Газотурбинный двигатель подробно — Энциклопедия журнала «За рулем»
ИДЕЯ применить в автомобилях газотурбинные двигатели возникла давно. Но лишь за последние несколько лет их конструкция достигла той степени совершенства, которая дает им право на существование.
Высокий уровень развития теории лопаточных двигателей, металлургии и техники производства обеспечивает теперь реальную
возможность создания надежных газотурбинных двигателей, способных с успехом заменить на автомобиле поршневые двигатели внутреннего сгорания.
Что представляет собой газотурбинный двигатель?
На рис. показана принципиальная схема такого двигателя. Ротационный компрессор, находящийся на одном валу с газовой турбиной, засасывает воздух из атмосферы, сжимает его и нагнетает в камеру сгорания.
Топливный насос, также приводимый в движение от вала турбины, нагнетает топливо в форсунку, установленную в камере сгорания. Газообразные продукты сгорания поступают через направляющий аппарат на рабочие лопатки колеса газовой турбины и заставляют его вращаться в одном, определенном направлении. Газы, отработавшие в турбине, выпускаются в атмосферу через патрубок. Вал газовой турбины вращается в подшипниках.
Характеризуя газовую турбину, прежде всего следует отметить, что она, как и паровая турбина, может развивать большие обороты. Это дает возможность получать значительную мощность от гораздо меньших по размерам (по сравнению с поршневыми) и почти в 10 раз более легких по весу двигателей.
Вращательное движение вала является по существу единственным видом движения в газовой турбине, в то время как в двигателе внутреннего сгорания, помимо вращательного движения коленчатого вала, имеет место возвратно-поступательное движение поршня, а также сложное движение шатуна. Газотурбинные двигатели не требуют специальных устройств для охлаждения. Отсутствие трущихся деталей при минимальном количестве подшипников обеспечивают длительную работоспособность и высокую надежность газотурбинного двигателя.
Основная причина, которая сдерживает развитие автомобильных газотурбинных двигателей, заключается в необходимости искусственно ограничивать температуру газов, поступающих на лопатки турбины. Это снижает коэффициент полезного действия двигателя и приводит к повышенному удельному расходу топлива (на 1 л. с ). Температуру газа приходится ограничивать для газотурбинных двигателей пассажирских и грузовых автомобилей в пределах 600—700°С, а в авиационных турбинах до 800—900°С потому, что еще очень дороги высокожаропрочные сплавы.
Принципиальная схема двухвального газотурбинного двигателя с теплообменником
Большинство существующих автомобильных газотурбинных двигателей построено по так называемой двухвальной схеме с теплообменниками. Здесь для привода компрессора 1 служит специальная турбина 8, а для привода колес автомобиля — тяговая турбина 7. Валы турбин не соединены между собой. Газы из камеры сгорания 2 вначале поступают на лопатки турбины привода компрессора, а затем на лопатки тяговой турбины. Воздух, нагнетаемый компрессором, прежде чем поступить в камеры сгорания, подогревается в теплообменниках 3 за счет тепла, отдаваемого отработавшими газами. Применение двухвальной схемы создает выгодную тяговую характеристику газотурбинных двигателей, позволяющую сократить число ступеней в обычной коробке передач автомобиля и улучшить его динамические качества.
Ввиду того, что вал тяговой турбины механически не связан с валом турбины компрессора, число его оборотов может изменяться в зависимости от нагрузки, не оказывая существенного влияния на число оборотов вала компрессора. Вследствие этого характеристика крутящего момента газотурбинного двигателя имеет вид, представленный на рис., где для сопоставления нанесена также и характеристика поршневого автомобильного двигателя (пунктиром).
Характеристика одновального газотурбинного двигателя отличается от показанной на рис. и, как правило, уступает, с точки зрения требований динамики автомобиля, характеристике поршневого двигателя (при равной мощности).
Большую перспективу имеет газотурбинный двигатель. В этом двигателе газ для турбины вырабатывается в так называемом свободно-поршневом генераторе, представляющем собой двухтактный дизель и поршневой компрессор, объединенные в общем блоке. Энергия от поршней дизеля передается непосредственно поршням компрессора.
Ввиду того, что движение поршневых групп осуществляется исключительно под действием давления газов и режим движения зависит только от протекания термодинамических процессов в дизельном и компрессорных цилиндрах, такой агрегат и называется свободно-поршневым. В его средней части расположен открытый с двух сторон цилиндр 4, имеющий прямоточную щелевую продувку, в котором протекает двухтактный рабочий процесс с воспламенением от сжатия. В цилиндре оппозитно перемещаются два поршня, один из которых 9 во время рабочего хода открывает, а во время возвратного хода закрывает выхлопные окна, прорезанные в стенках цилиндра. Другой поршень 3 также открывает и закрывает продувочные окна. Поршни связаны между собой легким реечным или рычажным синхронизирующим механизмом, не показанным на схеме. Когда они сближаются, воздух, заключенный между ними, сжимается; к моменту достижения мертвой точки температура сжимаемого воздуха становится достаточной для воспламенения топлива, которое впрыскивается через форсунку 5. В результате сгорания топлива образуются газы, обладающие высокой температурой и давлением; они заставляют поршни разойтись в стороны, при этом поршень 9 открывает выхлопные окна, через которые газы устремляются в газосборник 7. Затем открываются продувочные окна, через которые в цилиндр 4 поступает сжатый воздух, вытесняет из цилиндра выхлопные газы, смешивается с ними и также поступает в газосборник. За то время, пока продувочные окна остаются открытыми, сжатый воздух успевает очистить цилиндр от выхлопных газов и заполнить его, подготовив таким образом двигатель к следующему рабочему ходу.
Двигатель бензиновый 0,22—0,26
Газовая турбина с камерами сгорания постоянного объема без теплообменника 0,12-0,18
Газовая турбина с камерами сгорания постоянного объема с теплообменником 0,15—0,25
Газовая турбина со свободно-поршневым генератором газа 0,25—0,35
Таким образом, КПД лучших образцов турбин не уступает КПД дизелей. Не случайно поэтому количество экспериментальных газотурбинных автомобилей различного типа возрастает с каждым годом. Все новые фирмы в различных странах объявляют о своих работах в этой области.
Схема реального газотурбинного двигателяЭтот двухкамерный двигатель, без теплообменника, имеет эффективную мощность 370 л. с. Топливом для него служит керосин. Скорость вращения вала компрессора достигает 26 000 об/мин, а скорость вращения вала тяговой турбины от 0 до 13 000 об/мин. Температура газов, поступающих на лопатки турбины, равна 815° Ц, давление воздуха на выходе из компрессора — 3,5 ат. Общий вес силовой установки, предназначенной для гоночного автомобиля, составляет 351 кг, причем газопроизводящая часть весит 154 кг, а тяговая часть с коробкой передач и передачей на ведущие колеса — 197 кг.
Особенности конструкции газотурбинных двигателей (В. М. Корнеев)
Общие сведения о ГТД
Краткая история создания отечественных авиационных ГТД
Первые проекты воздушно-реактивных двигателей (ВРД) были разработаны в России еще во второй половине XIX века. Инженером И. И. Третеским в 1849 г. предложено использовать для передвижения аэростата силу реакции, возникающую при истечении сжатого воздуха. Несколько позже, в 1866 г., Н. М. Соковнин разработал проект компрессорного ВРД, предназначенного для дирижабля. В 1867 г. Н. Телешов изобрел двигатель «Теплородный духомет», содержащий все основные части современного ВРД.
Первый работающий турбинный двигатель создан в России в конце XIX века. В период с 1886 по 1892 гг. инженер П. Д. Кузьминский разработал, построил и провел испытания в Петербурге газопаротурбинного двигателя, в котором процесс подвода тепла к рабочему телу протекал при постоянном давлении. Двигатель П. Д. Кузьминского имел многоступенчатую радиальную турбину с концентрически расположенными сопловыми и рабочими лопатками. В 1890 г. П. Д. Кузьминский впервые предложил использовать газовую турбину в авиации.
Русским инженером В. В. Караводиным в 1906 г. запатентован «Аппарат для получения пульсирующей струи газа значительной скорости вследствие периодических взрывов горючей смеси». Во время второй мировой войны в Германии были построены пульсирующие ВРД, устанавливаемые на самолетах-снарядах (ФАУ-1) и работающие по предложенной В. В. Караводиным схеме.
В 1909 г. Н. В. Герасимов получил патент на двигатель, имеющий все основные элементы современного турбореактивного двигателя (ТРД). Схему турбовинтового двигателя (ТВД), в котором воздушный винт имел привод от газовой турбины, впервые разработал М. Н. Никольский в 1913 г. Модель этого двигателя была построена и испытана. Его предполагали использовать для самолета «Илья Муромец».
В 1949 г. создан ТРД с центробежным компрессором ВК-1 конструкции В. Я. Климова, имеющий наибольшую в мире тягу (27 кН) при минимальном удельном расходе топлива (0,104 кг/Н-ч) и удельном весе, равном 0,32. Этот двигатель был установлен на фронтовых истребителях и бомбардировщиках взамен РД-45, а в начале 50-х годов использован на скоростном почтово-грузовом гражданском самолете Ил-20. Последующий вариант этого двигателя с форсажной камерой ВК-1Ф, созданный в 1951 г., развивал тягу на форсажном режиме 33 кН и был установлен на фронтовом истребителе МИГ-17.
Первый отечественный ТРД с осевым компрессором ТР-1 конструкции А. М. Люлька прошел государственные испытания в 1947 г. Двигатель РД-9Б с форсажной камерой, созданный в 1952 г. под руководством С. К. Туманского, убедительно доказал преимущества ТРД с осевым компрессором перед ТРД с центробежным компрессором. Он обеспечил возможность создания первого в СССР серийного сверхзвукового истребителя МИГ-19 (1954 г.) с максимальной скоростью полета 1450 км/ч. Двухвальный ТРДФ с осевым компрессором Р11Ф-300 конструкции С. К. Туманского, на котором достигнута весьма высокая степень форсирования тяги, был применен на сверхзвуковых истребителях МИГ-21 (1958 г.), принятых на вооружение не только в СССР, но и в ряде других стран.
Параллельно с разработкой двигателей для сверхзвуковых истребителей советские конструкторы принимали энергичные меры по созданию новых ГТД с большой тягой и низким удельным расходом топлива для дальних бомбардировщиков и самолетов гражданской авиации. Конструкторским коллективом под руководством А. А. Микулина еще в 1946—1947 гг. создано несколько опытных двигателей большой тяги (ТКРД с тягой 37 кН, затем ТРД с тягой 47 кН), а в 1951 г. построен серийный турбореактивный двигатель АМ-3, имеющий наибольшую в мире тягу 86 кН. Двигатель АМ-3 в начале 50-х годов был установлен на дальнем бомбардировщике Ту-16, а его модифицированный вариант РД-ЗМ (максимальная стендовая тяга 95 кН) – на первом турбореактивном пассажирском самолете Ту-104, вышедшим на воздушные трассы в 1956 г. Наряду с турбореактивными двигателями в СССР созданы первоклассные ТВД для пассажирских и транспортных самолетов. Так, турбовинтовой двигатель НК-12МВ конструкции Н. Д. Кузнецова, работа по созданию которого были начаты еще в 1954 г., вплоть до настоящего времени не имеет себе равных в мире среди ТВД по мощности и экономичности (взлетная мощность более 11000 кВт, удельный расход топлива 0,28 кг/кВт-ч). Двигателями НК-12МВ вначале оборудовали пассажирский самолет Ту-114, а позднее – транспортный самолет Ан-22, «Антей», на котором в октябре 1967 г. был поднят самый большой для того времени груз (более 100 т на высоту 7848 м).
ТВД АИ-20 конструкции А. Г. Ивченко, заложенный в опытное производство с 1956 г., получил широкое применение на высокоэкономичных пассажирских самолетах Ил-18 и Ан-10, которые внесли основной вклад в обеспечение рентабельности воздушных перевозок. Двигатель АИ-20 имел наибольший для своего времени межремонтный ресурс (4000 ч, а отдельные экземпляры до 6000… 8000 ч) и высокую безотказность, достигающую уровня лучших мировых образцов ГТД данного класса. На базе двигателя АИ-20 конструкторским коллективом, руководимым А. Г. Ивченко, создан ТВД АИ-24, имеющий примерно в 1,7 раза меньшую мощность и установленный на самолет Ан-24, который до настоящего времени выполняет основной объем пассажирских перевозок на местных воздушных линиях.
Первым в нашей стране серийным ТРДД был двигатель Д-20П, созданный в 1960 г. под руководством П. А. Соловьева для пассажирского самолета Ту-124. В дальнейшем конструкторским коллективом, возглавляемым П. А. Соловьевым, построены ТРДД Д-30, Д-З0КП и Д-З0КУ, установленные на широко известные самолеты Ту-134, Ил-76 и Ил-62М.
Коллективом генерального конструктора Н. Д. Кузнецова в 60-х годах разработаны и построены оригинальные ТРДД семейства НК-8, примененные на скоростных пассажирских самолетах Ил-62 и Ту-154, а позже создан ТРДДФ НК-144 для сверхзвукового пассажирского самолета Ту-144 и выпущен высоконадежный двухконтурный двигатель НК-86, работающий на первом в нашей стране аэробусе Ил-86.
Ряд совершенных ТРДД разработан в конструкторском бюро, возглавляемом В. А. Лотаревым. Одним из первых двигателей этого коллектива был ТРДД АИ-25, установленный на самолет местных авиалиний Як-40. Для пассажирского самолета Як-42 и транспортного Ан-72 под руководством В. А. Лотарева создан высокоэкономичный и легкий ТРДД с большой степенью двух-контурности Д-36, который по конструктивному совершенству и удельным параметрам находится на уровне лучших мировых образцов современных ГТД данного класса.
Двигатель Д-36 был всесторонне исследован как модель построенного позже крупного ТРДД Д-18Т с тягой 230 кН. Самый большой для своего времени самолет ан-124, «Руслан», оснащенный четырьмя двигателями Д-18Т, в августе 1985г. установил мировой рекорд грузоподъемности, подняв груз массой более 171 т на высоту 10750 м. Груз, поднятый «Русланом», более чем на 60 т превышает предыдущий рекорд мира, установленный в декабре 1984 г. военно-транспортным самолетом США С-5А «Гэлакси». Всего на самолете Ан-124 зарегистрировано (за 1985 г.) 21 мировое достижение в полете.
Этапы развития, области применения и параметры ГТД
До конца второй мировой войны монопольное положение как в военной, так и в гражданской авиации занимали силовые установки с поршневыми двигателями, используемыми в качестве генераторов мощности, и воздушными винтами, выполняющими роль движителей. В период интенсивного развития поршневых двигателей (примерно 1910—1945 гг.)
В первом поколении ГТД преобладающим типом был турбореактивный двигатель, который совместил в себе функции генератора мощности и движителя, отрицая воздушный винт как движитель, имеющий ограниченные скоростные возможности Скорости истечения газа из сопла ТРД в несколько раз превышают скорости воздушных масс, отбрасываемых винтом.
В процессе эволюционного развития, протекающего, в основном, по пути увеличения температуры газа перед турбиной и степени повышения давления воздуха в компрессоре, появились труднопреодолимые недостатки турбореактивных двигателей сильно ограничившие их применение на самолетах гражданской авиации. Они обусловлены, в частности, тем, что процессы сжатия и расширения рабочего тела в лопаточных машинах происходят с большими потерями, чем в цилиндрах поршневого двигателя, из-за перетеканий воздуха и газа в зазорах между ротором и статором, повышенных потерь на трение в высокоскоростном потоке и т. п. Трудности охлаждения элементов горячей части ГТД (в основном деталей ротора турбины) намного снижают допустимую температуру газа по сравнению с достигнутой в поршневых двигателях. Все это делает рабочий процесс ТРД не столь совершенным, а КПД, соответственно, меньшим. По принципу создания тяги ТВД отрицает ТРД, в результате чего происходит возврат к исходной схеме силовой установки «двигатель – воздушный винт», но на значительно более высоком уровне развития, так как турбовинтовой двигатель не имеет таких жестких весовых ограничений по мощности, как поршневой [1].
Турбовинтовые двигатели обеспечили возможность существенного (по сравнению с поршневыми) увеличения скорости и грузоподъемности самолетов за счет избытка располагаемой мощности при малой массе конструкции и позволили достичь большой дальности полета благодаря высокой топливной экономичности, характерной для силовых установок с воздушным винтом.
Разработанные ТВД послужили основой для создания вертолетных ГТД, выполняемых, как правило, без встроенного редуктора и с расположенной на отдельном валу свободной (силовой) турбиной, используемой для привода несущего винта через выносной редуктор. Такие ГТД получили название турбовальных двигателей со свободной турбиной (ТВлД). Замена ими поршневых двигателей позволила существенно повысить мощность вертолетных силовых установок при незначительном увеличении их массы и увеличить за счет этого грузоподъемность вертолетов.
По мере накопления опыта проектирования ГТД появилась возможность создания газогенераторов, надежно работающих при Тг=1500… 1650 К, и степени сжатия воздуха 20…30, и высоконагруженных одноступенчатых вентиляторов со сверхзвуковым обтеканием лопаток со степенью сжатия равной 1,4…1,6, что позволило повысить степень двухконтурности ДТРД до 6…8 и снизить за счет этого удельный расход топлива до 0,032…0,038 кг/ч на взлетном режиме при одновременном уменьшении удельного веса.
Столь существенное улучшение параметров достигнуто благодаря широкому применению двух- и трехвальных схем, повышению КПД узлов конструктивными мероприятиями, использованию конвективно-пленочного охлаждения лопаток турбин, дальнейшему совершенствованию материалов и технологических процессов и т. п.
Дальнейшее развитие ГТД для самолетов гражданской авиации протекает, в основном, по пути улучшения их топливной экономичности. Резервы для этого есть, в частности потому, что существующие ДТРД с большой степенью двухконтурности еще не достигли уровня ТВД по удельному расходу топлива. Радикальным средством уменьшения удельного расхода топлива ДТРД является дальнейшее увеличение степени двухконтурности, которое, однако, в рамках их схемы может привести к значительному возрастанию удельного веса, что недопустимо. Поэтому в настоящее время созданы и проходят опытную доводку ГТД качественно нового типа – винтовентиляторные двигатели (ТВВД), в которых движителем является винтовентилятор (ВВ), представляющий собой малогабаритный высоконагруженный многолопастной воздушный винт изменяемого шага. Диаметр ВВ примерно на 40% меньше диаметра обычного винта, поэтому он может допустить большую скорость полета (до 850 км/ч) при сохранении КПД на приемлемом уровне.
Удельный расход топлива винтовентиляторных двигателей должен быть ниже, чем у ТВД классической схемы, так как их газогенераторы имеют (в соответствии с достигнутым уровнем развития) значительно более высокие параметры рабочего цикла и эффективный КПД. За счет прироста скорости полета ТВВД могут обеспечить для самолетов уменьшение расхода топлива на единицу транспортной работы примерно на одну треть по сравнению с лучшими ТВД.
Возникшее противоречие между необходимостью повышения температуры газа и ограниченными прочностными возможностями турбины было разрешено созданием на основе ТРД нового типа газотурбинного двигателя (ТРДФ) с подогревом газа путем сжигания дополнительного количества топлива в специальной камере сгорания (форсажной камере), расположенной между турбиной и реактивным соплом.
При больших дозвуковых и околозвуковых скоростях целесообразно применять ДТРД. Высокотемпературные ТРД могут обеспечить малые сверхзвуковые скорости (до Мн=2,0) при высотах полета около 20 км. Полеты при скоростях, соответствующих Мн= 2,0…3,5, на высотах до 30 км освоены с помощью ТРДФ и ДТРДФ. Дальнейший переход к большим сверхзвуковым и гиперзвуковым скоростям (Мн=6…8) возможен с применением турбопрямоточных и других комбинированных двигателей.
Перспективы развития ГТД
Определяющими факторами перспективного развития транспортной авиации, по мнению специалистов, будут социально-психологический и экономический факторы.
Социально-психологический фактор объединяет такие требования, как гарантия безопасности полетов, сокращение времени передвижения, комфорт, минимальное воздействие на окружающую среду и др.
Экономический фактор содержит в себе стремление к снижению себестоимости перевозок, росту эффективности использования воздушных судов, уменьшению эксплуатационных затрат и т п. Роль двигателей здесь весьма велика, так как, например, доля расходов на эксплуатацию современных широкофюзеляжных самолетов, связанная с двигателями, составляет 40—50%. Особенно велико значение двигателей для проблемы повышения эффективности использования топлива, на которую наибольшее влияние оказывает удельный расход топлива на крейсерском режиме полета. Уменьшение крейсерского удельного расхода топлива приводит не только к непосредственному уменьшению потребного на полет запаса топлива, но и к его дополнительному снижению за счет применения для облегченного самолета двигателей меньшей тяги.
Конструктивные и силовые схемы ГТД
Конструктивные схемы авиадвигателей
Конструктивная схема дает возможность получить общее представление о компоновке и силовой схеме двигателя, т. е. о взаимном расположении и связях его узлов, а также выявить наиболее характерные особенности конструкции основных элементов двигателя.
Конструктивные схемы современных двигателей чрезвычайно разнообразны и определяются, с одной стороны, типом ГТД, а с другой – его целевым назначением. Наиболее распространена так называемая последовательная схема расположения основных узлов: входного устройства, компрессора, камеры сгорания, газовой турбины и выходного устройства. При такой компоновке движение потока в проточной части ГТД совершается с наименьшими потерями, практически все узлы двигателя имеют осесимметричную структуру, упрощающую технологию их изготовления. Двигатель при этом ориентирован в осевом направлении, что облегчает его размещение на воздушном судне с минимальным лобовым сопротивлением. Последнее обстоятельство имеет определяющее значение прежде всего для маршевых ГТД: ТРД, ДТРД, ТВД.
Характерными типами ГТД являются турбореактивные одноконтурные, турбовальные (в том числе турбовинтовые) и турбореактивные двухконтурные двигатели. Последние занимают промежуточное положение между двумя первыми типами и являются наиболее распространенными в гражданской авиации. Кроме того, на воздушных судах широкое применение нашли ВСУ, представляющие собой малогабаритные ГТД различного назначения.
Двухконтурные турбореактивные двигатели (ДТРД)
ДТРД – наиболее распространенный тип ГТД в гражданской авиации. Конструктивные схемы ДТРД весьма разнообразны, но широкое применение нашли лишь некоторые из них.
Как и в случае ТРД, конструктивная схема определена прежде всего числом роторов. Двигатели со средней степенью двухконтурности (2…3), как правило, выполняют двухвальными. Ротор ВД – двух- или трехопорный, ротор НД – трех- или четырехопорный, причем по меньшей мере одна из опор выполняется межвальной. Между КНД и КВД располагается переходный корпус компрессора, служащий для размещения элементов опор, агрегатов и приводов к ним. КНД является обычно общим для обоих контуров: КВД располагается во внутреннем контуре. В ряде случаев для оптимизации параметров ДТРД часть ступеней КНД размещается во внутреннем контуре. Наружный контур концентричен внутреннему и расположен вокруг КВД, камеры сгорания и турбины. В зависимости от вида выходного устройства возможны две основные схемы ДТРД: с раздельным выходом потоков и со смешением потоков. Камера смещения несколько улучшает удельные параметры двигателя, позволяет упростить компоновку реверсивных устройств. По этой причине для ДТРД рассматриваемого класса характерно использование смесительных устройств. Реактивное сопло у подобных ДТРД нерегулируемое.
В двигателях с большой степенью двухконтурности (5…8 и более) применяются как двух-, так и трехвальные схемы. Первые обладают более простой конструкцией, но требуют мощной механизации компрессора для обеспечения необходимой газодинамической устойчивости. Трехвальная схема более сложна, но такие ДТРД обладают лучшими эксплуатационными характеристиками. Применение двухопорных роторов для всех каскадов упрощает компоновку двигателя. ГТД подобного типа имеют, как правило, укороченный наружный контур, т. е. относятся к ДТРД с раздельным выходом потоков. Это связано с тем, что преимущества схемы с нерегулируемым смешением потоков не всегда оправдываются усложнением конструкции и увеличением массы ГТД. Раздельный выход потоков дает также возможность создать «холодное» реверсивное устройство в наружном контуре.
Турбовальные двигатели и вспомогательные силовые установки
Турбовальные двигатели представляют собой ГТД, в которых преобладающая доля энергии сгорания топлива преобразуется в работу на выходном валу, используемую в вертолетных ГТД для привода несущих, а в турбовинтовых двигателях-тянущих воздушных винтов. Таким образом, кроме элементов, характерных для всех типов ГТД, Турбовальные двигатели включают редуктор и воздушный винт. Расположение последних относительно турбокомпрессора и определяет особенности конструктивных схем этих типов двигателей. Простейшую конструкцию имеет одновальный ТВД с одним воздушным винтом. Его конструктивная схема отличается от схемы ТРД увеличенным числом ступеней турбины и более простым выходным устройством, так как оно служит в ТВД лишь для отвода газов в атмосферу без существенного преобразования энергии.
Передача мощности от турбины к винту осуществляется через редуктор. Наиболее распространена схема встроенного редуктора. Он располагается обычно в передней части двигателя и составляет с ним единое целое в силовом отношении. Двигатель имеет в этом случае специальный узел – лобовой картер, в котором располагаются каналы входного устройства (одновременно он используется для размещения агрегатов и приводов к ним). Редуктор крепится к передней части лобового картера. В качестве редукторов применяются в основном планетарные механизмы с двухвенечными сателлитами или замкнутые планетарные передачи. Реже используются двухступенчатые простые редукторы.
Так же разнообразны и конструктивные схемы ВСУ. Во-первых, они определены их целевым назначением. ВСУ используется в качестве турбокомпрессорного стартера, генератора сжатого воздуха или турбогенераторной установки. В последнее время (особенно при большом числе двигателей) на самолетах используются многоцелевые ВСУ, обеспечивающие не только запуск основных двигателей, но и кондиционирование пассажирских кабин на стоянке, питание электросистем воздушного судна как на земле, так и в полете, а иногда и некоторые другие функции.
ГТД имеет центробежный компрессор, центростремительную газовую турбину и противоточную камеру сгорания. Выходное устройство выполняет роль простейшего теплообменника. Роторы турбины и компрессора соединены валом-рессорой и расположены в жестком кольцевом корпусе, образующем силовой каркас ГТД. В ВСУ предусмотрены отбор сжатого воздуха из полости между компрессором и камерой сгорания (для запуска маршевых ГТД и кондиционирования) и отбор мощности на генератор, обеспечивающий питание электросистемы самолета.
Силовые схемы ГТД
Силовые схемы роторов
В современных ГТД, как показано при анализе конструктивных схем, имеется от одного до трех механически не связанных между собой роторов. Роторы турбокомпрессоров состоят из рабочих колес компрессора и турбины, соединенных валом; роторы свободных турбин включают систему валов, соединяющих турбины с ходовой частью редуктора. В зависимости от компоновки ГТД применяются схемы с коаксиальными валами или раздельным расположением соединительных валов.
В зависимости от числа опор различают двух-, трех- и четырехопорные роторы
Роторы турбины и компрессора соединяются в двухоперной схеме жестко.
Схема трехопорных роторов получила более широкое распространение В этом случае ротор компрессора установлен на два, а ротор турбины – на один подшипник (вторым своим концом он опирается на ротор компрессора) Соединение роторов турбины и компрессора осуществляется соединительной муфтой, обеспечивающей передачу крутящего момента, а также осевой и радиальной сил в условиях несоосности роторов.
Силовые схемы статоров
Силовая схема статора (корпуса) представляет собой систему связанных неподвижных узлов, которая воспринимает нагрузки, действующие в двигателе, и передает их равнодействующие через узлы подвески на воздушное судно. Силовой корпус двигателя состоит из нескольких опор (на которые передаются нагрузки от подшипников роторов), соединенных между собой корпусами компрессоров, камеры сгорания, турбины и наружного контура (в ДТРД). К нему присоединяются элементы входного и выходного устройств (если они не выполнены в виде отдельных узлов со своими элементами крепления к воздушному судну), а также коробки приводов и агрегаты.
Статор двигателя должен обладать необходимой прочностью и жесткостью при минимальных габаритах и массе.
Классификацию силовых схем статоров можно провести в зависимости от способов силовой связи между турбиной и компрессором.
Схема с внутренней силовой связью характеризуется тем, что соединение статоров турбины и компрессора осуществляется с помощью внутренней стенки корпуса камеры сгорания.
Схема с внешней силовой связью отличается тем, что соединение статоров компрессора и турбины осуществляется наружным корпусом камеры сгорания. Последний, благодаря большему диаметру, оказывается достаточно жестким при сравнительно малой массе и более простой конструкции.
Подвеска двигателя к воздушному судну
Подвеска двигателя осуществляется с помощью специальных узлов, монтируемых на корпусе двигателя, и подмоторных рам, относящихся к конструкции воздушного судна. Узлы крепления двигателя нагружаются силой тяги, силами инерции и другими свободными силами и моментами. В ТВД к ним относятся прежде всего моменты, обусловленные реакцией воздушного винта.
Двигатель крепится к воздушному судну, как правило, в двух плоскостях. Плоскость, в которой осуществляется передача силы тяги, носит название основной. Вторая плоскость подвески соответственно называется дополнительной или вспомогательной. В обеих плоскостях крепления необходимо обеспечить свободные температурные расширения корпуса ГТД в радиальном направлении, а во вспомогательной плоскости – дополнительно и в осевом направлении.
Основная плоскость подвески обычно располагается возможно ближе к центру масс двигателя, дополнительная – как можно дальше от первой.
Компоновки осевых компрессоров
Компрессор, являясь одним из основных узлов ГТД, во многом определяет конструктивное совершенство двигателя в целом, его экономичность и надежность.
Как известно из теории авиационных двигателей, по направлению движения воздуха в проточной части компрессоры делятся на центробежные, осевые и диагональные. Применяют также кoмбиниpoванныe схемы компрессоров, например, осецентробежные, диагонально-осевые и др.
Конструктивные компоновки компрессоров зависят от типа ГТД, потребной степени повышения давления, степени двухконтурности и других параметров. Они характеризуются числом роторов и ступеней, формой проточной части, числом и расположением опор, конструктивными типами роторов и статоров.
Для ТРД и ТВД малых тяг и мощностей, имеющих низкие параметры рабочего процесса (степень сжатия = 6…8, Т*г=1150…1250 К), применяют однокаскадные компрессоры, в которых число ступеней не превышает 8…10. Роторы таких компрессоров обычно выполняют по двухопорной схеме. Проточную часть используют с постоянным наружным диаметром, при котором корпус имеет простую в изготовлении цилиндрическую форму, а последние ступени, благодаря возрастанию среднего диаметра, обладают достаточно высокой напорностью.
В ГТД с умеренными параметрами (степенью сжатия = 10…15, Т*г =1250…1350 К) и относительно высокими параметрами (степенью сжатия = 15…25, Т*г =1450… 1550 К.) параметрами рабочего процесса применяют двухкаскадные компрессоры с независимыми приводами от отдельных турбин, обладающие повышёнными по сравнению с однокаскадными схемами запасами газодинамической устойчивости. В указанных типах ГТД КНД имеют от четырех до шести ступеней, а число ступеней КВД достигает 6…8 и более.
Трехкаскадные компрессоры используют в ТРДД с большой степенью двухконтурности (m = 4…8) при степени сжатия = 20…30 и выше. Вентиляторы таких ДТРД обычно выполняют одноступенчатыми сверхзвуковыми со степенью повышения давления = 1,4…1,6 (до 1,8).
Роторы осевых компрессоров
Ротор – это вращающаяся часть компрессора. Он включает в себя следующие элементы: рабочие лопатки; диски (или барабан), на которых закреплены рабочие лопатки; вал или цапфы, с помощью которых ротор опирается через подшипники на силовой корпус двигателя; элементы крепления дисков между собой и дисков с валом или цапфами.
В настоящее время различают три конструктивных типа роторов: барабанные, дисковые и смешанные (барабанно-дисковые).
Дисковый ротор состоит из отдельных облопаченных дисков, соединенных своими ступицами с общим валом, который служит для передачи крутящего момента на диски и размещения подшипников опор. Каждый диск имеет наружный обод для крепления лопаток, центральную утолщенную часть – ступицу для соединения с валом и среднюю тонкую часть – полотно.
Рабочие лопатки являются главными элементами ротора компрессора. В межлопаточных каналах рабочих колес происходит преобразование работы вращения ротора в кинетическую энергию движения воздуха и одновременно в потенциальную энергию его давления. Все остальные элементы конструкции ротора служат только для передачи механической энергии к рабочим лопаткам с целью сообщения им окружного перемещения в проточной части с заданной скоростью.
В простейшем случае рабочая лопатка состоит из профилированной части-пера и хвостовика, предназначенного для крепления лопатки в диске или барабане. Во многих случаях лопатки имеют также полки хвостовиков, используемые для формирования внутренней поверхности проточной части рабочего колеса.
Для повышения КПД ступени перо лопатки тщательно профилируют в процессе проектирования и изготовления. Линейные и угловые размеры выдерживают с большой степенью точности.
Поверхность пера обрабатывают до высокой чистоты с целью уменьшения гидравлических потерь и повышения усталостной прочности лопатки. Переходы от пера к. хвостовику или его полке выполняют с плавными округлениями для снижения концентрации напряжении.
Крепление рабочих лопаток наиболее часто осуществляют с помощью хвостовиков типа «ласточкин хвост», устанавливаемых в продольные трапециевидные пазы ободов дисков.
Массивные лопатки вентиляторов ДТРД иногда крепят в продольных пазах ободов дисков с помощью хвостовиков елочного типа. Такое крепление обладает повышенной, по сравнению с другими типами креплений, несущей способностью и позволяет разместить на ободе большее число лопаток.
Для повышения жесткости длинных лопаток вентиляторов ДТРД и демпфирования их колебаний на профильной части лопаток выполняют антивибрационные полки, между которыми в рабочем колесе осуществляют плотный контакт. Демпфирование колебаний обеспечивается силами трения, возникающими в зонах контакта полок.
Статоры осевых компрессоров
Статор – это неподвижная часть компрессора. В его состав входят следующие основные элементы: направляющие аппараты; корпус компрессора, состоящий из корпусов направляющих аппаратов и корпусов опор; входные направляющие и спрямляющие аппараты; различные оболочковые конструкции, например кок двигателя, оболочки наружного контура и проч.
Направляющие аппараты (НА) устанавливают за рабочими колесами для частичной раскрутки потока воздуха и дальнейшего повышения его давления в диффузорных межлопаточных каналах за счет снижения скорости потока в абсолютном движении.
Входные направляющие аппараты (ВНА) устанавливают перед рабочими колесами первых ступеней для предварительной закрутки воздуха обычно по направлению вращения ротора с целью снижения относительной скорости потока в рабочем колесе. Межлопаточные каналы ВНА профилируют конфузорными. В них происходит увеличение абсолютной скорости потока и его кинетической энергии
Лопатки ВНА часто выполняют с обогреваемыми входными кромками, во внутренние полости которых подводят горячий воздух от последних ступеней компрессора для предотвращения обледенения кромок. Применяют также для этой цели пустотелые лопатки со вставными дефлекторами, обеспечивающими эффективный подогрев лопаток при небольших расходах воздуха.
Спрямляющие аппараты (СпА) устанавливают в некоторых компрессорах за направляющими аппаратами последних ступеней с целью полной раскрутки воздушного потока.
В корпусе любой опоры компрессора (равно как и турбины) можно выделить три характерных группы элементов: внутреннее кольцо, в котором размещен узел подшипника; наружное кольцо, необходимое для соединения корпуса опоры с другими частями силового корпуса двигателя; радиальные силовые элементы, соединяющие между собой вышеназванные кольца, в результате чего образуется жесткая осесимметричная кольцевая рама.
Существенное влияние на КПД компрессора оказывает величина радиального зазора между концевыми профилями рабочих лопаток и элементами корпуса НА, через который происходит непроизводительное перетекание воздуха со стороны выхода из рабочего колеса на его вход под действием разности давлений. Увеличение относительного радиального зазора (отношения зазора к высоте лопаток) во всех ступенях на 1% приводит к уменьшению КПД компрессора на 3%, что сопровождается возрастанием удельного расхода топлива до 10%. Поэтому величину радиального зазора необходимо уменьшать до предельно возможного значения
В процессе работы двигателя величина относительного радиального зазора изменяется в широких пределах под действием эксплуатационных нагрузок и температур, вызывающих возникновение силовых и термических деформаций статора и ротора. Так, например, при запуске и любых переходах двигателя на повышенные режимы менее массивный корпус компрессора нагревается до более высоких температур, чем ротор, поэтому радиальные температурные деформации статора, суммируясь с деформациями от избыточного внутреннего давления воздуха, приводят к существенному увеличению радиального зазора. На крейсерских режимах этот зазор также больше, чем на неработающем двигателе. При выключении двигателя (особенно в условиях низких температур атмосферного воздуха на земле или в полете) корпус охлаждается значительно быстрее ротора, что сопровождается резким уменьшением температуры газов (возможно до нуля и ниже), которое может вызвать заклинивание ротора в статоре, разрушение рабочих лопаток и т. п.
Для предотвращения разрушения рабочих лопаток в случае их касания о корпус на внутреннюю поверхность элементов корпуса НА наносят мягкое покрытие толщиной 1…3 мм, которое называют уплотнительным слоем. При уменьшении зазора до нуля и ниже рабочие лопатки легко срезают часть этого слоя, не получая повреждений.
В состав уплотнительного слоя входят следующие материалы: графит, тальк, асбест, алюминиевый порошок и другие компоненты. Из указанных материалов и специальных лаков изготавливают пасту, которая по составу должна быть различной для первых и последних ступеней в связи с различными температурными условиями. Пасту наносят на специально подготовленную шероховатую поверхность в кольцевые расточки корпуса НА или на рабочие кольца, затем высушивают в электропечи и растачивают на заданные диаметры для всех ступеней одновременно при полностью собранном корпусе НА.
В последних ступенях высоконапорных компрессоров, где температура воздуха может достигать 650…700 °С, вместо мягких покрытий на основе вышеуказанных материалов применяют термостойкие металлокерамические или сотовые вставки, используемые в газовых турбинах.
Для уменьшения перетеканий воздуха под действием разности давлений со стороны выхода из направляющего аппарата в сторону входа через радиальный зазор между НА и ротором компрессора обычно применяют межступенчатые лабиринтные уплотнения.
Для создания межступенчатого лабиринтного уплотнения на элементах ротора между рабочими колесами выполняют заостренные выступы (лабиринтные гребни), относительно которых с небольшим зазором устанавливают внутреннее бандажное кольцо НА с нанесенным на его внутреннюю поверхность уплотнительным слоем.
Для защиты входа в компрессор от посторонних предметов (камней, града, птиц, пыли и т. д.) изучены возможности применения защитных сеток или решеток, устройств струйного и инерционного типов. Несмотря на большую важность данной проблемы отмеченные защитные устройства не получили широкого практического применения, главным образом из-за существенного их отрицательного влияния на топливную экономичность двигателей, обусловленного большими потерями на преодоление гидравлических сопротивлений входа. Защитные устройства применяют, в основном, для вертолетных ГТД, которые работают в условиях запыленной воздушной среды, что приводит к интенсивному эрозионному износу лопаток компрессора. Используют при этом пылезащитные устройства (ПЗУ) инерционного типа с криволинейными входными каналами, сформированными таким образом, что при повороте потока центробежные силы перемещают частицы пыли в пылесборники.
Конец ознакомительного фрагмента.
На пути к Т-80: танковые газотурбинные двигатели
В пятидесятых годах прошлого века широкое распространение получили газотурбинные двигатели (ГТД) различных классов. Турбореактивные моторы разгоняли авиацию до сверхзвуковых скоростей, а по воде и железным дорогам двигались локомотивы и корабли с первыми моделями газотурбинных двигателей. Предпринимались попытки оснастить такими моторами и грузовики, однако эти эксперименты оказались неудачными. Подобные силовые установки, при всех своих плюсах – экономичности на номинальном режиме работы, компактности и возможности применять различные типы топлива – не были лишены недостатков. Прежде всего, это слишком большой расход топлива при разгоне или торможении, что в итоге и определило нишу, в которой ГТД нашли свое применение. Одним из итогов различных экспериментов с такой силовой установкой стал советский танк Т-80. Но достижение всемирной известности было далеко не простым делом. От начала работ по созданию танкового ГТД до начала его серийного производства прошло почти два десятка лет.Первые проекты
Идея сделать танк с газотурбинной силовой установкой появилась еще тогда, когда никто и не думал о проекте Т-80. Еще в 1948 году конструкторское бюро турбинного производства Ленинградского Кировского завода начало работу над проектом танкового ГТД мощностью в 700 лошадиных сил. К сожалению, проект был закрыт за бесперспективностью. Дело в том, что 700-сильный двигатель, по расчетам, потреблял чрезвычайно много топлива. Расход признали слишком большим для практического использования. Чуть позже неоднократно предпринимались попытки сконструировать другие двигатели подобного класса, но они тоже не дали никакого результата.
Во второй половине пятидесятых годов ленинградские конструкторы создали еще один двигатель, который дошел до стадии сборки прототипа. Получившийся ГТД-1 не оснащался теплообменником и выдавал мощность до тысячи лошадиных сил при расходе топлива в 350-355 г/л.с. ч. Вскоре на основе этого двигателя сделали две модификации: ГТД1-Гв6 со стационарным теплообменником и ГТД1-Гв7 с вращающимся. К сожалению, несмотря на некоторый прогресс, все три модели ГТД имели расход топлива выше расчетного. Улучшить этот параметр не представлялось возможным, поэтому проекты закрыли.

В целом, все ранние проекты ГТД для сухопутной, в том числе и гусеничной, техники не отличались особыми успехами. Все они не смогли добраться до серийного производства. В то же время, в ходе разработки и испытаний новых моторов удалось найти немало новых оригинальных технических решений, а также собрать нужную информацию. К этому времени сформировались две основные тенденции: попытки приспособить авиационный двигатель для использования на танке и сделать специальный ГТД.
В начале шестидесятых годов произошло несколько событий, которые позитивно сказались на всем направлении. Сначала Научно-исследовательский институт двигателей (НИИД) предложил несколько вариантов моторно-трансмиссионного отделения для танка Т-55. Предлагались два варианта газотурбинного двигателя, отличавшиеся друг от друга мощностью и потреблением топлива. В апреле 1961 года вышло соответствующее распоряжение руководства страны, согласно которому НИИД должен был продолжить работы по начатым проектам, а на Челябинском тракторном заводе создавалось специальное конструкторское бюро, занятое исключительно тематикой ГТД.
Челябинские двигатели
Новое бюро получило индекс ОКБ-6 и объединило усилия с Институтом двигателей. Результатом проектирования стал проект ГТД-700. При мощности до 700 л.с. этот двигатель потреблял 280 г/л.с.ч, что приближалось к требуемым значениям. Столь высокие для своего времени характеристики были обусловлены рядом оригинальных решений. Прежде всего необходимо отметить конструкцию теплообменника, каналы которого были оптимизированы в плане сечения и скорости течения газов. Кроме того, на работе двигателя благотворно сказался новый одноступенчатый воздухоочиститель циклонного типа, задерживавший до 97% пыли. В 1965 году начались испытания двух первых образцов ГТД-700. Работа двигателей на стенде показала все преимущества примененных решений, а также позволила вовремя определить и исправить имеющиеся проблемы. Вскоре собрали еще три двигателя ГТД-700, один из которых позже был установлен на опытный танк «Объект 775Т». В марте 1968 года прошел первый запуск газотурбинного двигателя на танке и через несколько дней начались ходовые испытания. До апреля следующего года экспериментальный танк прошел около 900 километров при наработке двигателя порядка 100 часов.

Несмотря на имеющиеся успехи, в 1969 году испытания двигателя ГТД-700 завершились. В это время прекратились работы над ракетным танком «Объект 775» и, как следствие, его газотурбинной модификацией. Однако развитие двигателя не остановилось. По результатам испытаний сотрудники НИИД провели несколько исследований и пришли к позитивным выводам. Как оказалось, конструкция ГТД-700 позволяла довести мощность до уровня порядка 1000 л.с., а расход топлива снизить до 210-220 г/л.с.ч. Перспективная модификация двигателя получила обозначение ГТД-700М. Ее расчетные характеристики выглядели многообещающе, что привело к дальнейшим разработкам. ВНИИТрансмаш (переименованный ВНИИ-100) и конструкторское бюро ЛКЗ предприняли попытку установить ГТД-700М на танки «Объект 432» и «Объект 287». Однако никаких практических результатов добиться не удалось. Моторно-трансмиссионное отделение первого танка оказалось недостаточно большим для размещения всех агрегатов силовой установки, а второй проект вскоре был закрыт за бесперспективностью. На этом история двигателя ГТД-700 закончилась.



ГТД-3 для «Объекта 432»
Одновременно с НИИД и челябинскими конструкторами над своими проектами ГТД работали в омском ОКБ-29 (сейчас Омское моторостроительное конструкторское бюро) и ленинградском ОКБ-117 (завод им. В.Я. Климова). Стоит отметить, основным направлением работы этих предприятий была адаптация авиационных двигателей к танковым «нуждам». Этим фактом обусловлен целый ряд особенностей получившихся двигателей. Одним из первых переработке подвергся вертолетный турбовальный двигатель ГТД-3, разработанный в Омске. После адаптации для использования на танке он получил новый индекс ГТД-3Т и немного потерял в мощности, с 750 до 700 л.с. Расход топлива в танковом варианте составлял 330-350 г/л.с.ч. Такое потребление горючего было слишком велико для практического использования двигателя, но ГТД-3Т все же был установлен на ходовой макет, базой для которого послужил танк Т-54. Позже подобный эксперимент провели с танком Т-55 (проект ВНИИ-100) и с «Объектом 166ТМ» (проект Уралвагонзавода). Примечательно, что после испытаний своего опытного образца тагильские конструкторы пришли к выводу о нецелесообразности продолжения работ по газотурбинной тематике и вернулись к созданию танков с дизельными двигателями.


В 1965 году ОКБ-29 и ВНИИ-100 получили задание доработать двигатель ГТД-3Т для использования на танке «Объект 432», который вскоре был принят на вооружение под обозначением Т-64. В ходе такой доработки двигатель получил новое обозначение ГТД-3ТЛ и ряд изменений в конструкции. Изменились конструкция компрессора и корпуса турбины, появилась система перепуска газов после компрессора, созданы два новых редуктора (один в составе моторного агрегата, другой располагался на корпусе танка), а также переделана выхлопная труба. Имея сравнительно небольшие габариты, двигатель ГТД-3ТЛ хорошо вписался в моторно-трансмиссионное отделение «Объекта 432», а в свободных объемах уместились дополнительные баки на 200 литров топлива. Стоит отметить, в МТО танка пришлось ставить не только новый двигатель, но и новую трансмиссию, приспособленную для работы с газотурбинным двигателем. Крутящий момент двигателя передавался на главный редуктор и распределялся на две бортовые планетарные коробки передач. В конструкции новой трансмиссии широко использовались детали исходной системы «Объекта 432». Ввиду специфических требований двигателя к подаче воздуха пришлось заново спроектировать оборудование для подводного вождения, имеющее в своем составе воздухопитающие и выхлопные трубы большего диаметра.
В ходе проектирования двигателя ГТД-3ТЛ, с целью проверки некоторых идей, на танке Т-55 установили мотор ГТД-3Т. Танк с газотурбинным двигателем сравнили с аналогичной бронемашиной, оборудованной стандартным дизелем В-55. В результате этих испытаний подтвердились все предварительные расчеты. Так, средняя скорость опытного танка оказалась немного выше скорости серийного, но за это преимущество пришлось платить в 2,5-2,7 раза более высоким расходом топлива. При этом к моменту сравнительных испытаний не были достигнуты требуемые характеристики. Вместо необходимых 700 л.с. ГТД-3ТЛ выдавал лишь 600-610 и сжигал порядка 340 г/л.с.ч вместо требовавшихся 300. Повышенный расход топлива привел к серьезному уменьшению запаса хода. Наконец, ресурс в 200 часов не дотягивал даже до половины от заданных 500. Выявленные недостатки были учтены и вскоре появился полноценный проект ГТД-3ТЛ. К концу 1965 года ОКБ-29 и ВНИИ-100 совместными усилиями завершили разработку нового двигателя. За основу для него был взят не танковый ГТД-3Т, а авиационный ГТД-3Ф. Новый двигатель развивал мощность до 800 л.с. и потреблял не более 300 г/л.с.ч. В 1965-66 годах изготовили два новых двигателя и проверили их на танке «Объект 003», представлявшем собой доработанный «Объект 432».
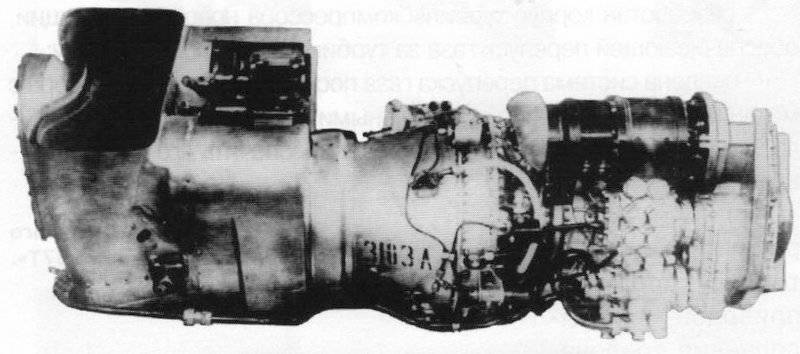

Одновременно с испытаниями танка «Объект 003» шла разработка «Объекта 004» и силовой установки для него. Предполагалось использовать двигатель ГТД-3ТП, имевший большую мощность в сравнении с ГТД-3ТЛ. Кроме того, мотор с индексом «ТП» должен был размещаться не поперек корпуса танка, а вдоль, что повлекло за собой перекомпоновку некоторых агрегатов. Основные пути развития остались прежними, но их нюансы подверглись определенным коррективам, связанным с выявленными проблемами газотурбинных двигателей. Пришлось серьезно доработать систему забора и фильтрации воздуха, а также отвода выхлопных газов. Еще один серьезный вопрос касался эффективного охлаждения двигателя. Создание новой трансмиссии, повышение характеристик и доведение моторесурса до требуемых 500 часов также остались актуальными. При проектировании двигателя и трансмиссии для танка «Объект 004» старались скомпоновать все агрегаты таким образом, чтобы они могли уместиться в МТО с минимальными его доработками.
Наибольшим изменениям подверглась крыша моторно-трансмиссионного отделения и кормовой лист бронекорпуса. Крышу сделали из сравнительно тонкого и легкого листа с окнами, на которых разместили жалюзи воздухозаборного устройства. В корме появились отверстия для выброса газов двигателя и воздуха из системы охлаждения. Для повышения живучести эти отверстия прикрыли бронированным колпаком. Двигатели и некоторые агрегаты трансмиссии укрепили на заново разработанной раме, которая монтировалась на бронекорпусе без доработок последнего. Сам двигатель установили продольно, с небольшим сдвигом от оси танка влево. Рядом с ним разместились топливный и масляный насосы, 24 прямоточных циклона системы воздухоочистки, компрессор, стартер-генератор и т.п.

Двигатель ГТД-3ТП мог выдавать мощность до 950 л.с. при расходе топлива в 260-270 г/л.с.ч. Характерной чертой этого двигателя стала его схема. В отличие от предыдущих моторов семейства ГТД-3 он был сделан по двухвальной системе. С двигателем была сопряжена четырехскоростная трансмиссия, разработанная с учетом характерных для газотурбинного двигателя нагрузок. Согласно расчетам, трансмиссия могла работать в течение всего срока службы двигателя – до 500 часов. Бортовые коробки передач имели тот же размер, что и на исходном «Объекте 432» и помещались на исходных местах. Приводы управления агрегатами двигателя и трансмиссии в большинстве своем располагались на старых местах.
Насколько известно, «Объект 004» так и остался на чертежах. В ходе его разработки удалось решить несколько важных вопросов, а также определить планы на будущее. Несмотря на уменьшение заметности танка с ГТД в инфракрасном спектре, улучшившееся качество очистки воздуха, создание специальной трансмиссии и т.п., расход топлива оставался на недопустимом уровне.
ГТД из Ленинграда
Еще одним проектом, начавшимся в 1961 году, были ленинградские исследования перспектив турбовального двигателя ГТД-350. Ленинградские Кировский завод и Завод им. Климова совместными усилиями начали изучать поставленный перед ними вопрос. В качестве стенда самых для первых исследований применялся серийный трактор К-700. На него установили двигатель ГТД-350, для работы с которым пришлось немного доработать трансмиссию. Вскоре начался еще один эксперимент. На этот раз «платформой» для газотурбинного двигателя стал бронетранспортер БТР-50П. Подробности этих испытаний не стали достоянием общественности, но известно, что по их результатам двигатель ГТД-350 признали пригодным для использования на сухопутной технике.

На его базе создали два варианта двигателя ГТД-350Т, с теплообменником и без. Без теплообменника газотурбинный двигатель двухвальной системы со свободной турбиной развивал мощность до 400 л.с. и имел расход топлива на уровне 350 г/л.с.ч. Вариант с теплообменником был ощутимо экономичнее – не более 300 г/л.с.ч., хотя и проигрывал в максимальной мощности порядка 5-10 л.с. На основе двух вариантов двигателя ГТД-350Т были сделаны силовые агрегаты для танка. При этом, ввиду сравнительно малой мощности, рассматривались варианты с применением как одного двигателя, так и двух. В результате сравнений наиболее перспективным был признан агрегат с двумя двигателями ГТД-350Т, располагавшимися вдоль корпуса танка. В 1963 году началась сборка опытного образца такой силовой установки. Его установили на шасси экспериментального ракетного танка «Объект 287». Получившуюся машину назвали «Объектом 288».
В 1966-67 годах этот танк прошел заводские испытания, где подтвердил и скорректировал расчетные характеристики. Однако главным результатом поездок по полигону стало понимание того, что перспективы спаренной системы двигателей сомнительны. Силовая установка с двумя двигателями и оригинальным редуктором получилась сложнее в производстве и эксплуатации, а также дороже, чем один ГТД эквивалентной мощности с обычной трансмиссией. Предпринимались некоторые попытки развить двухдвигательную схему, но в итоге конструкторы ЛКЗ и Завода им. Климова остановили работы в этом направлении.
Стоит отметить, проекты ГТД-350Т и «Объект 288» были закрыты только в 1968 году. До этого времени, по настоянию заказчика в лице Минобороны, состоялись сравнительные испытания сразу нескольких танков. В них участвовали дизельные Т-64 и «Объект 287», а также газотурбинные «Объект 288» и «Объект 003». Испытания были суровыми и проходили на разных местностях и в разных погодных условиях. В результате выяснилось, что при имеющихся преимуществах в части габаритов или максимальной мощности существующие газотурбинные двигатели менее пригодны для практического применения, чем освоенные в производстве дизели.

Незадолго до прекращения работ по тематике спаренных двигателей конструкторы ЛКЗ и Завода им. Климова сделали два эскизных проекта, подразумевавших установку на танк «Объект 432» спаренной установки с перспективными двигателями ГТД-Т мощностью по 450 л.с. Рассматривались различные варианты размещения двигателей, но в итоге оба проекта не получили продолжения. Спаренные силовые установки оказались неудобными для практического применения и более не использовались.
Двигатель для Т-64А
Принятый на вооружение в шестидесятых годах танк Т-64А при всех своих преимуществах не был лишен недостатков. Высокая степень новизны и несколько оригинальных идей стали причиной технических и эксплуатационных проблем. Немало нареканий вызвал двигатель 5ТДФ. В частности, и из-за них было решено всерьез заняться перспективным ГТД для этого танка. В 1967 году появилось соответствующее постановление руководства страны. К этому времени уже имелся определенный опыт в сфере оснащения танка «Объект 432» газотурбинной силовой установкой, поэтому конструкторам не пришлось начинать с нуля. Весной 1968-го года на ленинградском Заводе им. Климова развернулись проектные работы по двигателю ГТД-1000Т.

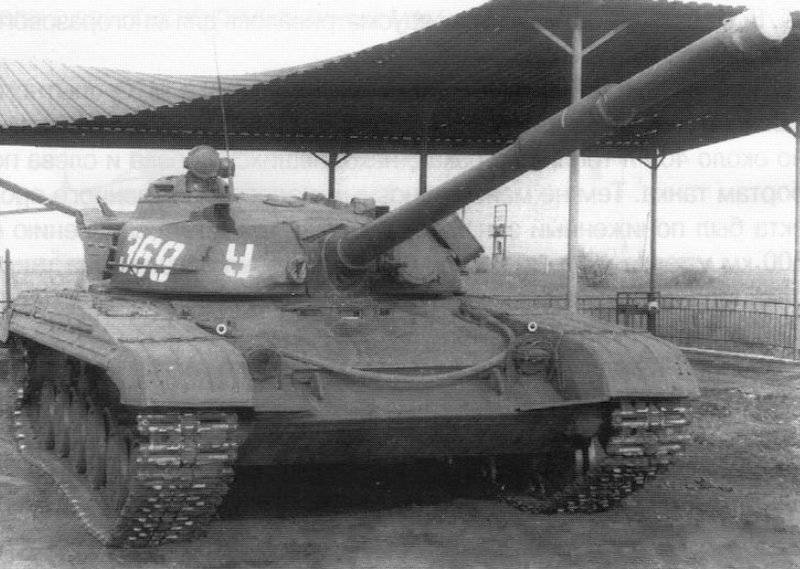
Главным вопросом, стоявшим перед конструкторами, было снижение расхода топлива. Остальные нюансы проекта уже были отработаны и не нуждались в столь большом внимании. Улучшать экономичность предложили несколькими путями: повысить температуру газов, улучшить охлаждение элементов конструкции, модернизировать теплообменник, а также повысить КПД всех механизмов. Кроме того, при создании ГТД-1000Т применили оригинальный подход: координацией действий нескольких предприятий, занятых в проекте, должна была заниматься сводная группа из 20 их сотрудников, представлявших каждую организацию.
Благодаря такому подходу достаточно быстро удалось определиться с конкретным обликом перспективного двигателя. Таким образом, в планы входило создание трехвального ГТД с двухкаскадным турбокомпрессором, кольцевой камерой сгорания и охлаждаемым сопловым аппаратом. Силовая турбина – одноступенчатая с регулируемым сопловым аппаратом перед ней. В конструкцию двигателя ГТД-1000Т сразу ввели встроенный понижающий редуктор, который мог преобразовывать вращение силовой турбины со скоростью порядка 25-26 тыс. оборотов в минуту в 3-3,2 тыс. Выходной вал редуктора разместили таким образом, что он мог передавать крутящий момент на бортовые коробки передач «Объекта 432» без лишних деталей трансмиссии.
По предложению сотрудников ВНИИТрансмаш, для очистки поступающего воздуха применили блок прямоточных циклонов. Выведение выделенной из воздуха пыли было обязанностью дополнительных центробежных вентиляторов, которые, кроме того, обдували масляные радиаторы. Использование такой простой и эффективной системы очистки воздуха привело к отказу от теплообменника. В случае его использования для достижения требуемых характеристик требовалось очищать воздух почти на все 100%, что было, как минимум, очень сложно. Двигатель ГТД-1000Т без теплообменника мог работать даже если в воздухе оставалось до 3% пыли.


Отдельно стоит отметить компоновку двигателя. На корпусе собственно газотурбинного агрегата установили циклоны, радиаторы, насосы, маслобак, компрессор, генератор и прочие части силовой установки. Получившийся моноблок имел габариты, пригодные для установки в моторно-трансмиссионное отделение танка Т-64А. Кроме того, в сравнении с оригинальной силовой установкой, двигатель ГТД-1000Т оставлял внутри бронированного корпуса объем, достаточный для размещения баков на 200 литров топлива.
Весной 1969 года началась сборка опытных экземпляров Т-64А с газотурбинной силовой установкой. Интересно, что в создании прототипов участвовали сразу несколько предприятий: Ленинградский Кировский и Ижорский заводы, Завод им. Климова, а также Харьковский завод транспортного машиностроения. Чуть позже руководство оборонной промышленности решило построить опытную партию из 20 танков Т-64А с газотурбинной силовой установкой и распределить их по различным испытаниям. 7-8 танков предназначались для заводских, 2-3 для полигонных, а оставшиеся машины должны были пройти войсковые испытания в разных условиях.


За несколько месяцев испытаний в условиях полигонов и испытательных баз было собрано нужное количество информации. Двигатели ГТД-1000Т показали все свои преимущества, а также доказали пригодность для использования на практике. Однако выяснилась другая проблема. При мощности в 1000 л.с. двигатель не слишком удачно взаимодействовал с имеющейся ходовой частью. Ее ресурс заметно снижался. Более того, к моменту окончания испытаний почти все двадцать опытных танков нуждались в ремонте ходовой или трансмиссии.
На финишной прямой
Самым очевидным решением проблемы выглядела доработка ходовой части танка Т-64А для использования вместе с ГТД-1000Т. Однако такой процесс мог занять слишком много времени и с инициативой выступили конструкторы ЛКЗ. По их мнению, нужно было не модернизировать имеющуюся технику, а создавать новую, изначально рассчитанную под большие нагрузки. Так появился проект «Объект 219».

Как известно, за несколько лет разработки этот проект успел претерпеть массу изменений. Корректировались почти все элементы конструкции. Точно так же доработкам подвергся и двигатель ГТД-1000Т и сопряженные с ним системы. Пожалуй, самым главным вопросом в это время было повышение степени очистки воздуха. В результате массы исследований выбрали воздухоочиститель с 28 циклонами, оснащенными вентиляторами с особой формой лопасти. Для уменьшения износа некоторые детали циклонов покрыли полиуретаном. Изменение воздухоочистительной системы сократило поступление пыли в двигатель примерно на один процент.
Еще во время испытаний в Средней Азии проявилась другая проблема газотурбинного двигателя. В тамошних грунтах и песках было повышенное содержание кремнезема. Такая пыль, попав в двигатель, спекалась на его агрегатах в виде стекловидной корки. Она мешала нормальному течению газов в тракте двигателя, а также увеличивала его износ. Эту проблему пытались решить при помощи специальных химических покрытий, впрыска в двигатель особого раствора, создания вокруг деталей воздушной прослойки и даже применения неких материалов, постепенно разрушавшихся и уносивших с собой пригоревшую пыль. Однако ни один из предложенных методов не помог. В 1973 году эту проблему решили. Группа специалистов Завода им. Климова предложила установить на наиболее подверженную загрязнению часть двигателя – сопловой аппарат – специальный пневмовибратор. При необходимости или через определенный промежуток времени в этот агрегат подавался воздух от компрессора и сопловой аппарат начинал вибрировать с частотой в 400 Гц. Налипшие частички пыли буквально стряхивались и выдувались выхлопными газами. Чуть позже вибратор заменили восемью пневмоударниками более простой конструкции.
В результате всех доработок наконец удалось довести ресурс двигателя ГТД-1000Т до требуемых 500 часов. Расход топлива танков «Объект 219» был примерно в 1,5-1,8 раза больше, чем у бронемашин с дизельными двигателями. Соответствующим образом сократился и запас хода. Тем не менее, по совокупности технических и боевых характеристик танк «Объект 219сп2» признали пригодным для принятия на вооружение. В 1976 году вышло постановление Совмина, в котором танк получил обозначение Т-80. В дальнейшем эта бронемашина претерпела ряд изменений, на ее базе было создано несколько модификаций, в том числе и с новыми двигателями. Но это уже совсем другая история.


По материалам сайтов:
журнал ««Техника и вооружение: вчера, сегодня, завтра…»»
http://armor.kiev.ua/
http://army-guide.com/
http://t80leningrad.narod.ru/
Газотурбинный двигатель
Газотурбинный двигатель успешно применяется в танках и авиации. К сожалению, ряд конструктивных ограничений не позволяет использовать эту прогрессивную конструкцию в качестве силовой установки для легкового автомобиля.
Преимущество двигателей этого типа в том, что у них самая большая удельная мощность среди существующих силовых установок, относящихся к двигателям внутреннего сгорания, до 6 кВт/кг. Кроме того, газотурбинный двигатель может работать на различных видах жидкого топлива, а не только на бензине или дизеле.
История создания газотурбинного двигателя
Первая газовая турбина была разработана в 1519 году. Она существенно отличалась от современных устройств и применялась в «сфере малой механизации». Турбина вращала вертел, предназначенного для жарки мяса. Использовалась газовая турбина и для приведения в движение повозки изобретателя Джона Барбера.
Один из первых газотурбинных двигателей для танков разработала компания BMW в 1944 году. Он был опробован на самоходной установке «Пантера»
В 1950 году компанией «Rover» был разработан газотурбинный двигатель, предназначенный для автомобилей. В результате появилась экспериментальная модель гоночного автомобиля «JET1». Двигатель машины был расположен позади сидений, по бокам монтировались воздухозаборники, а на верхней задней части находились отверстия для выхода выхлопных газов. Скорость вращения турбины достигала 50 тысяч оборотов за 1 минуту. В качестве топлива использовался бензин, парафиновое масло и дизельное топливо. Максимальная скорость, с которой могла двигаться машина, составляла 140 км/ч. Из-за значительного расхода топлива автомобили с газотурбинным двигателем не пользовались особым спросом.
Единственный случай применения газотурбинного двигателя в конструкции мотоцикла — MTT Y2K Turbine Superbike с ДВС Rolls-Royce-Allison Model 250
Модернизировав устройство и сконструировав модель «BRM», копания «Rover» приняла участие в гоночных соревнованиях 1963 года и установила рекорд: машина разгонялась до скорости 229 км/ч. Позже в аналогичных соревнованиях участвовали и другие автомобильные производители. Например, компания «Howmet» выпустила модель «TX», которая работала на газотурбинном двигателе и неоднократно становилась гоночным фаворитом.
Единственная в истории модель серийного автомобиля с газотурбинным двигателем, предназначенного для передвижения по дорогам общего пользования, была выпущена американским концерном Chrysler в 1963 году. Пятьдесят экземпляров автоьмобля под названием Chrysler Turbine были вручную собраны специалистами итальянского кузовного ателье Ghia. В продажу автомобили не поступали, а были розданы добровольцам, на два года для тестирования. Эксперимент прошёл удачно, но для запуска нового производства требовалась постройка завода по выпуску двигателей нового типа, и концерн Chrysler не рискнул инвестировать большие деньги. В семидесятые годы, когда в США существенно ужесточились экологические нормы, и, вдобавок, начался топливный кризис, взвинтивший цены на нефть компания отказалась от продолжения разработок.
Устройство и принцип действия газотурбинного двигателя
Попадая в компрессор, воздух подвергается сжатию и нагреванию. Далее он поступает в камеру сгорания, куда также подается и часть топлива. Из-за высокой скорости воздух и топливо воспламеняются при столкновении. Во время сгорания смеси выделяется энергия, которая преобразуется в механическую работу за счет вращения. Часть данной энергии используется для сжатия воздуха в компрессоре. Другая часть поступает в электрический генератор. После этого отработавшие газы отправляются в утилизатор.
Достоинства и недостатки газотурбинных двигателей
Газотурбинные двигатели во многом превосходят поршневые моторы. Благодаря способности развивать большие обороты устройство отличается высокой мощностью, но при этом имеет компактные размеры. В качестве топлива используют керосин или дизельное топливо. Масса газотурбинного двигателя в 10 раз меньше массы аналогичного по мощности двигателя внутреннего сгорания. Ввиду отсутствия трущихся деталей газовая турбина не требует наличия разветвленной системы охлаждения.
Инженеры Chrysler, создавшие единственный мелкосерийный автомобиль с газотурбинным двигателем, опытным путем выяснили, что лучшее топливо для ГТД — обычный керосин
Основным недостатком становится повышенный расход топлива, вызванный необходимостью искусственного ограничения температуры газов. Это ограничение связано с тем, что в случае с автомобилем двигатель устанавливается внутри кузова, а не под крылом, как, у самолета, например. Соответственно, температура двигателя не должна превышать 700 градусов. Металлы, устойчивые к таким температурам, имеют очень высокую стоимость. Эта проблема часто вызывает интерес у ученых, и в скором будущем должны появиться газотурбинные двигатели, обладающие хорошими показателями экономичности. Очевидно, это произойдет только в том случае, если будет решена проблема отвода большого количества тепла, что позволит ставить на автомобили «незадушенные» двигатели, в конструкции которых проблема экономичности решена. Среди недостатков также следует отметить высокие требования к качеству атмосферного воздуха и отсутствие возможности торможения двигателем.
Двухвальный газотурбинный двигатель, оснащенный теплообменником
Этот тип двигателей встречается наиболее часто. По сравнению с одновальными аналогами, данные устройства соответствуют более высоким требованиям к динамике автомобилей. Двухвальные агрегаты предполагают наличие специальной (для привода компрессора) и тяговой (для привода колес) турбин, валы которых не соединены. Такие двигатели позволяют улучшить динамические свойства машины и дают возможность сократить количество ступеней в коробке передач.
После отказа от массового производства автомобилей с газотурбинными двигателями компания Chrysler уничтожила большую часть тестовых экземпляров, чтобы «турбины не попали на авторазборки»
В отличие от поршневых моторов, двухвальные газотурбинные установки предполагают автоматическое возрастание крутящего момента при увеличении нагрузки. Благодаря этому переключение коробки передач требуется значительно позже или вообще не требуется. При равной мощности автомобили с двухвальным газотурбинным двигателем разгоняются быстрее, чем машины с поршневыми моторами. Недостатками данного вида является сложность изготовления, увеличение размеров и веса вследствие наличия дополнительных деталей: теплообменника, газо- и воздухопроводов.
Газотурбинный двигатель со свободно-поршневым газовым генератором
На данный момент газотурбинные двигатели этой конструкции — самые перспективные для строительства автомобилей. Устройство представляет собой блок, объединяющий поршневой компрессор и двухтактный дизель. В средней части находится цилиндр с прямоточной продувкой, внутри которого располагается два связанных между собой специальным механизмом поршня. При схождении поршней происходит сжимание воздуха, и топливо воспламеняется. Сгоревшее топливо способствует образованию газов, которые при высокой температуре и давлении провоцируют расхождение поршней в стороны. Далее через выхлопные окна газы попадают в газосборник. Благодаря наличию продувочных окон в цилиндр проникает сжатый воздух, который способствует очищению от выхлопных газов и подготавливает двигатель к следующему циклу. После этого процесс повторяется.
| |||
| Сайт своими руками | ||
Отдохни на нашем сайте | Схема ГТД с центробежным компрессором | Странички истории | |
Странички на заметку | Примером использования этой схемы является двигатель ТА-8. Является вспомогательной силовой установкой(ВСУ), устанавливался на самолёте Ту-134A(Б). Как осевой компрессор сжимает воздух? В основе работы осевого компрессора(О.К.) лежит всё тот же принцип Бернулли, «чем больше скорость потока, тем меньше давление внутри этого потока», и наоборот, чем меньше скорость потока, тем больше давление внутри этого потока. | ||
Меню страницы | рис.1 Лопатки (Н.А.) предназначены для расчётного направления потока воздуха на лопатки (Р.К.) таким образом, чтобы на этих лопатках не возникал срыв потока воздуха, т.е., чтобы обтекание было ламинарным(см.рис2.лопатка3) гдеU- скорость потока воздуха, определяемая расходом, W-линейная скорость сечения пера лопатки, V-результирующая скорость потока воздуха, попадающего на лопатку рабочего колеса. Угол атаки потока воздуха имеет небольшой диапазон, внутри которого лопатка обтекается ламинарным потоком. Величина этого угла атаки зависит от многих факторов: от частоты вращения ротора компрессора, от расхода воздуха, проходящего через компрессор и определяющего осевую скорость воздушного потока, от давления воздуха и его температуры. При большом расходе воздуха, и низкой частоте вращения, угол атаки настолько мал, что на корытце рабочей лопатки возникает срыв потока воздуха(см. рис2, лопатка4). Турбулентный поток не пропускает весь расход воздуха через ступень, в результате чего компрессор «запирается»(см. рис2. лопатку4). | ||
рис.2 При небольшом расходе воздуха и значительной частоте вращения, результирующая скорость воздуха попадает на перо лопатки под большим углом атаки. В результате организуется срыв потока на спинке пера лопатки. Компрессор тоже «запирается». В результате такого «запирания», возникает явление, которое получило название помпаж. Компрессор не может пропустить через последние ступени расход воздуха, который он пропустил через первые ступени, а поступление его продолжается. Так как осевой компрессор является фактически трубой, без каких-либо перегородок, то при нерасчётных режимах работы компрессора, сжатый воздух начинает движение из зоны повышенного давления в зону пониженного, т.е. обратно на вход. Происходит хлопок. | |||
Перепускные клапаныИтак для того чтобы расход воздуха на выходе из двигателя соответствовал расходу на входе, на средних ступенях компрессора, по окружности, устанавливают перепускные клапаны. Обычно такую схему применяют на турбовинтовых двигателях. (см рис3) рис.3 Т.к. рабочий диапазон вращения ротора таких двигателей не велик, порядка 90-100%, то нет необходимости усложнять двигатель. 90% это как правило режим земного малого газа. В полёте частота вращения ротора постоянно 100%. Это делается из-за условия приёмистости двигателя. Т.к. винт очень массивен, и быстро раскрутить его до нужного режима не представляется возможным, то обороты двигателя сделали постоянными 100%, а режим работа задаётся рычагом УПРТ(управление положением рычага топлива). При даче газа подача топлива увеличивается при постоянных оборотах, а лопасти винта переставляются на больший угол атаки(винт догружается) за минимальное время. Для повышения газодинамической устойчивости турбореактивных двигателей и увеличения рабочего диапазона частот вращения, одних клапанов перепуска мало, применяют также поворотные лопатки В.Н.А.(входного направляющего аппарата), а также многовальную схему. Разберём вначале поворотные лопатки В.Н.А. | |||
Поворотные лопатки В.Н.А. От начала запуска и до определённых оборотов, поворотные лопатки Н.А. устанавливаются на отрицательный угол (-10гр на Д-30-3с, -30гр на Д-30-КУ), тем самым обеспечивая пониженный расход воздуха на передних ступенях компрессора и расчётный расход на последних ступенях. рис.4 | |||
Многовальная схема Третьим конструктивным противопомпажным мероприятием является многовальная схема двигателя. Чтобы пропустить больший расход воздуха через последние ступени сжатия, они должны вращаться с большей скоростью. Передние ступени компрессора насаживаются на ротор низкого давления (НД) со своей турбиной, а задние ступени устанавливаются на ротор высокого давления(ВД), тоже со своей турбиной. Причём если компрессор НД установлен перед компрессором ВД, то турбина НД установлена после турбины ВД (см. рис.5). рис.5 Такие двигатели обычно ставят на газоперекачивающих станциях. | |||
Какие двигатели ставятся на самолёт?Как уже говорилось выше, газотурбинный двигатель очень прожорлив. Чтобы снизить расход топлива, на двигатели стали устанавливать второй контур. Т.е. на входе в двигатель установили компрессор большего диаметра, способного пропускать через себя большие расходы воздуха. Пройдя этот компрессор, воздух стал разделяться на два потока: внешний(наружный) и внутренний(см.рис6) . Примером использования схемы с небольшой степенью двухконтурности является двигатель Д-30КУ. Устанавливается на самолёт Ту-154М и Ил-62М, модификация Д-30КП устанавливается на Ил-76. потока воздуха не взаимодействуют друг с другом, у каждого потока своё сопло, потоки имеют разные скорости, у потока внешнего контура меньшая скорость, а у внутреннего большая. За счёт большего массового расхода воздуха, 70% тяги двигателя создаётся внешним контуром и лишь 30% внутренним, хотя скорость потока в нём и больше. Двигатели с камерой смешения(см.рис8) имеют одно сопло. Примером использования схемы со смешением потоков может служить двигатель ПС-90. Устанавливается на самолёты Ту-214, Ил-96. Воздух поступающий из внешнего контура эжектируется потоком газа внутреннего контура, приобретая на срезе сопла двигателя дополнительную скорость. Тяга таких двигателей выше, чем у двигателей без камеры смешения, но у них больше вес. Компромисс находится для каждого двигателя индивидуально, ещё одна золотая середина, коих при проектировании самолёта, великое множество. | |||
Какие двигатели ставятся на вертолёт? На современные вертолёты, как и на самолёты, устанавливаются газотурбинные двигатели, но они несколько отличаются от самолётных.Связано это с тем, что на вертолёте установлен неcущий винт большого диаметра, частота его вращения порядка 100-150об/мин несоизмерима с частотой вращения ротора двигателя, равной ~ 30000об/мин.
Чтобы редуцировать такие обороты, редуктор несущего винта должен быть больших размеров и, как следствие, большого веса. Газовоздушная смесь, отдав часть своей энергии на турбину компрессора, полностью срабатывает свою энергию на лопатках свободной турбины, а оставшийся выхлоп выводится в расширяющееся сопло, направленное вбок от оси двигателя. Обороты свободной турбины значительно меньше оборотов ротора двигателя, а отсюда и входной вал редуктора НВ вращается с оборотами соизмеримыми с оборотами выходного вала, т.е. НВ. , так и через свободную турбину, установленную сзади двигателя и передающую вращение винту через вал, проложенный внутри вала ротора компрессора. В военной авиации используются двигатели с форсажной камерой, позволяющей резко повысить тягу двигателя на некоторое время. Примером является двигатель АЛ-31Ф, установленный на самолёт Су-27 всех модификаций. Смысл форсажной камеры в том, что в газовоздушной смеси реактивной струи, находится ещё достаточно воздуха в котором может гореть топливо. При этом поднимается температура выходящих газов, растёт энергия струи. В сужающемся сопле происходит её расширение и увеличение скорости, а отсюда и тяги. Общий расход топлива, при этом, гигантский, но это уже не в счёт. Сопла на таких двигателях делают регулируемыми, как по диаметру среза сопла, так и по углу отклонения вектора тяги. Такие двигатели существенно улучшают летные характеристики истребителей. | |||
Как запускаются газотурбинные двигатели? Сразу хочу отметить, что запуск газотурбинного двигателя, это довольно энергоёмкий процесс, тем самым я предваряю, возникающие по этому поводу вопрос, почему нельзя запускать сразу все двигатели на самолёте. А сейчас вы сможете посмотреть небольшой фильм о газодинамических процессах, происходящих внутри двигателя. Приятного просмотра. | |||
Анекдот в студию!!! | Если у Вас возникнут какие-либо вопросы, добро пожаловать на форум, или в форму обратной связи Copyright © Владимир Глухов 2010 | ||
Русифицированная версия скрипта Commentics | |||
Выходное устройство газотурбинного двигателя
ЦЕЛЬ РАБОТЫ: изучение конструкции и назначения выходного устройства ГТД.
Выходное устройство — часть двигателя, расположенная за силовой турбиной и предназначенная для отвода газов из ее проточной части.
Оно должно иметь минимальное гидравлическое сопротивление, обладая при этом высокой стойкостью против коробления, прогара и газовой коррозии.
Выходное устройство состоит из наружного и внутреннего оболочек, соединенных стойками. Внутренний конус-обтекатель служит для предотвращения резкого расширения газа за турбиной и плавного перехода потока из кольцевого сечения за турбиной в сплошное за конусом.
Выходное устройство также является элементом силовой схемы ГТУ и служит задней опорой ротора силовой турбины.
На наружном корпусе выходного устройства имеются:
штуцера для подвода масла к подшипникам и для его отвода;
электрические разъемы для снятия сигнала от индуктивных датчиков частоты вращения ротора силовой турбины, размещенных во внутреннем конусе;
фланцами для отбора горячих газов.
Угол внутреннего конуса у вершины составляет 30-50 0. Устойчивое разряжение вокруг конуса использовано для организации воздушного охлаждения размещенных в нем подшипников ротора силовой турбины.
К заднему фланцу наружной обечайки корпуса выходного устройства крепится поворотный патрубок, который может монтироваться как при правом, так и левом варианте установки двигателя.
Детали конструкции выходных устройств работают в условиях обтекания химически активными газами при высокой температуре, достигающей 900 — 1000 К. Поэтому для изготовления деталей выходного устройства используются жаропрочные нержавеющие стали типа 1Х18Н9Т, 0Х18Н12Б или титанового сплава.
Порядок выполнения работы
1. Изучение конструкции и назначения выходного устройства газотурбинного двигателя.
2. Эскизирование выходного устройства ГТД и определение его основных геометрических параметров.
Контрольные вопросы
1. Для чего служит выходное устройство ГТД?
2. Какие требования предъявляются выходным устройствам ГТД?
3. Из каких материалов изготавливаются элементы выходных устройств?
Лабораторная работа №10
Конструктивные схемы газотурбинных двигателей
ЦЕЛЬ РАБОТЫ: изучение расположения основных узлов ГТД и их силовой взаимосвязи.
Основные неподвижные элементы ГТД, воспринимающие силы и моменты, возникающие в процессе работы двигателя, образуют его силовую схему. В ее состав входят корпуса компрессора, камеры сгорания, турбин, корпуса входного и выходного устройств и опор подшипников.
При работе ГТД на силовые корпуса действуют газодинамические силы, силы инерции и тяжести. Поэтому к нему предъявляются повышенные требования в отношении прочности и жесткости.
Газодинамические силы возникают во входном устройстве, при обтекании лопаток направляющих и сопловых аппаратов компрессора и турбины. Величина газодинамических сил пропорциональна массе воздуха или газа, протекающих по проточной части турбомашин в единицу времени, и разности скоростей потока на соответствующих участках. Вектор газодинамических сил направлен под углом к оси двигателя.
Силы, возникающие на направляющих лопатках компрессора и на диффузорном участке камеры сгорания, направлены в сторону входного устройства ГТД.
Силы, возникающие на лопатках сопловых аппаратов турбин, направлены в сторону выходного патрубка.
Осевые силы вызывают напряжения растяжения или сжатия в силовых корпусах ГТД.
Окружные составляющие сил, действующие на корпуса, создают крутящий момент, который также воспринимает судовой фундамент.
Число узлов крепления ГТД к судовому фундаменту определяется размерами двигателя, величиной и характером действующих нагрузок.
Неравномерность полей скоростей и давлений газового потока вызывают вибрации силовых корпусов, что негативным образом сказывается на ресурсе и надежности ГТД.
Окружные составляющие газодинамических сил определяют величины крутящих моментов, действующих в рабочих колесах компрессора и турбин.
Осевые составляющие сил, действующие в компрессоре и турбинах, направлены в противоположные стороны. Поэтому соединение роторов компрессора и турбины позволяет уменьшить нагрузку, действующую на радиально-упорный подшипник.
Равнодействующая всех осевых сил, воздействующая как на корпуса, так и передаваемая роторами через радиально-упорные подшипники, воспринимается через узлы крепления ГТД судовым фундаментом.
Количество радиально-упорных подшипников равно числу роторов.
В вертолетных и танковых ГТД , применение которых наиболее вероятно на судах речного флота, используют как двухроторную, так и трехроторную схемы.
В двигателях, выполненных по двухроторной схеме, например в двигателях типа ТВ3-117, применяют два радиально-упорных подшипника. Один из них устанавливают на задней цапфе ротора компрессора, в корпусе опоры, расположенной между компрессором и камерой сгорания.
Второй радиально-упорный подшипник устанавливают на вале силовой турбины за ее второй ступенью, в корпусе выходного устройства.
В этой схеме ротор компрессора и турбины его привода имеют еще два радиальных подшипника. Один из них расположен во входном устройстве, а второй — в корпусе опор, расположенном между турбиной привода компрессора и силовой турбиной.
Радиальный подшипник силовой турбины расположен также в корпусе выходного устройства.
В трехроторных схемах , в которых имеется компрессоры низкого и высокого давления и соответствующие турбины для их привода, радиально-упорные подшипники расположены между компрессорами. Каждый из этих роторов имеет еще по два радиальных подшипника.
Силовая турбины, как и в предыдущем случае, имеет два подшипника, один из которых выполняют радиально-упорным.
Порядок выполнения работы
С помощью чертежей, технической документации и узлов двигателя ТВ3-117 определить корпуса, входящие в его силовую схему.
Определить положение радиальных и радиально-упорных подшипников.
Определить направление осевых и окружных составляющих сил, действующих на корпусы и роторы компрессора и турбин.
Выполнить схематический чертеж двигателя.
Контрольные вопросы
Какие узлы входят в силовую схему ГТД?
Какие силы действуют на корпуса и роторы ГТД?
На какое количество подшипников опираются роторы компрессора и турбин?
Где расположены радиально-упорные подшипники роторов?
Список рекомендованной литературы
Артемов Г.А. Совершенствование судовых газотурбинных установок. Л.: Судостроение, 1984, 230 с.
Жаров Г.Г., Венцюлис Л.С. Судовые высокотемпературные газотурбинные установки. Л.: Судостроение, 1973.
Масленников М.М., Шальман Ю.И. Авиационные газотурбинные двигатели. М.: Машиностроение, 1975
Маслов Л.А. Судовые газотурбинные установки. Л.: Судостроение, 1973.
Справочник инженера-механика судовых газотурбинных установок. /Под ред. В.Д. Речистера. Л.: Судостроение, 1985
2.3. Устройство гтд
Схема конструкции газотурбинного двигателя судовой установки ГТУ — 20 мощностью 8700 кВт приведена на Рис. 30.
|
Рис. 30. Схема судового газотурбинного двигателя легкого типа |
Компрессор высокого давления приводится во вращение турбиной высокого давления, компрессор низкого давления — турбиной среднего давления (вал проходит внутри вала КВД — ТВД). Турбина винта вырабатывает полезную мощность, которая через рессору 13 и редуктор 14 передается винту. Все три турбины имеют различную частоту вращения. Для передачи мощности от пусковых электродвигателей и для привода навешенных вспомогательных механизмов служат передняя 2 и основная 3 коробки приводов. Маслоагрегат 15 также получает энергию от вала компрессора. Все элементы ГТД смонтированы на общей раме 16. Окружающий воздух эжектируется уходящими газами и, проходя между кожухом и корпусом двигателя, охлаждает эти элементы.
2.4. Гту со свободнопоршневым генератором газа
Двухтактный ДВС совместно с поршневым компрессором образует так называемый свободнопоршневой генератор газов -СПГГ, который снабжает газовую турбину рабочим телом (газами) с высокими значениями давления и температуры. Такой комбинированный двигатель, схема которого изображена на Рис. 31 позволяет в области высоких значений температур и давлений, использовать поршневой агрегат, а в области низких давлении и больших расходов — газовую турбину.
|
Рис. 31. Схема газотурбинного двигателя со свободнопоршневым генератором газа |
Принцип действия ГТУ с СПГГ заключается в следующем. Воздух сжимается в компрессоре 2 и подается в воздушную емкость 3, откуда попадает в цилиндр дизеля 4. Поршни компрессора жестко соединены с поршнями дизеля, которые движутся в разные стороны и образуют в средней части цилиндра камеру сжатия. Кинематической схемой синхронизируется движение поршней. Топливо подается в цилиндр через форсунку 5. Рабочий процесс совершается за два хода поршня, как и в двухтактном ДВС. После совершения рабочего хода поршни сходятся под действием работы сжатого воздуха, находящегося в воздушной буферной ёмкости 1. Газы из цилиндра попадают в газовую турбину 6, которая, через редуктор 7 передает крутящий момент на движитель 8, и после расширения в турбине удаляется в атмосферу.
2.5. Компрессоры Назначение, классификация
Компрессором называют машину, предназначенную для повышения давления газа и для его перемещения за счет подведенной механической энергии.
По принципу действия компрессоры разделяют на лопаточные (турбокомпрессоры) и объемного действия. В лопаточных компрессорах давление рабочей среды повышается за счет преобразования подведенной механической энергии от вращающихся рабочих лопаток к потоку воздуха (газа) движущемуся в межлопаточных каналах. В компрессорах второго типа давление повышается за счет уменьшения объема, занимаемого воздуха (газа), под действием перемещающейся детали, например поршня.
По конструктивному исполнению компрессоры различают на: центробежные, осевые и комбинированные.
Объемные компрессоры в зависимости от характера движения рабочего органа делятся на поршневые и ротационные.
По параметрам компрессоры характеризуются производительностью — массовой или объемной:
— степенью повышения давления;
— скоростью перемещения рабочих органов — частотой вращения ротора или скоростью движения поршня.
По назначению различают компрессоры газотурбинных двигателей, компрессоры наддувочных и продувочных агрегатов.
Компрессоры судовых ГТУ должны отвечать следующим требованиям: создать необходимую степень сжатия при возможно большем к. п. д.; подать в камеры сгорания непрерывный поток воздуха; быть всережимными; то есть иметь как можно меньшую чувствительность к изменениям режимов работы от пуска до полного хода. Этим требованиям больше всего удовлетворяют осевые и центробежные компрессоры. Оба типа компрессоров относятся к классу ротативных лопаточных машин. В осевом компрессоре сжатие потока движется параллельно оси, в центробежном — от центра к периферии.