуне; 3-метка на крышке шатуна
Шатуны и поршни при сборке ориентируют следующим образом:
- для поршней первого, второго, третьего и четвертого цилиндров надпись на поршне <перед> и номер, выштампованный на стержне шатуна, должны быть направлены в противоположные стороны, а для поршней пятого, шестого, седьмого и восьмого цилидров — в одну сторону (рис. 27).
- Стопорные кольца поршневого пальца устанавливают в канавки бобышек поршня так, чтобы отгиб усика был направлен наружу.
- Поршневые кольца подбирают по гильзам, в которых они будут работать. Зазор, замеренный в стыке кольца, уложенного в гильзу, должен быть в пределах 0,3 — 0,5 мм для компрессионных и маслосъёмных колец, В верхнюю поршневую канавку устанавливают хромированное, а во вторую — луженое компрессионное кольцо выточкой на внутренней стороне к днищу.
Перед установкой в гильзы цилиндров стыки поршневых колец расположить под углом в 120° друг к другу, а на шатунные болты следует надеть защитные латунные колпачкн, чтобы избежать случайной порчи поверхности шатунных шеек.
При установке поршней в гильзы цилиндров следить за тем, чтобы надпись на поршне <перед> была направлена к переднему торцу блока цилиндров. Гайки болтов шатуна затянуть (момент 6,8 — 7,5 кГм) и законтрить.
После запрессовки шестерни на распределительный вал (рис. 28) проверить щупом осевой зазор между упорным фланцем и торцом шестерни распределительного вала. Зазор должен быть в пределах 0,08 — 0,2 мм.
Рис. 28. Напрессовка шестерни на распределительный вал
При зацеплении шестерен газораспределения зуб шестерни коленчатого вала с меткой <О> должен войтb во впадину зубьев шестерни распределительного вала, отмеченную риской. Шестерни заменять комплектно, так как их подбирают на заводе по боковому зазору и по шуму при работе. Боковой зазор в зацеплении должен быть в пределах 0,03—0,08 мм.
При установке на блок цилиндров крышку распределительных шестерен сцентрировать по переднему концу коленчатого вала при помощи конусной оправки для предохранения переднего сальника коленчатого вала от работы одной стороной.
Надеть на передний конец коленчатого вала конусную оправку и прижать ею крышку распределительных шестерен к блоку цилиндров при помощи храповика, после этого затянуть гайки крепления крышки.
Уплотнительную прокладку трубки маслоприёмника следует уложить в гнездо в блоке цилиндров, а не надевать на трубку.
Перед установкой на двигатель масляный насос заполняют маслом.
При сборке головки цилиндров стержни новых клапанов обмазывают смесью, состоящей из семи частей коллоидно-графитового препарата и трех частей авиационного масла.
Оси коромысел собирают таким образом, чтобы отверстия под шпильки крепления в оси и стойках были смещены в противоположную сторону от регулировочных болтов коромысел.
Гайки крепления впускного трубопровода затягивают с умеренным усилием, так как резиновые прокладки не могут ограничить затяжки до упора и при перетяжке гаек возможно раздавливание резиновых прокладок.
Привод прерывателя-распределителя необходимо устанавливать в такой последовательности.
- Установить поршень 1-го цилиндра в положение верхней мертвой точки (в.м.т.) в такте сжатия.
- Вставить привод прерывателя-распределителя в отверстие в блоке цилиндров так, чтобы прорезь в валике привода была направлена вдоль оси двигателя и смещена влево, считая по ходу автомобиля.
- Закрепить корпус привода держателем и гайкой так, чтобы кронштейн с резьбовым отверстием для крепления прерывателя-распределителя был направлен назад и повернут на угол 23° влево от продольной оси двигателя, как показано на рис. 29.
- Перед установкой прерывателя-распределителя на двигатель следует проверить зазор в контактах прерывателя и, если необходимо, отрегулировать его. Зазор в контактах должен быть в пределах 0,3 — 0,4 мм.
- Гайками октан-корректора повернуть корпус прерывателя-распределителя так, чтобы стрелка установилась на нулевое деление шкалы.
- Повернуть ротор распределителя так, чтобы он был обращен в сторону клеммы первого цилиндра. Клемма первого цилиндра на крышке распределителя зажигания отмечена цифрой «1».
Надеть крышку распределителя с проводами и присоединить последние к свечам зажигания в порядке работы цилиндров двигателя (1 — 5 — 4 — 2 — 6 — 3 — 7 — 8). Порядок зажигания отлит на впускном трубопроводе двигателя.
Рис. 29. Установка привода прерывателя-распределителя
технические характеристики. Сборка двигателя ГАЗ-53, установка, ремонт :: SYL.ru
В СССР самой распространенной моделью грузовых автомобилей стал ГАЗ-53 и его модификации. За более чем тридцать лет, с момента выпуска первой машины, с конвейеров сошло свыше 4 миллионов экземпляров.
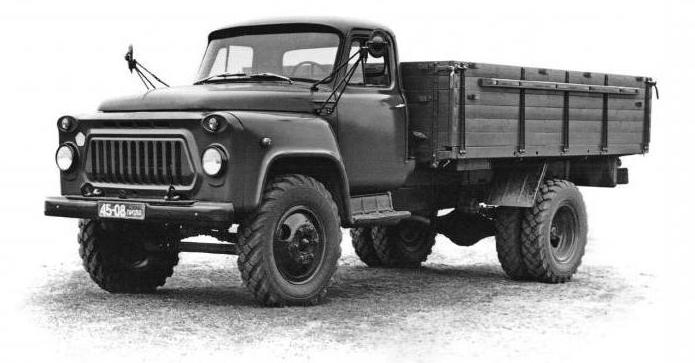
Выпускался автомобиль с 1961 по 1992 годы на мощностях Горьковского автозавода.
Двигатель ГАЗ-53
На автомобили ГАЗ-53 устанавливались две основные модели силовых агрегатов: шестицилиндровый ГАЗ-11 и восьмицилиндровый ЗМЗ-53. Второй мотор имел несколько различных модификаций, однако особой разницы в их конструкции нет.
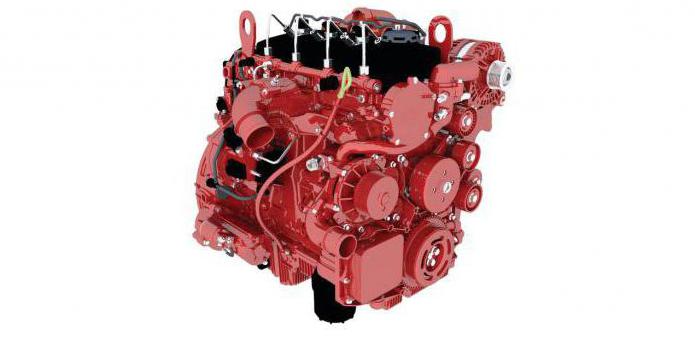
Несмотря на высокое качество сборки и надежность, двигатель ГАЗ-53 со временем требует проведения ремонтных работ.
Обслуживание мотора
Двигатели внутреннего сгорания, относящиеся к семейству ЗМЗ-53, отличаются неплохим рабочим ресурсом и надежностью, однако, как и любые другие силовые агрегаты, требуют проведения регулярного технического обслуживания. К числу подобных профилактических мер можно отнести:
- Смену смазочного материала. Масло в двигатель ГАЗ-53 заливается как минеральное, так и синтетика с полусинтетикой. Менять его приходится каждые 5-6 тысяч километров пробега для первого типа, для второго – каждые 10-12 тысяч. Впрочем, синтетические масла не совсем подходят для такого двигателя, и использовать их нежелательно.
- Регулярная подтяжка креплений впускного коллектора и головок блока цилиндров. В других ситуациях проверяется затяжка раз в 30 тысяч километров, однако можно и чаще. У двигателя слабым местом является именно впускной коллектор, который зачастую идет «винтом». Подтягиваются его гайки очень просто и находятся в свободном доступе.
- Проверка уровня охлаждающей жидкости. Проводить ее желательно перед каждым выездом на автомобиле. Ремонт двигателя ГАЗ-53 зачастую становится последствием недостаточного уровня жидкости в системе охлаждения.
- Проверка клапанов. Их регулировку проводят только после смены прокладок ГБЦ либо если двигатель ГАЗ-53 подвергался серьезному ремонту. В остальных случаях корректировка их работы происходит только если они начинают стучать. Сами по себе клапаны, как правило, из строя не выходят, так что в большинстве случаев их слишком сильно пережимают мастера во время работы. Как показывает практика, лучше, если они будут немного стучать.
- Проверка уровня масла. Проводится процедура ежедневно. При нехватке масла его доливают до необходимого уровня.
- Ремонт двигателя ГАЗ-53 может заключаться в заделке протечек масла. В большинстве случаев смазка протекает через задний коренной подшипник, поэтому его осмотр проводят только на смотровой яме.
Чтобы двигатель ГАЗ-53 работал как можно больше без неисправностей, необходимо регулярно проводить его диагностику, вовремя устранять неполадки и заливать только качественное моторное масло.
Двигатель ГАЗ-53: технические характеристики
Транспортные средства данной марки комплектуются несколькими модификациями силовых агрегатов. Начиная с 1966 года, на автомобили ГАЗ производилась установка двигателя ГАЗ-53. Модель комплектовалась карбюратором К-126Б и имела верхнее расположение клапанов. Нескольким позднее характеристика двигателя ГАЗ-53 изменилась, поскольку карбюратор был заменен на К-135.
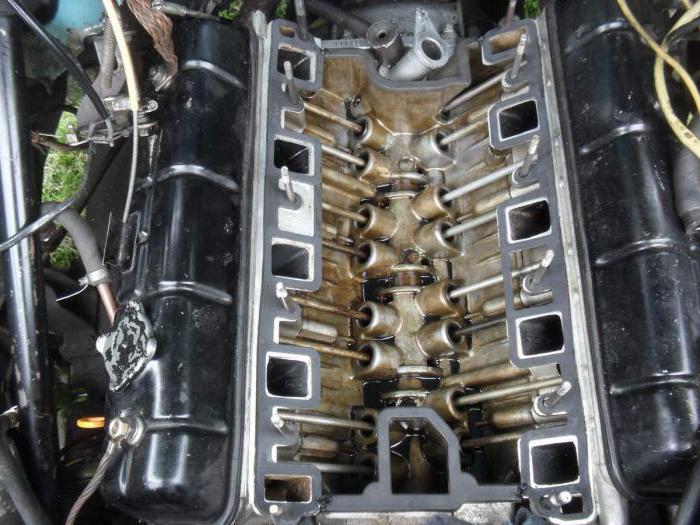
У этого мотора небольшой ход поршня и объем цилиндров. Многие придерживаются мнения, что детали других ДВС из одной линейки можно установить на двигатель ГАЗ-53. Технические характеристики этих моторов несколько разные, поэтому их элементы не являются взаимозаменяемыми. Отличаются не только блоки цилиндров, но и ГБЦ, поршневая группа и коленчатый вал.
Диагностика двигателя
Регулярная проверка необходима для блока цилиндров. Если его крепления ослабевают, подтягивают гайки. Прежде чем проводить такие работы, из системы сливается вся охлаждающая жидкость и ослабевается крепление впускной трубы — это позволяет не допускать воздействия подтяжки одной головки цилиндра на остальные.
После проведения таких процедур динамометрическим ключом закручиваются гайки. Такую работу производитель рекомендует осуществлять первые три технических обслуживания, затем ее частоту можно сократить до каждого второго.
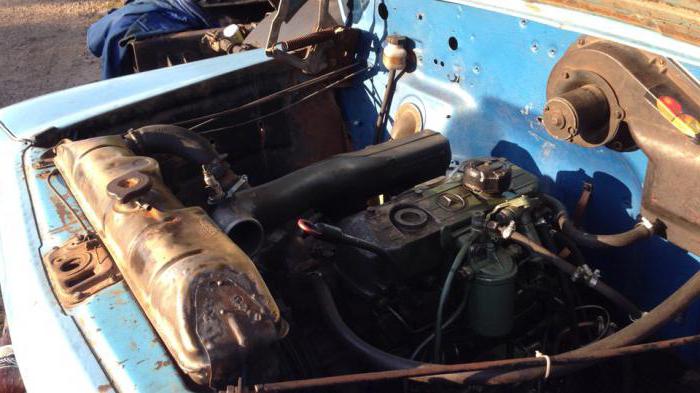
Двигатель ГАЗ-53 не требует проведения ремонта при условии использования смазочных материалов и топлива высокого качества. В таком случае образующийся на поршнях и внутри камеры сгорания нагар будет небольшим и не станет оказывать никакого влияния на работу мотора.
Несоблюдение банальных правил может привести к детонации, увеличению расхода и понижению мощности.
Удаление нагара
Двигатель ГАЗ-53 очень просто избавляется от нагара. Для этого необходимо провести чистку стенок камеры сгорания и днища поршней. Нагар содержит большое количество вредных веществ, поэтому при проведении такой процедуры желательно защитить дыхательные пути. С этой целью его нередко промазывают керосином.
Смена деталей коленчатого вала
С целью повышения потенциала двигателя желательно регулярно производить замену вкладышей коленчатого вала и поршневых колец.
Основной причиной обновления вкладышей является резкое снижение давления масла. Если возникает необходимость, замене подлежат и шатунные вкладыши.
Замена поршневых колец
Главным признаком того, что пришла пора менять поршневые кольца, становится увеличение расхода смазочного материала. В норме он составляет 400 г на 100 километров пробега. В комплект поршневых колец входят стальные диски и компрессионное кольцо из чугуна.
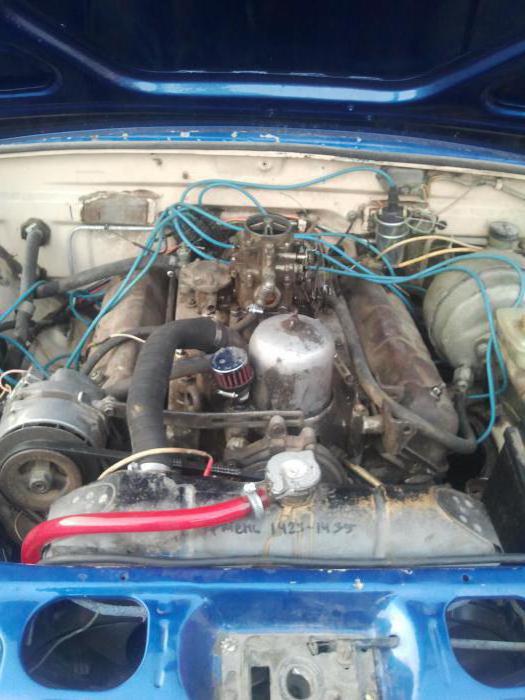
С гильз цилиндров во время замены удаляют неизношенный участок пояска, а ГБЦ очищаются от нагара.
Газораспределительный механизм также требует регулярной диагностики. Зазоры клапанов проверяются только при работающем вхолостую двигателе и опущенном до упора толкателе.
Возможные неисправности ДВС ГАЗ-53
У силового агрегата встречаются поломки и неисправности, характерные для любого другого мотора. Для их устранения производится полная разборка и сборка двигателя ГАЗ-53. Причины появления поломок могут быть различными:
- Появление стука латунных вкладышей. Является самой серьезной неисправностью. Приводит к ней низкий уровень масла, износ всех деталей либо сниженное или полностью отсутствующее давление в системе.
- Повышенный расход смазочного материала. Масло может либо протекать через сальники и соединения, либо через поршневые кольца. Также причиной этого может быть забивка сапуна.
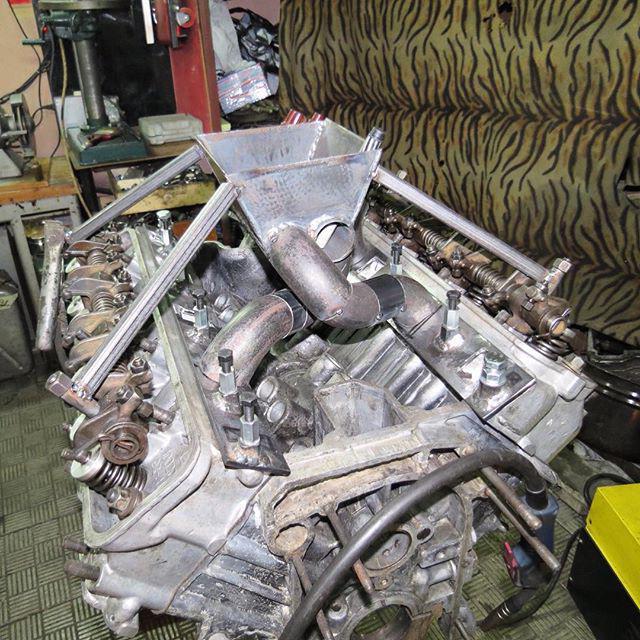
- Стуки втулок или поршней шатуна. Для поршней характерно перегорание днища либо выход из строя перегородок между кольцами. Основная причина этого — перегрев двигателя.
- Прогорание выпускных клапанов. Сами по себе они не прогорают, но зачастую можно столкнуться с износом направляющих втулок. Причин этого может быть несколько: попадание моторного масла, низкое качество топлива или отсутствие в клапанах зазора.
- Прогорание прокладок блока цилиндров. Причина — перегрев двигателя, который может привести к искривлению поверхности головок.
Капитальный ремонт двигателя
Мотор ГАЗ-53 при должном уходе крайне редко нуждается в капитальном ремонте, но если это все же случается, то причинами могут быть следующие неисправности:
- Увеличение расхода смазочного материала, причем с заменой колец проблема осталась актуальной.
- Низкое давление в смазочной системе и появление стуков в двигателе.
- Износ всего силового агрегата с исчерпыванием его рабочего ресурса.
- Заклинивание мотора из-за коленчатого вала.
Ремонт двигателя может производиться самостоятельно — производителем выпускается полное руководство по эксплуатации, в котором все действия по смене деталей и возможные неисправности и методы их устранения подробно описаны.
Несмотря ни на что, двигатели, устанавливаемые на ГАЗ-53, отличаются неплохой выносливостью. Учитывая различные «доработки» ДВС и масла, которые порой в него заливают, остается только удивляться его работоспособности. Нередко такой движок может спокойно функционировать годами даже при условии наличия непонятных стуков.
Двигатель ГАЗ-53: Трещина в блоке цилиндров
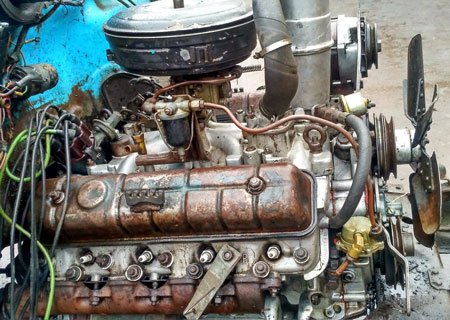
1. Утечка масла из двигателя и попытка ее устранить
2. Повторный разбор двигателя вместе с мотористом
3. Трещина горизонтального масляного канала блока цилиндров
4. Сломанная шпилька блока цилиндров
Двигатель ГАЗ-53 для своего времени был довольно надежен и бывало выхаживал до 200 тыс. км, уступая разве что мотору ЗИЛ-130. Однако, боялся он перегрева и обезличенного капитального ремонта.
Поэтому, многие водители предпочитали делать капиталку в своем гараже и считали это более надежным, чем ремонт в условиях авторемзавода.
1. Утечка масла из двигателя и попытка ее устранить
История двигателя, который стоял на моей машине, мне не известна, но точно уверен, что это было уникальное творение автопрома. Мотор постоянно барахлил и доставлял мне множество неприятностей. Одной из них, была течь масла через уплотнение заднего коренного подшипника.
Сначала, потери масла были не большими, но постепенно, они выросли до 4-6 литров в день. С таким расходом масла, наша организация не могла мириться и поэтому, шеф выделил мне день на поиск и устранение неисправности. Для этого, я нашел фирменную набивку с несколькими медными жилками.
Перед ремонтом, я проверил осевой люфт коленчатого вала и он оказался минимальным, что и следовало ожидать, ведь давление масла было нормальным. Работа по сливу масла с двигателя и снятию поддона, много времени не заняла.
Легко открутил маслозаборник и снял заднюю коренную крышку, а также крышку держателя набивки. Сама набивка имела вполне себе приличный вид. Далее, открутил еще один коренной подшипник и ослабил остальные.
Дело в том, что крышки коренных подшипников на моторе ГАЗ-53 чугунные. Сделано это для того, чтобы облегчить заводку двигателя в холодное время года.
Достигается это тем, что коэффициенты линейного расширения чугуна и стали приблизительно равны, поэтому в холодное время года, коленчатый вал двигателя не испытывает такого сильного сжатия, как в случае с крышками коренных подшипников выполненными из алюминия.
Открутив три первых крышки коренных подшипников, я смог оттянуть вал вниз с тем расчетом, чтобы вытащить старую набивку и с помощью проволоки завести новую. Когда новая набивка была в пазу блока цилиндров, установил предпоследнюю крышку и затянул все остальные. Лишние концы набивки отрезал, оставив запас на сжатие.
Далее, вставил набивку в съемную нижнюю крышку и так же подрезал ее, оставив небольшие концы. Крышку, которая держит набивку, тщательно протянул по месту, заменив при этом маслоуплотнительные флажки.
Затем, проверил еще на раз затяжку коренных крышек, установил маслоприемник и закрыл поддон двигателя. С чувством хорошо выполненной работы, залил масло в систему.
Завел мотор с хорошим настроением и каково же было мое удивление, когда заглянув под двигатель, я увидел еле видную струйку масла. Настроение сразу же испортилось и досаде моей не было предела. Шеф же вместе с гаражным большинством решили, что для такой филигранной работы, нужен специалист моторист.
Надо отдать коллективу должное, никаких ухмылок в мою сторону не было. Я же поехал работать дальше, доливая каждый день минимум по пол ведра масла. Шеф вздыхал, но талоны на масло где то находил.
2. Повторный разбор двигателя вместе с мотористом
Сколько с таким расходом я проездил, точно сказать не могу, но в какой то момент шеф объявил, что после обеда нужно снять поддон двигателя, т.к. приедет моторист, который будет ремонтировать двигатель, а мне ему нужно будет помочь.
Быстренько все разобрал и дождался моториста, который произвел операцию по замене сальниковой набивки. Пока я ставил поддон и заливал масло, моторист уж успел получить деньги за сделанную работу.
Двигатель был заведен и шеф, вместе со специалистом, подошли посмотреть. Заглянули под машину и обнаружили, что масло все еще бежит.
Увидев такое дело, моторист молча одел халат, взял переноску и опять полез под двигатель. Произведя осмотр, он матюкнулся и заявил, что масло действительно течет с коренного. Меня такое заявление не обрадовало и оптимизма не внушило.
Шеф с мотористом ушли, а через какое то время, мне была дана команда снять завтра с утра двигатель и перевезти его в соседнюю организацию, чтобы уже там произвести ремонт как надо.
На следующий день, я занялся привычной для меня работой по откручиванию гаек и уже в обед вместе с двигателем был в соседней организации. Там открутил с мотора поддон, а также снял сцепление и маховик.
Вместе с мотористом, подсвечивая себе переноской, мы тщательно осмотрели заднюю часть блока цилиндров на предмет возможной трещины. Однако, никаких дефектов нам выявить не удалось. После чего, моторист с особой тщательностью во второй раз выполнил работу по замене сальниковой набивки, флажков уплотнения крышки и установке поддона.
На следующий день к обеду, я уже устанавливал двигатель на автомобиль. Не знаю по какой причине, но меня не покидало чувство какой то нереальности событий, ведь операцию по замене набивки на этом моторе проделывали уже трижды.
Работа шла не так быстро и я не успел до вечера поставить коробку. Однако, решил не ждать полной сборки, а попробовать завести двигатель так. Шеф с мотористом были неподалеку и наблюдали за процессом.
Мотор завелся сразу и давление масла поднялось, после чего под двигателем образовалась уже всем знакомая масляная струйка. Моторист громко чертыхнулся и полез злой под мотор, но довольно быстро молча вылез обратно.
Заглянул под двигатель и я, однако картина была старая. Создавалась полная уверенность, что масло течет с шейки коренного подшипника.
Подумав немного, моторист объявил, что такого у него никогда не было и лучше бы мы заменили мотор. Проблема же была в том, что другой двигатель нам взять было просто негде (по крайней мере так заявил шеф). Еще парочка человек залазило под машину, но все сходились во мнении, что течет масло с коренного.
3. Трещина горизонтального масляного канала блока цилиндров
Потихоньку, я стал переодеваться и собираться домой. Тут то у меня и возник вопрос, а будет ли работать двигатель ГАЗ-53 без маховика? На резонный вопрос коллег, а зачем это собственно нужно проверять, я пояснил, что без маховика можно будет точно увидеть, откуда течет масло.
Посовещавшись, коллеги озвучили общую позицию, что двигатель работать не будет, т.к. поршневая группа без маховика не сможет выйти из мертвых точек. Однако, я все же решил демонтировать сцепление и маховик, после чего попробовать завести двигатель рукояткой.
Демонтаж много времени не занял и я, взяв рукоятку и включив зажигание, приступил к заводке. Прокрутил вал несколько раз и неожиданно двигатель завелся. Самое интересное, он работал очень ровно и практически был неподвижен.
Взял переноску и полез под машину со стороны КПП, где очень отчетливо увидел место с которого мелкими каплями из трещины шло масло. Оно просачивалось с горизонтального масляного канала и поэтому при заглушенном двигателе, эту трещину увидеть было невозможно.
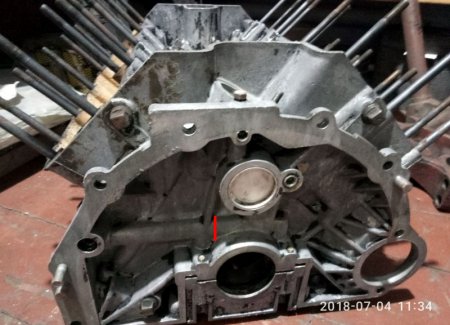
Блок двигателя ГАЗ-53 с красной полоской на месте трещины
Спустя 3 дня, шеф нашел блок цилиндров под замену, а мне опять пришлось снять и отвезти двигатель в уже знакомую ремонтную организацию. При разборе мотора, мы обнаружили еще и не совпадение шестерен распредвала на один зуб. Заменили блок и вновь собрали двигатель. После чего, я вернулся к своей машине и установил мотор на место.4. Сломанная шпилька блока цилиндров
На этом, проблемы с течью масла из двигателя закончились и я относительно спокойно проездил на машине около 1 тыс. км. Однако, пришло время протянуть головки блока и как назло в процессе лопнула шпилька (хорошо, что не крайняя) по резьбе в недрах блока.
Тогда, я взял деревянную сухую пробку длиной 10 см и забил ее на место шпильки. Сделал это для того, чтобы даже случайно по шпильке или прокладке, вода не попадала по отверстию шпильки в головке в поддон. Так и ездил около года, пока не получил квартиру, ради которой работал.
Свечи двигатель по прежнему забрасывал, но причина этого мне так и осталась неизвестна. После того как я уволился, машина проходила еще около полугода, а потом ее списали. Думаю, это никого особо не расстроило.
Больше мне таких проблемных двигателей и машин в жизни не попадалось. Однако, зла за это я не держу, ведь автомобиль дал мне опыт борьбы с трудными поломками и позволил заработать на квартиру.
Автор: Эдуард Залуцкий
Сборка двигателя автомобиля ГАЗ-66, ГАЗ-53
Страница 1 из 2
Для сборки двигателя, так же как и для его разборки, блок цилиндров двигателя в сборе с картером сцепления закрепляют на стенде (см. рис. 1).
Все детали двигателя перед сборкой подбирают по размерам, тщательно промывают, продувают сжатым воздухом и протирают чистыми салфетками
Все резьбовые соединения (шпильки, пробки, штуцера и т. д.), если они вывертывались при разборке или были заменены, необходимо ставить на сурике или свинцовых белилах, разведенных натуральной олифой.
Неразъемные соединения (заглушки блока и головок цилиндров) ставят на нитролаке.
К постановке на ремонтируемый двигатель не допускаются:
— шплинты и шплинтовочная проволока, бывшие в употреблении;
— пружинные шайбы, потерявшие упругость;
— болты и шпильки с вытянувшейся резьбой;
— гайки и болты с изношенными гранями;
— детали, имеющие на резьбе более двух забоин или вмятин или сорванные нитки резьбы;
— поврежденные прокладки.
Собирают двигатель в порядке, обратном разборке.
Подготовку деталей для сборки двигателя можно посмотреть в статье — Подготовка узлов и деталей для сборки двигателя ЗМЗ-53
Ниже приводятся отдельные рекомендации и дополнительные требования по сборке двигателя.
При замене гильз цилиндров перед установкой гильзу подбирают по гнезду в блоке цилиндров.
Гильзы подбирают при помощи точной металлической линейки и набора щупов следующим образом:
— гильза, установленная на свое место в блоке цилиндров без уплотнительных прокладок, должна утопать относительно привалочной поверхности блока цилиндров.
Линейку устанавливают на привалочную поверхность, а щуп вводят в зазор между линейкой и торцом гильзы (рис. 2).
Толщину прокладки выбирают таким образом, чтобы после установки гильзы с прокладкой было обеспечено возвышение ее над поверхностью блока цилиндров в пределах 0,02—0,09 мм.
Уплотнительные прокладки выпускают различной толщины:
0,3; 0,2; 0,15 и 0,1 мм. В зависимости от зазора на гильзу цилиндра надевают ту или иную прокладку, иногда необходимую величину получают набором прокладок различной толщины.
После установки в блок цилиндров гильзы закрепляют втулками-зажимами (см. рис. 3).
В качестве заднего сальника на двигателях применяют асбестовый шнур, пропитанный масляно-графитовой смесью.
В гнезда блока цилиндров и сальникодержателя укладывают шнур длиной 140 мм.
При помощи приспособления шнур опрессовывают в своих гнездах легкими ударами молотка, как указано на рис. 4.
Не снимая приспособления, подрезают концы шнура заподлицо с плоскостью разъема сальникодержателя.
Срез должен быть ровным, разлохмачивание концов и неровный срез не допускаются.
При сборке коленчатого вала с маховиком и сцеплением соблюдают следующие требования.
Гайки крепления маховика затягивают, обеспечивая момент 7,6—8,3 кГм.
При сборке сцепления ведомый диск устанавливают демпфером к нажимному диску и центрируют по подшипнику коленчатого вала (в качестве оправки может быть использован ведущий вал коробки передач).
Метки «О», выбитые на кожухе нажимного диска и маховика около одного из отверстий для болтов крепления кожуха, необходимо совместить.
Коленчатый вал в сборе с маховиком и сцеплением должны быть динамически сбалансированы. Допустимый дисбаланс 70 Гсм.
При балансировке снимают лишнюю массу с тяжелой стороны высверливанием металла маховика на расстоянии 6 мм от зубчатого венца сверлом диаметром 8 мм на глубину не более 10 мм.
Если дисбаланс собранного вала превышает 180 Гсм, вал разбирают и балансируют каждую деталь отдельно.
Дисбаланс маховика не должен превышать 35 Гсм;
дисбаланс нажимного диска в сборе с кожухом — 36 Гсм;
Дисбаланс ведомого диска— 18 Гсм.
По сборке коленчатого вала смотрим статью — Сборка коленчатого вала с маховиком и сцеплением и установка его в блок цилиндров
Крышки коренных подшипников устанавливают так, чтобы фиксирующие выступы вкладышей находились с одной стороны, а номера или метки, выбитые на крышках, соответствовали номерам постелей.
При установке передней крышки необходимо следить, чтобы фиксирующий усик задней шайбы упорного подшипника вошел в паз крышки, и чтобы не образовывалось ступеньки между торцом крышки и торцом блока цилиндров.
Гайки крепления крышек коренных подшипников затянуть (момент 11—12 кГм).
После затяжки и шплинтовки гаек крышек коренных подшипников коленчатый вал должен легко вращаться от небольших усилий.
После напрессовки шестерни коленчатого вала (рис. 5) при помощи съемника и упорной втулки проверить осевой зазор коленчатого вала, для чего отжать коленчатый вал к заднему концу двигателя и при помощи щупа определить зазор между торцом задней шайбы упорного подшипника и торцом передней коренной шейки коленчатого вала (рис. 6).
Зазор должен быть в пределах 0,075 — 0,175 мм.